FANUC CNC machines are automated tools used to cut, drill, and shape metal and other materials with high precision.
These machines have been an integral part of many industrial factories since 1974, known for their yellow casing and reliable performance.
Although FANUC excels at the cutting itself, the real bottleneck often happens around the machine. Loading parts, waiting for cycles to complete, and manually transferring materials between operations can eat up significant amounts of your total production time.
This article covers FANUC's key features, real-world benefits, practical use cases, and compares it to affordable robotic automation alternatives for modern manufacturers.
What is a FANUC CNC machine?
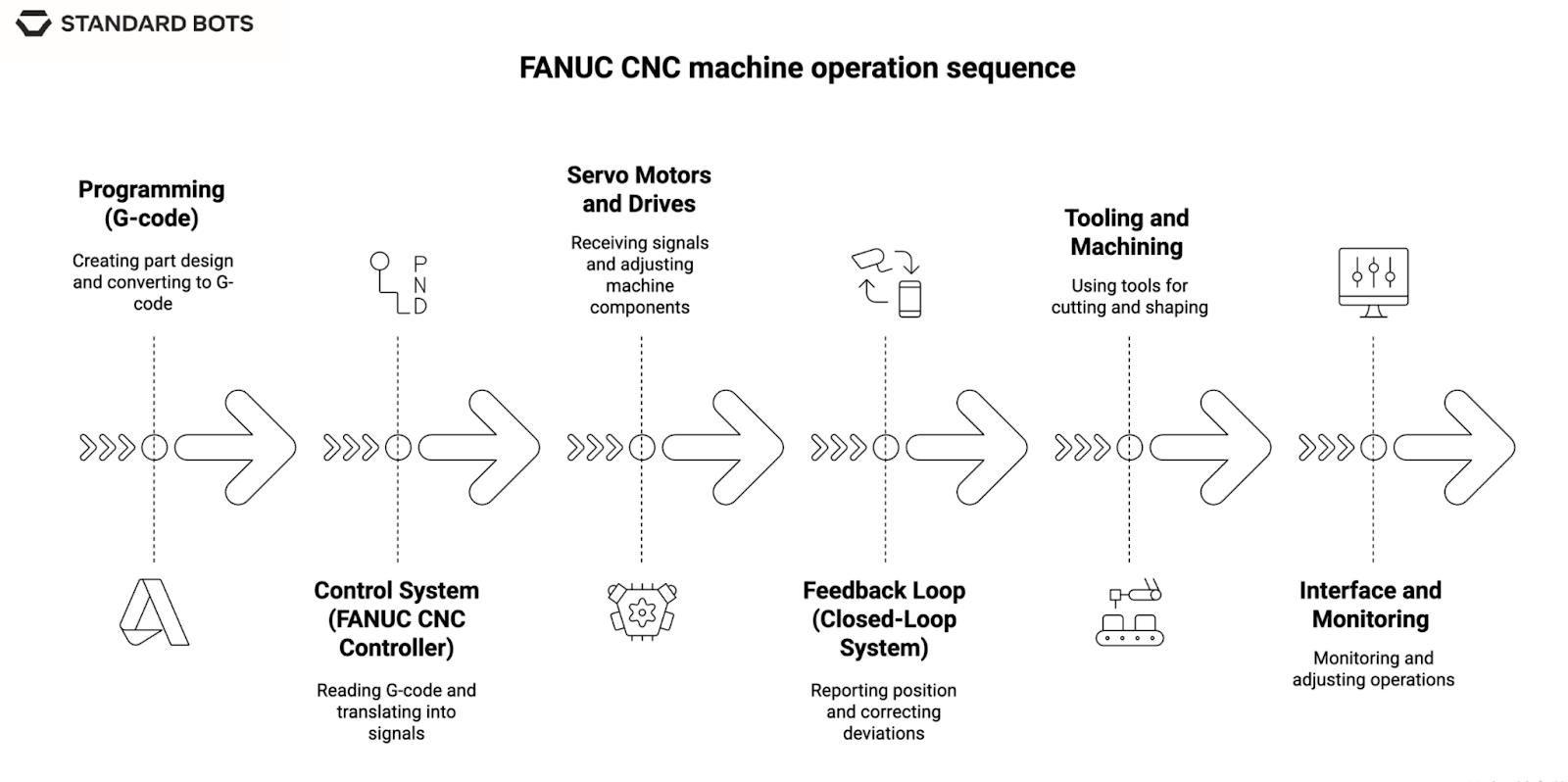
FANUC is a leading global provider of CNC systems, industrial robots, and factory automation solutions. FANUC CNC systems are widely used in machine tools for precision machining and automation.
Even though the machine itself might be made by brands like Haas, DMG Mori, or Mazak, it’s often a FANUC controller under the hood interpreting G-code and directing the motors, spindles, and tooling.
Today, FANUC controls about 65% of the CNC controller market, worldwide. If CNC machines were cars, FANUC would be the most popular engine manufacturer.
You’ll find FANUC especially common in automotive plants, where its systems manage everything from drivetrain machining to thermal management components. Over time, the yellow FANUC box has become a symbol of industrial-grade reliability and precision.
Key features of FANUC CNC machines
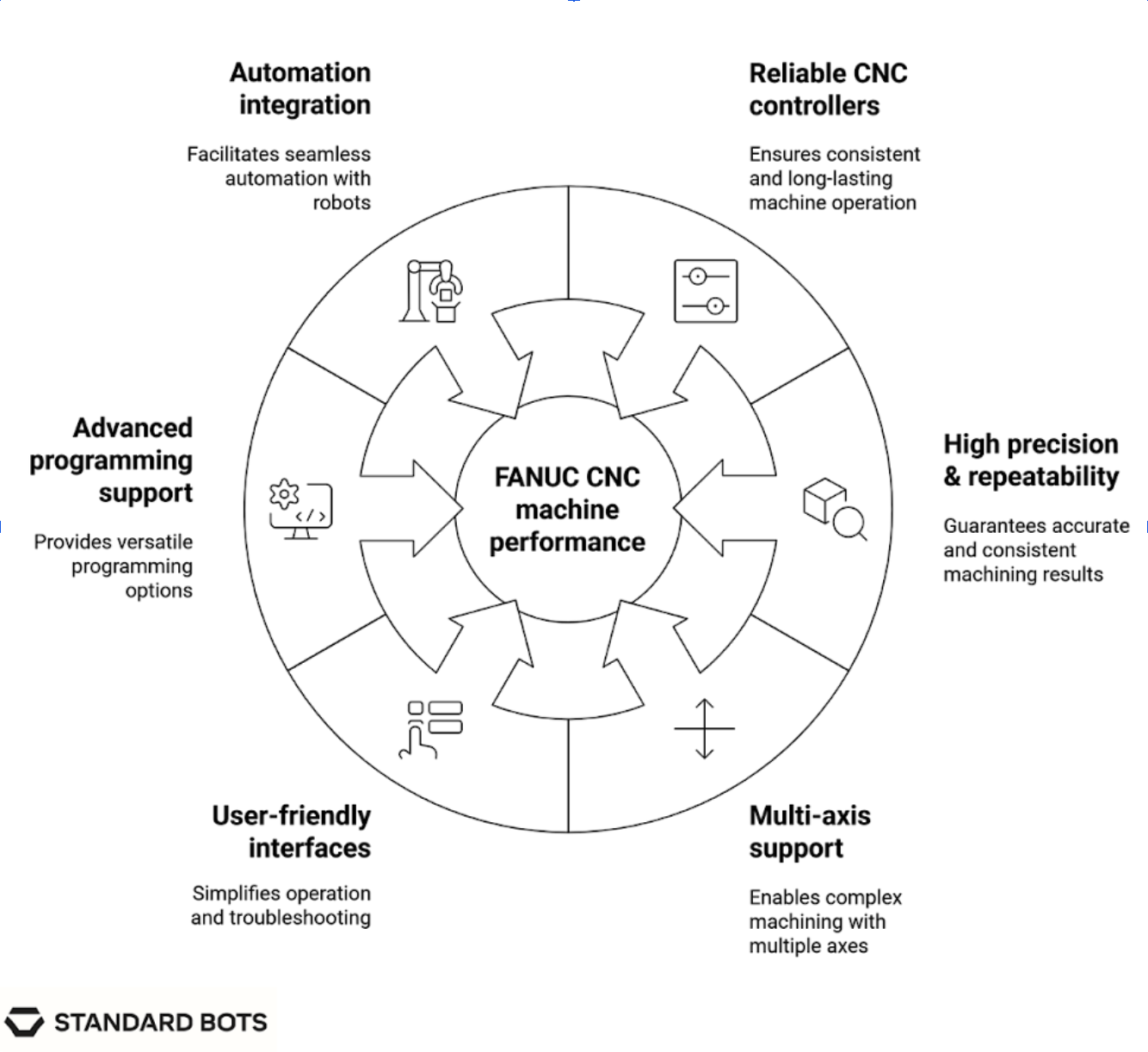
- Reliable CNC controllers: FANUC’s Series 0i and 30i controllers are the backbone of countless manufacturing floors. The 0i handles basic operations with rock-solid reliability, while the 30i powers advanced multi-axis and high-speed jobs. These controllers are known for longevity, because many 20-year-old FANUC systems are still in service. FANUC’s newest 0i-D/F and 0i-F Plus controllers are built to last. In factory testing, the average time before one of these systems would fail is more than 47 years for the 0i-D/F and over 52 years for the 0i-F Plus. This means these controllers are among the most durable and reliable in the entire industrial automation industry.
- High precision and repeatability: FANUC CNC systems can support precision of ±0.001 mm, tight enough that your part matches your CAD file on the first try. That accuracy is the difference between reworking parts and shipping finished goods. Thermal compensation ensures reliability even during long runs, which matters most in aerospace and medical manufacturing, where microns mean money.
- Multi-axis support: FANUC controllers manage 32+ axes at once (depending on the model), making them ideal for 5-axis machining and turn-mill centers. What once required multiple setups, like roughing, finishing, and drilling a turbine blade, can now run in a single cycle. The system keeps all axes moving in sync, eliminating jerkiness and preserving surface quality.
- User-friendly interfaces and diagnostics: FANUC’s touchscreen interfaces are designed for clarity. Instead of cryptic error codes, diagnostic screens show what went wrong and how to fix it. Built-in help and alarm histories walk operators through each issue, while guided prompts reduce guesswork during setup and troubleshooting.
- Advanced programming support: FANUC supports both G-code and macro programming for full control over machining. Macro B lets you automate repetitive tasks, turning 50 lines of code into 5. Conversational modes help operators build programs without deep G-code knowledge. The system also supports CAM imports from Mastercam or Fusion 360.
- Automation integration with FANUC robots: FANUC robots and CNC controllers speak the same language, which makes automation easier to deploy. A FANUC robot can load, position, and unload parts between machining cycles without any custom coding. For high-volume production, this tight coordination shortens cycle times and eliminates handoffs that typically cause delays or errors.
Common use cases & industries
- Automotive manufacturing: Plants run FANUC machines to produce engine blocks, transmission cases, and brake components. Repeatability ensures identical parts meet tight tolerances, which is critical with high-volume production.
Example: BMW uses FANUC robots in engine and body production lines to increase uptime and maintain consistent quality across its global factories. - Aerospace manufacturing: Companies like Boeing use FANUC systems across multiple global sites. Identical G-code runs on machines from Seattle to South Carolina, helping meet traceability and compliance requirements for flight-grade components.
Example: Triumph Aerospace (via Microtrol Engineering) upgraded Cincinnati Milacron machines using FANUC CNC controls. This upgrade reduced processing times, minimized errors, and improved production for precision aerospace parts.
- Medical device manufacturing: FANUC’s precision and thermal compensation support the production of surgical tools and titanium implants. Dimensional stability is crucial during long runs, where minor errors can lead to costly scrap.
Example: MIP (Manufacturers of Injection Precision) uses FANUC CNCs to power a 12-axis machine producing high-precision tool parts. This process increased productivity by more than 300% and demonstrates FANUC’s role in precision and medical tooling.
- Electronics manufacturing: FANUC handles smartphone cases, laptop housings, and heat sinks with high surface finish requirements. Multi-axis support enables complex geometries in fewer setups, improving throughput and quality in consumer electronics production.
Example: Foxconn has used FANUC CNCs to manufacture iPhone components, including aluminum casings. FANUC CNCs have helped Foxconn meet Apple’s strict tolerance and quality standards.
Real-world applications of the FANUC CNC machine
Tier 1 automotive suppliers commonly use FANUC-controlled 5-axis machines to manufacture complex aluminum components, including engine blocks with integrated cooling channels. The advanced capabilities of 5-axis CNC machining allow for complex internal geometries to be handled in single operations, significantly reducing cycle times and improving dimensional accuracy.
In aerospace, companies like Spirit AeroSystems use advanced CNC tech to machine carbon fiber wing components. These systems are configured for advanced composite cutting, where macro programming manages delicate fiber paths without causing delamination. Spirit AeroSystems has established itself as the world's largest user of AFP technology with 17 automated fiber placement machines.
High-volume vs. prototyping applications
FANUC excels in high-volume production, where consistency drives profitability. Automotive plants rely on FANUC systems to run identical programs for months at a time with minimal intervention. This makes them ideal for second and third-shift operations, where unattended machining reduces labor costs and downtime.
For prototyping and low-volume work, FANUC systems can be overkill. Shops producing one-off parts often find the programming and setup less intuitive compared to lighter platforms. That said, many manufacturers still prefer FANUC when moving from prototyping to production, since the same programs scale easily without rewriting code.
Benefits of using a FANUC CNC machine
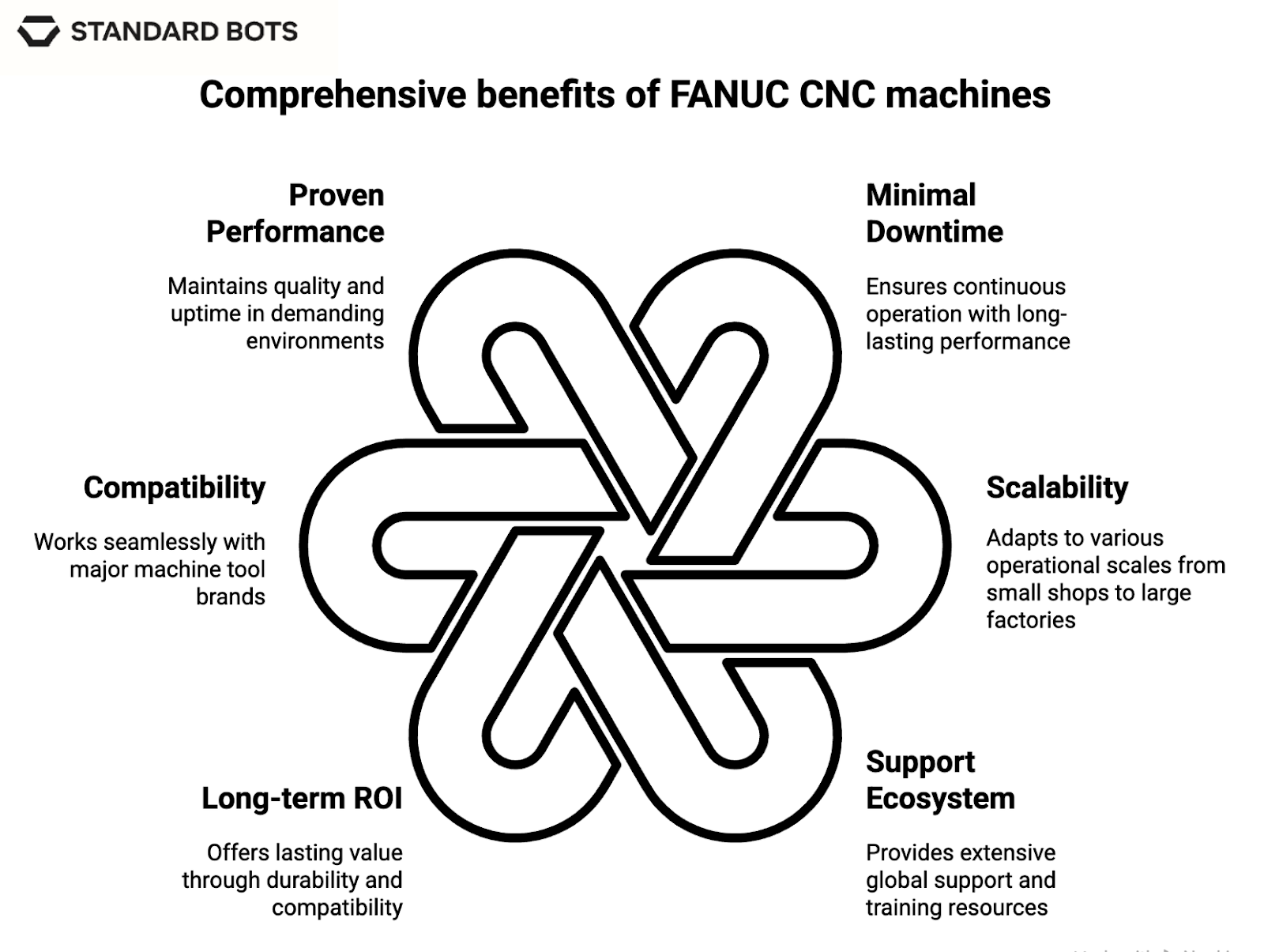
- Minimal downtime: FANUC controllers are built for exceptional reliability (with 52-year MTBF ratings) and can run for years without major failures. When issues do arise, the systems provide direct fault codes that make troubleshooting fast and accurate. This reduces downtime and gets production back online quickly.
- Scalability from small shops to full-scale factories: FANUC controllers perform equally well on a single machine or in large factories across industries. For example, job shops using FANUC‑equipped systems have expanded from one machine to several without changing their control platform, making automation upgrades more straightforward.
- Massive support ecosystem and training availability: FANUC maintains a global network of technicians, training centers, and support teams. Its 24/7 support line is staffed by engineers with deep product knowledge, including weekends and holidays. Training programs are widely available through community colleges, trade schools, and FANUC-owned facilities, many of which offer hands-on courses.
- Long-term ROI through durability: Even when mechanical parts wear down after 15 to 20 years, most controllers can be migrated to new equipment without compatibility issues. G-code written in the 1990s still executes on modern FANUC platforms, protecting long-term programming investments. Compared to proprietary systems that require frequent software updates or hardware replacements, FANUC minimizes the total cost of ownership over time.
- Compatibility with almost every major machine tool brand: FANUC supports a broad range of machine tool brands, including DMG Mori. In practice, manufacturers frequently run Haas and Mazak machines side by side on FANUC controllers. The similarity in programming standards allows operators to move between these brands with minimal adjustment.
- Proven performance in real-world conditions: Manufacturers in aerospace and other demanding industries operating around the clock rely on these systems to maintain quality and uptime without surprises.
Best alternatives to FANUC CNC machines: TL;DR
1. RO1 by Standard Bots
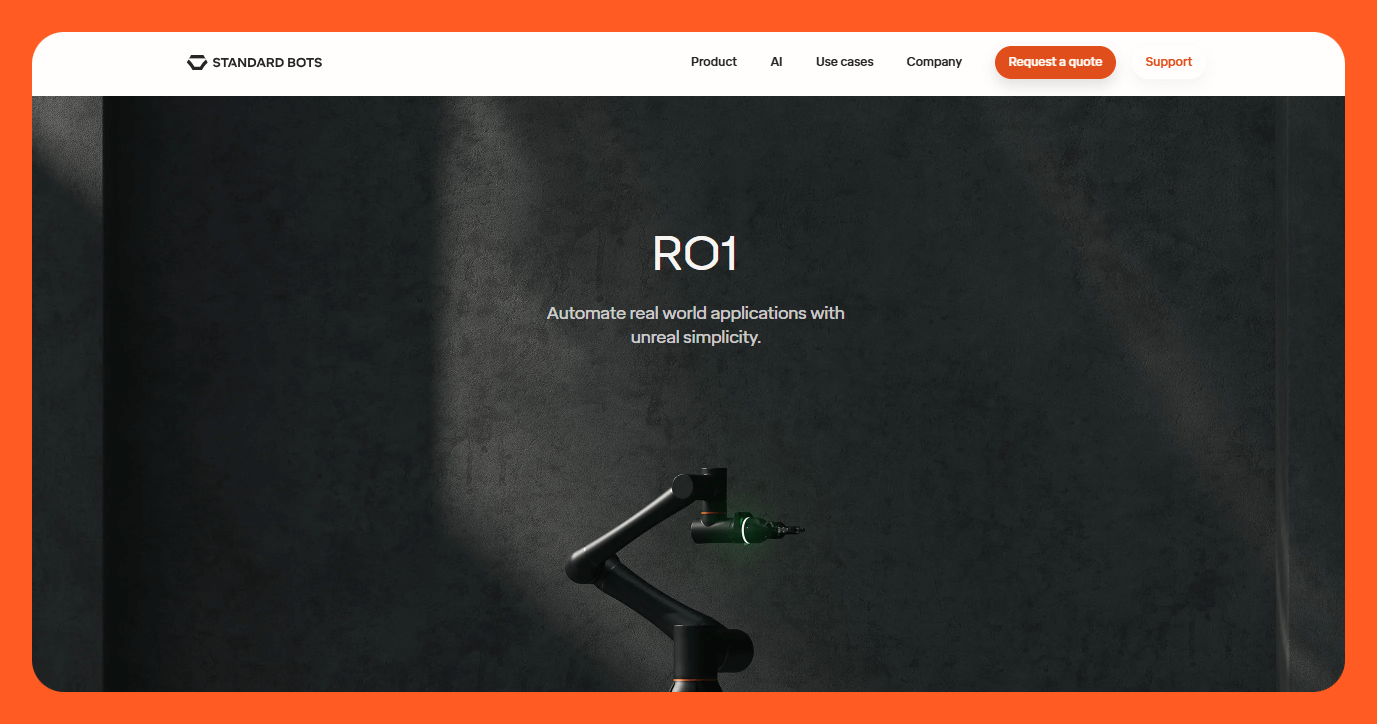
Standard Bots' RO1 brings automation without the complexity. Built for easy compatibility with FANUC CNC machines, it handles material movement while the CNC handles cutting and shaping. RO1 offers robust hardware specs like an 18 kg payload, 1300 mm reach, ±0.025 mm repeatability, and a built-in 3D vision system.
It features a collaborative design with collision detection, ensuring safety in shared workspaces. Programming is beginner-friendly with a no-code touchscreen interface and drag-and-drop routine creation, making it accessible even to those with no robotics background. Operators can get up and running in hours, while advanced functions take just a day or two to master.
RO1 connects effortlessly via direct I/O or Ethernet, supports plug-and-play with FANUC controllers, and works out of the box with OnRobot grippers. With a linear speed of 3 m/s and reliable 24/7 operation, it ensures both precision and endurance on the shop floor.
Ideal use cases: CNC machine tending, pick and place operations, palletizing, perfect for shops wanting to automate existing FANUC machines without replacing proven equipment.
2. Siemens
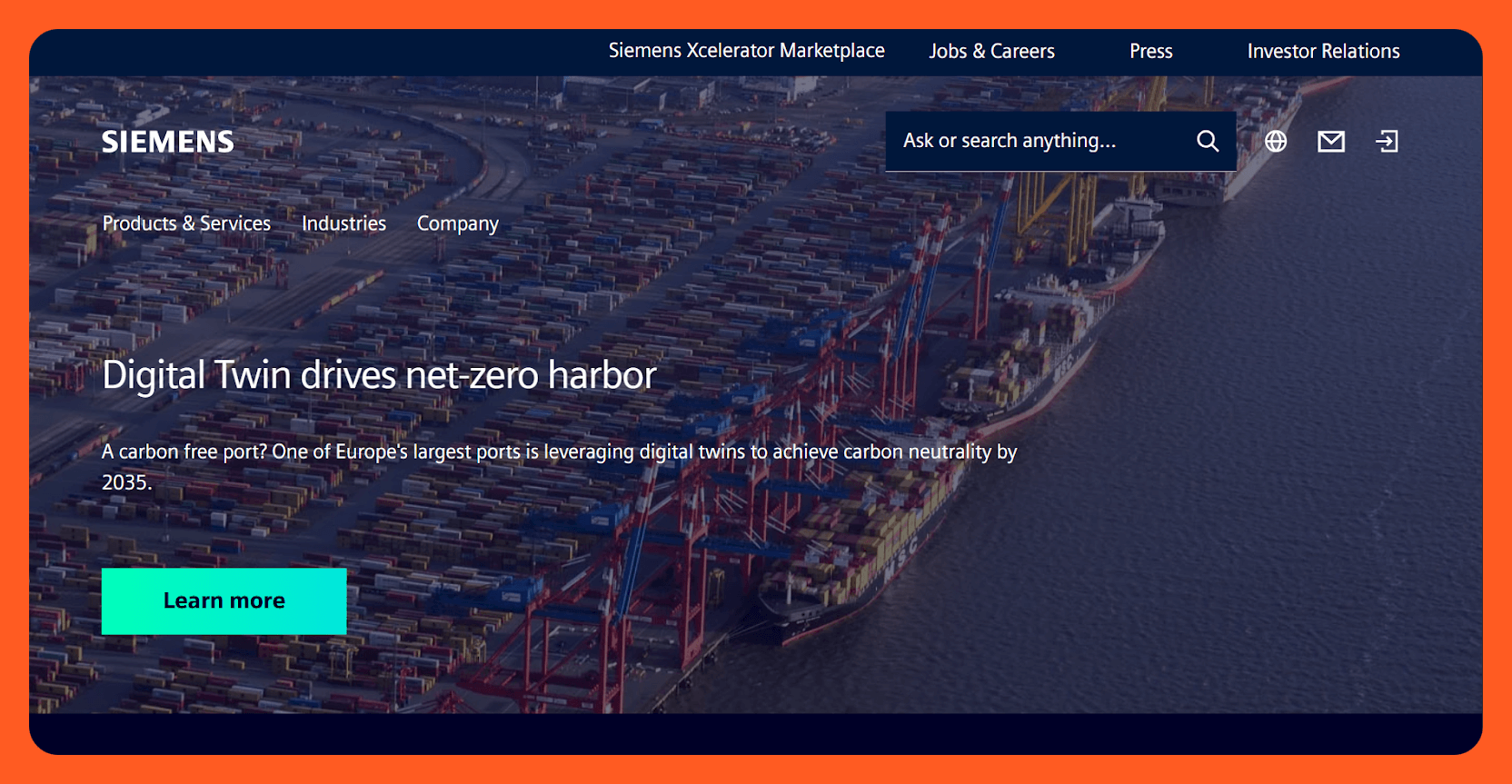
Siemens Sinumerik CNC systems are known for their great UI, powerful controllers, and dominance across European markets. They support up to 31 axes with high-speed processing and advanced servo tech, enabling complex multi-spindle setups.
The Windows-based HMI makes operation intuitive, and ShopMill/ShopTurn provides conversational programming for easier setup. For advanced users, it includes 3D simulation, CAD/CAM integration, and macro programming. Connectivity is extensive with Ethernet, OPC UA, and MindSphere IoT support coming standard, along with wide third-party compatibility.
Performance is top-tier, offering sub-micron precision, look-ahead processing, thermal compensation, and superior surface finishes on intricate parts. However, its steep learning curve demands 2 to 4 weeks of training for operators and significant programming knowledge to unlock its full potential.
Ideal use cases: High-precision machining, complex 5-axis applications, European OEM machines, advanced manufacturing requiring sophisticated programming features.
3. Haas
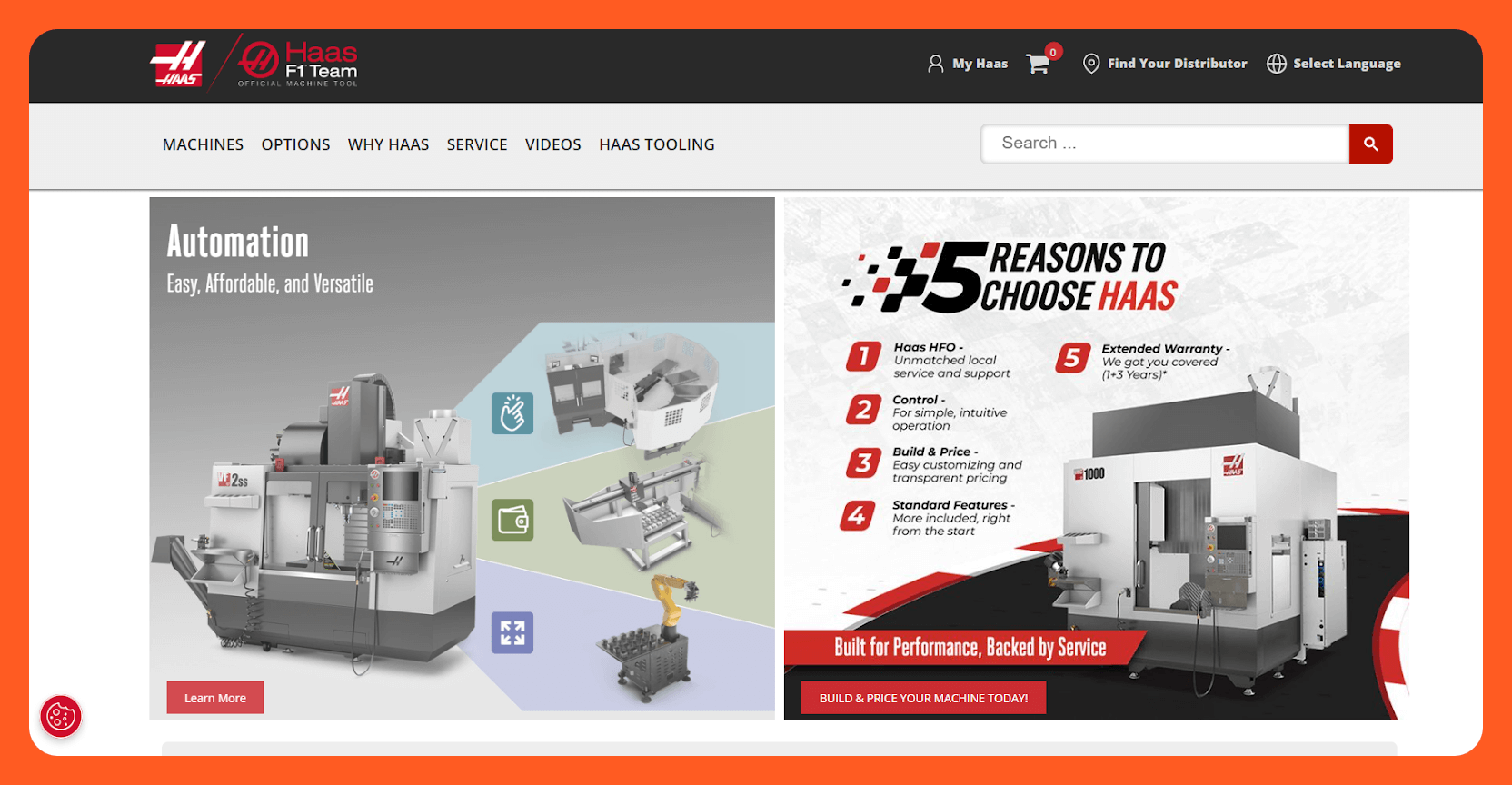
Haas CNC systems are a popular choice for U.S. shops looking for affordability and ease of use. The controls are straightforward and significantly more budget-friendly than FANUC. Hardware capabilities include basic to intermediate multi-axis support and solid servo performance, ideal for simpler machining tasks.
Programming is accessible with standard G-code and Haas’ Visual Quick Code (VQC) for conversational programming. While simulation tools are basic, they’re enough for most standard jobs.
Connectivity includes standard networking options, though IoT and advanced data tracking are limited. In terms of performance, Haas offers reliable repeatability and machining quality for everyday use, though it lacks the precision needed for complex geometries or high-end surface finishes.
Most operators can become proficient within 1 to 2 weeks, especially those already familiar with G-code. Extensive learning resources are also readily available through Haas Technical Education Centers.
Ideal use cases: General machining, prototype work, small to medium job shops, training environments, cost-conscious operations not requiring advanced features.
4. Heidenhain
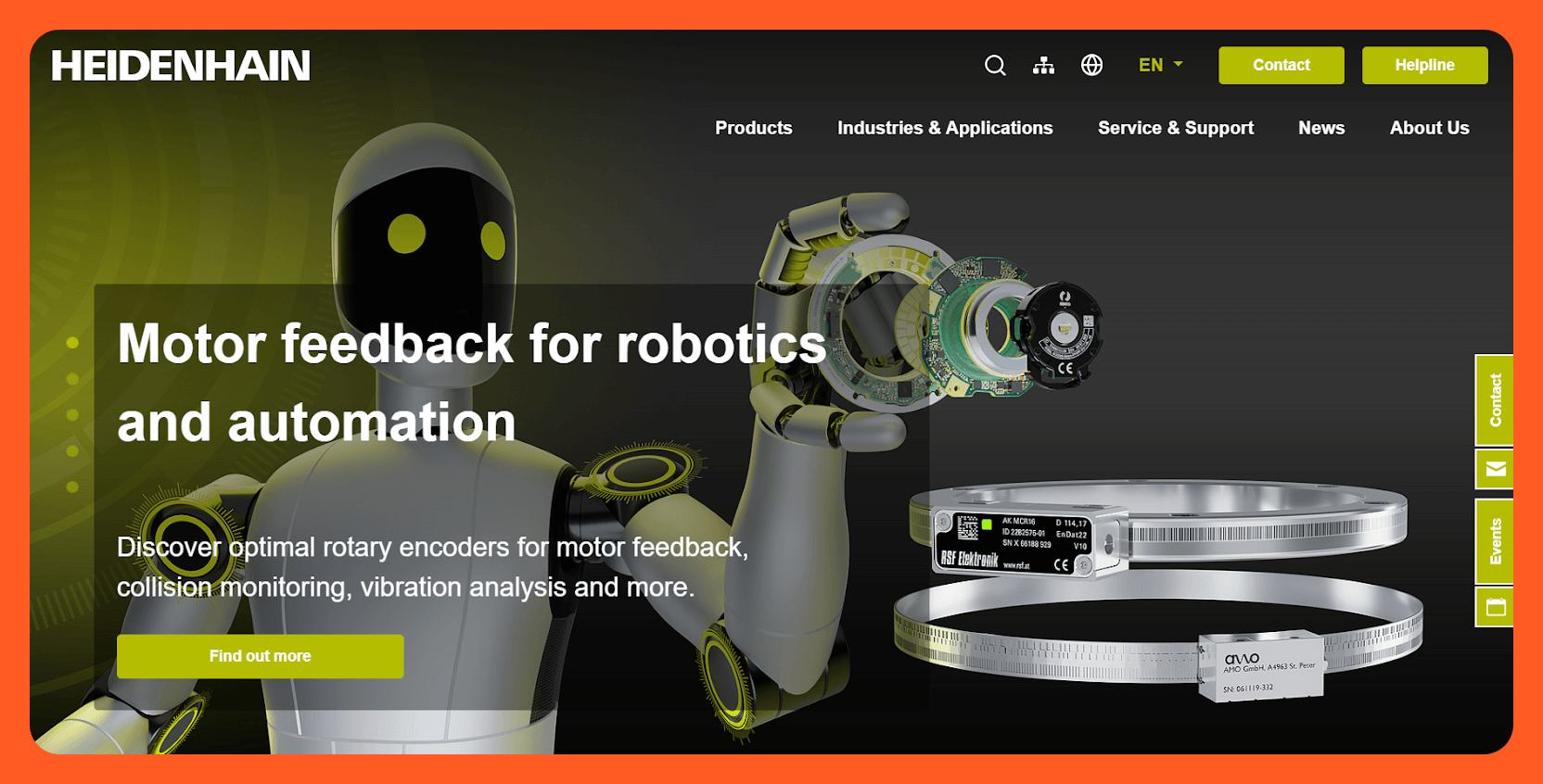
Heidenhain controllers are a go-to for high-end 5-axis milling and applications that demand ultra-precise surface machining.
Built in Germany, these systems offer advanced multi-axis control, high-resolution encoders, and excellent thermal stability, making them ideal for demanding environments. The software stands out with powerful conversational programming, advanced cycle programming, intuitive tool management, and top-tier graphical interfaces.
While integration is solid with standard Ethernet connectivity, Heidenhain focuses more on machining precision than on IoT features. Performance is unmatched for 3D contouring and surface finishes, aided by high-speed look-ahead motion control.
However, full operator proficiency typically requires 3 to 4 weeks of training, along with a solid grasp of advanced machining concepts. Training centers are also less widespread in North America.
Ideal use cases: Tool and die work, aerospace components, medical device manufacturing, mold making, any application requiring exceptional surface quality and complex 5-axis machining.
Summing up
FANUC CNC machines continue to set the benchmark for precision, uptime, and industrial compatibility. From small job shops to global manufacturing giants, their controllers power some of the most demanding production lines in the world.
But they’re not the only option. For teams focused on high-mix automation, RO1 offers a simpler path to lights-out operation without complex programming. Likewise, brands like Haas and Siemens cater to different needs, from affordability to advanced control.
So, whether scaling up or upgrading, choosing the right system depends on the parts being made, the team running them, and the ROI that matters most.
Next steps with Standard Bots
Looking for a smarter alternative to FANUC CNC machines? RO1 by Standard Bots is built for modern shop floors that need performance, precision, and simplicity, all at a fraction of the usual cost.
- Affordable and adaptable: Costs half as much as traditional cobots, with a list price of $37K.
- Precision and power: Repeatability of ±0.025 mm and an 18 kg payload make it perfect for handling real work, from pick-and-place to tool changes and more.
- AI-driven simplicity: RO1 optimizes as it runs, cuts down cycle times, and learns without being told twice.
- Safety-first design: Collision detection and machine vision let RO1 work right next to your team — no cages, no problem.
Schedule your risk-free, 30-day on-site trial today and see what fast, flexible automation actually looks like.
FAQs
1. What's the difference between FANUC and other CNC controllers?
The biggest difference between FANUC and other CNC controllers is their focus and strengths. FANUC is known for its reliability, ease of use, and strong global support network, making it popular in industries like automotive and aerospace. On the other hand, Siemens is recognized for its powerful features, open architecture, and flexibility, often favored for high-end, complex applications.
2. Are FANUC CNC machines worth the higher cost?
Yes, FANUC CNC machines are generally considered worth the higher cost due to their reputation for reliability, ease of use, and suitability for various industries. The upfront cost pays for itself through minimal downtime, longer equipment life, and lower total cost of ownership. However, the higher initial cost may be a barrier for some businesses, particularly those with tighter budgets or specific custom needs.
3. How hard is it to learn FANUC programming?
Learning FANUC programming is challenging but manageable, especially for those with prior coding experience and access to quality training. The early learning curve can feel steep, particularly for users new to robotics or CNC systems. Structured training is also widely available through community colleges, technical institutes, and FANUC’s dedicated training centers.
4. Can I automate my existing FANUC CNC machine?
Yes, and it's often more cost-effective than buying new automated equipment. Solutions like Standard Bots' RO1 can handle loading, unloading, and tending existing FANUC machines for around $37K, much less than replacing proven equipment. FANUC's built-in I/O makes integration straightforward with most automation systems.
5. What industries benefit most from FANUC CNC machines?
The industries that benefit the most from FANUC CNC machines are the automotive, aerospace, and medical manufacturing industries. This is due to FANUC's precision and reliability requirements. Any industry needing high-volume production, tight tolerances, or 24/7 operation will appreciate FANUC's proven track record. Electronics and job shops can also benefit, though simpler alternatives might suffice for lower-volume work.
6. How long do FANUC CNC controllers typically last?
FANUC controllers typically last for 15–20 years or more. Many shops still run controllers from the 1990s that work perfectly with modern software updates. The hardware is built for industrial environments and designed to outlast the mechanical components of the machines they control. This longevity protects your programming investment. Since the G-code written decades ago still runs on current systems.
Join thousands of creators
receiving our weekly articles.