Automated machine tending uses robots to load, unload, and monitor manufacturing equipment without human intervention.
20.6% of manufacturing plants report labor shortages as a key constraint on production while machines sit idle between shifts. Robots keep machines running between shifts instead of sitting idle.
This guide explains how to choose the right robot, calculate ROI, and get your first machine-tending cell up and running fast.
What is automated machine tending?
Automated machine tending refers to the use of robotic systems to load and unload parts or materials into and out of machines, particularly CNC machines, in manufacturing settings. It handles repetitive loading tasks that often lead to strain injuries or operator fatigue.
Instead of an operator standing by each machine, a robot handles the cycle. Your CNC mill finishes a part, the robot opens the door, removes the finished piece, loads a new blank, closes the door, and hits cycle start. The machine runs continuously while the operator manages multiple cells.
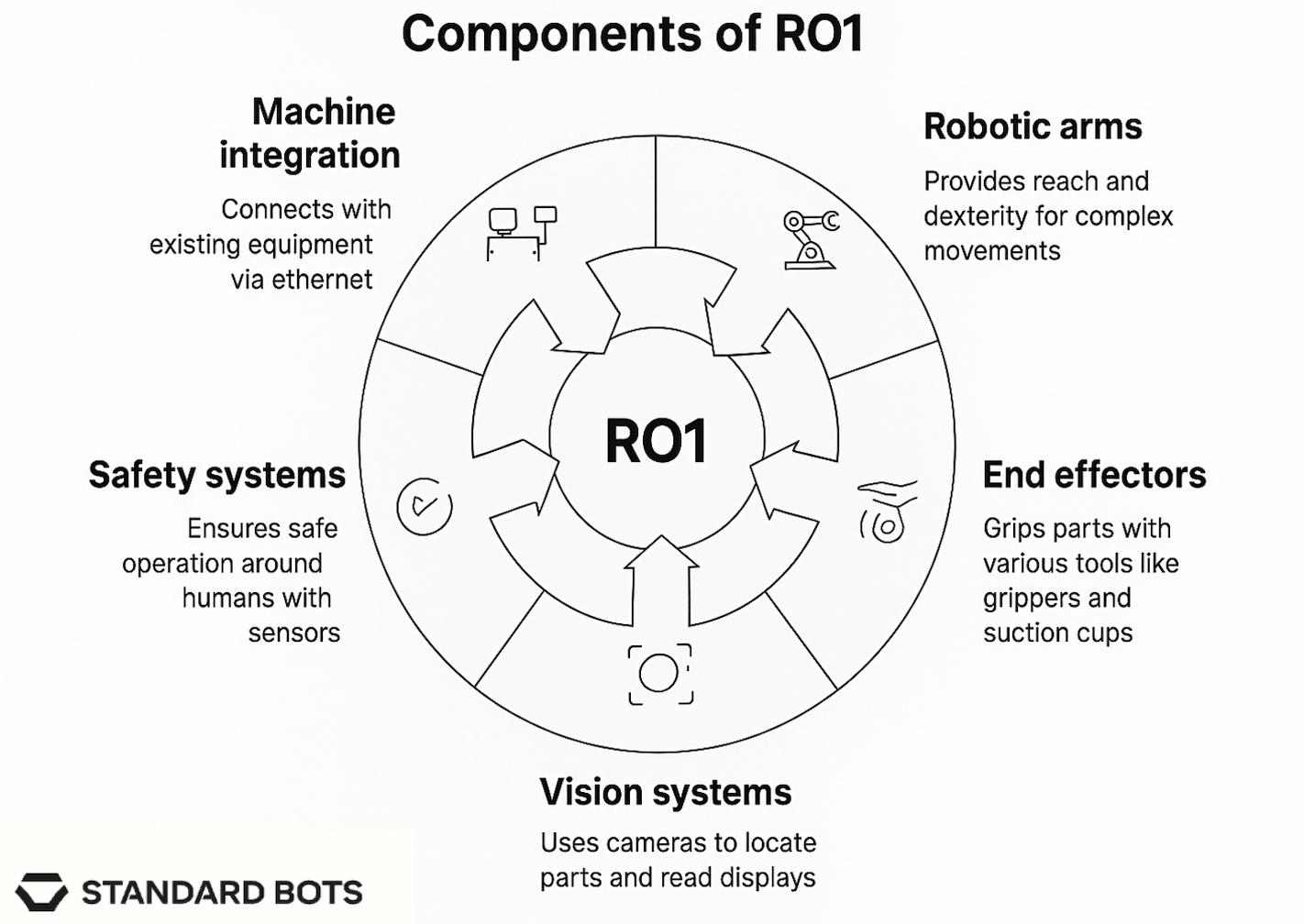
Manual vs. automated comparison
Manual tending usually requires one operator per machine, limiting how many machines can run at once. In contrast, automated setups allow one operator to manage 3 to 5 machines, freeing up labor for more skilled tasks.
Manual operations run 8–16 hours a day based on shift schedules, but automation makes 24/7 lights-out manufacturing possible. That means higher machine use and faster ROI. And since fatigue accounts for up to 42% of quality defects, mistakes creep in after long hours, and quality can dip. Robots repeat each task with the same timing and precision, shift after shift.
Automated CNC machine tending explained
Automated CNC machine tending focuses specifically on CNC mills, lathes, and machining centers, the backbone of most machine shops. CNC machines are ideal for automation because of their repeatable programs and standard interfaces.
Typical CNC tending workflow
- Load raw material: Robot picks up bar stock, blanks, or castings from a staging area
- Open machine door: Either through I/O signals or physical door operation
- Remove finished part: Extract the completed workpiece from the chuck or fixture
- Load new blank: Position fresh material in the correct orientation
- Close the door and start the cycle: Send the start signal to begin machining
- Monitor and repeat: Track cycle time and be ready for the next part
So, why does CNC tending work so well? CNC machines are ideal for automation because they run predictable cycles. Think of the same program being executed identically every time. Most modern mills come with standard Ethernet or I/O connections, so integrating a robot is simple and usually doesn’t require custom wiring.
The high-value parts these machines produce make the automation investment worth it, especially since they can run around the clock with the right monitoring in place.
Integration with popular mills
- Haas mills: RO1 connects directly via Ethernet
- Mazak centers: Standard I/O handles door control and cycle signals
- DMG Mori: Supports most models through universal interfaces
- Okuma lathes: Compatible with bar feeders and chuck-based systems
CNC tending operations
Types of automated machine tending systems
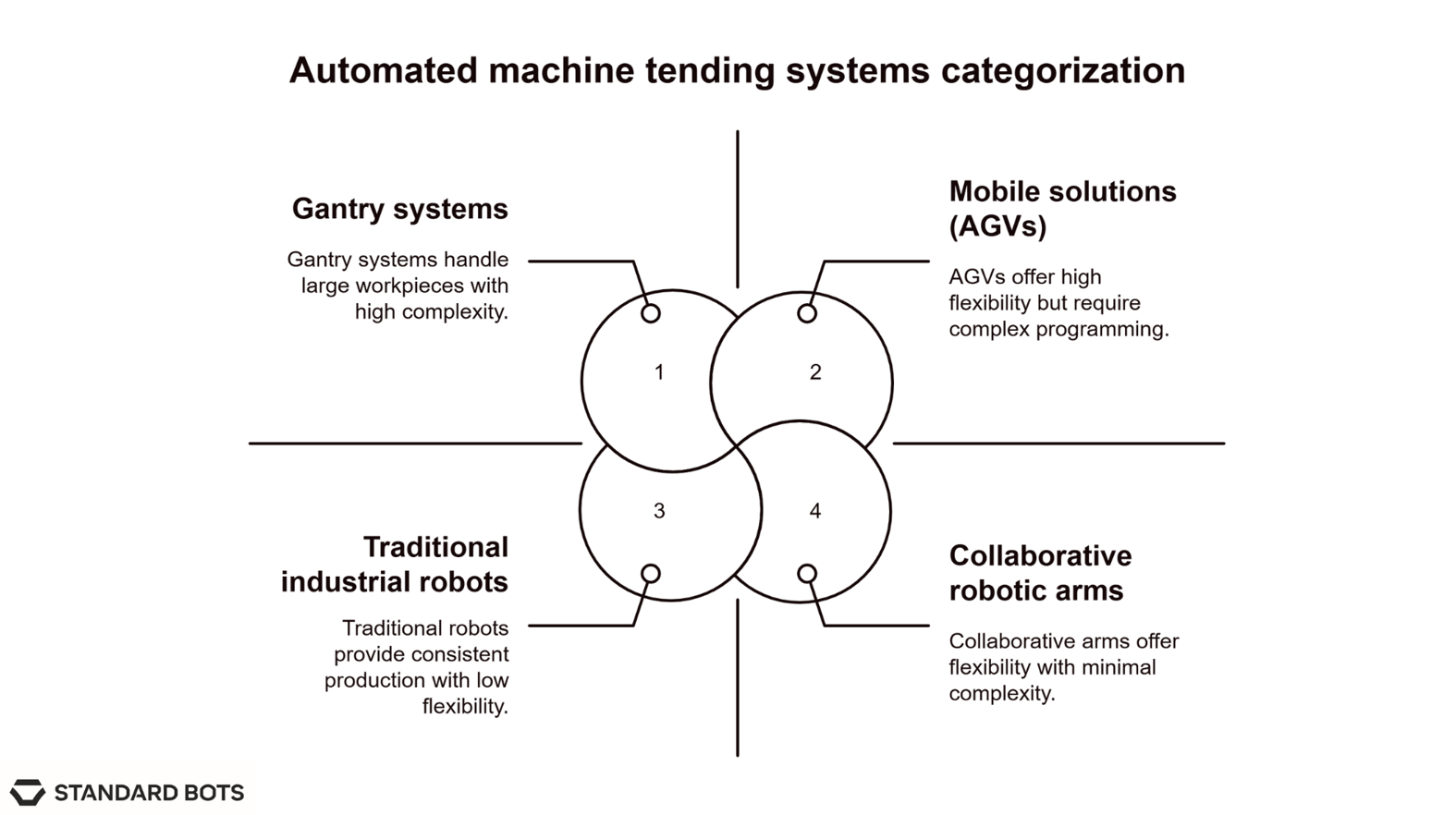
Cobots
Six-axis arms like RO1 operate safely around humans without safety fencing. Built-in sensors detect collisions and automatically stop movement when contact occurs. These systems offer the most flexibility for changing product mixes and can be easily reprogrammed by operators.
Best for: Flexible programming and mixed production
Traditional industrial robots
Many traditional industrial robots have higher speed and payload capabilities, but require safety fencing to protect workers. These robots excel in high-volume applications where consistent cycle times matter most. Programming may require specialized technicians rather than shop floor operators.
Best for: High-volume, consistent production runs
Gantry systems
Linear motion gantry robot systems mounted overhead or on rails are ideal for handling heavy parts across large work areas. These systems can cover multiple machine tools simultaneously and offer excellent reach for oversized workpieces. Setup requires significant floor space and structural support.
Best for: Large workpieces and high-speed operations
Mobile solutions (AGVs)
Autonomous guided vehicles (AGVs) move between multiple machines, handling parts transfer and basic tending operations. These systems work well in facilities where robots need to service several different machine types. Programming complexity increases with workflow complexity.
Best for: Complex workflows and multiple stations
Top 5 benefits of using automated machine tending
- 24/7 operations and increased productivity: Robots run continuously without breaks, allowing machines to operate during off-shifts when no operators are present. This maximizes equipment use and can double or triple daily output. RO1's precision ensures parts are positioned correctly every time with consistent cycle times.
- Enhanced safety and ergonomics: Workers no longer perform repetitive lifting, bending, and reaching motions hundreds of times per shift, reducing workplace injuries. Robots work with parts straight from heat treatment or handle sharp machined components without risk of burns or cuts. RO1's collision detection prevents accidents, with force sensors automatically stopping movement when unexpected contact occurs.
- Consistent quality and precision: RO1's ±0.025 mm repeatability ensures parts are positioned identically every cycle, leading to consistent machining results. This precision is impossible to maintain manually over long runs. Consistent part positioning eliminates setup variations that cause dimensional issues, meaning less rework and lower material costs.
- Labor cost savings: Automated machine tending provides a reliable solution that doesn't call in sick or quit unexpectedly, allowing better production planning. Operators can focus on quality control, machine setup, and process optimization instead of standing by machines.
- Easy scalability: RO1's no-code programming allows operators to create new routines for different parts without specialized training. Changes take minutes, not hours. When production volumes change, robots easily work additional shifts without hiring and training temporary workers.
Machine tending costs and ROI breakdown
Initial investment ranges
Basic systems: Entry-level machine tending setups start at $25K–50K for simple applications like CNC loading. These systems typically include a cobot arm, a basic gripper, and simple integration with existing equipment.
Advanced systems: Full-featured installations with vision systems, multiple end effectors, and complex integration can range from $100K–250K. These handle more sophisticated applications like multi-station tending or complex part handling.
Installation costs: Add 10–20% to system costs for professional installation, commissioning, and initial training. RO1 installations are faster due to plug-and-play design and no-code programming.
ROI calculation example
Labor savings: A single robot can replace one operator per shift, saving $40K–80K annually when factoring in wages, benefits, and overhead costs. Multi-shift operations see proportionally higher savings.
Typical payback period: Most machine tending installations achieve ROI within 12 to 36 months, depending on labor costs and utilization rates. RO1's lower upfront cost often results in faster payback compared to traditional systems.
Productivity gains: Automated systems achieve significant throughput increases through reduced cycle times, elimination of breaks, and consistent performance. Extended operating hours can double, triple, or even 4x daily production.
Operating costs
Maintenance requirements: Expect a small percentage of the initial investment annually for routine maintenance, software updates, and occasional repairs. RO1's simplified design and remote diagnostics help minimize maintenance needs.
Power and utilities: Robotic systems have minimal impact on facility power consumption, with negligible additions to utility costs for most installations.
Training costs: Budget $500–1,500 per operator for initial training on system operation and basic maintenance. RO1's intuitive interface reduces training time compared to traditional systems requiring specialized programming knowledge.
How to choose the right machine-tending robot
How to implement automated CNC tending
You can get up and running by following three clear phases.
1. Planning and assessment
Begin by pinpointing which machines and parts make the strongest automation candidates. Look for high‑volume runs, predictable cycle times, and parts that are easy to grip and present.
Walk your shop floor to map out material flow, note any safety or guarding requirements, and verify that your CNCs have the right I/O or Ethernet connections. Finally, sketch a budget that covers robot hardware, end effectors, integration work, and operator training.
2. Installation and setup
With a solid plan in hand, bring in the robot cell. Coordinate site prep (power, network, safety fencing) before your integrator delivers and commissions the equipment.
Next, connect the robot to your CNC via its standard interface and install any conveyors or part‑presenting devices. Wrap up this phase by training your operators, typically one to two days, on basic cell operation, simple program tweaks, and routine maintenance checks.
3. Optimization and scaling
Once the cell is live, track key metrics: cycle times, uptime, scrap rates, and labor hours saved. Use that data to fine‑tune robot programs (grip force, approach paths, dwell times) and cell layout (part trays, feed hoppers) for maximum efficiency.
When you’ve dialed in performance, replicate the setup on additional machines, or expand the cell with a second robot arm or conveyor, to multiply your throughput gains.
Summing up
Automated machine tending is a practical way to handle labor shortages, boost output, and improve quality. The tech is proven, with most setups paying off within 12 to 36 months. RO1’s all-in-one system cuts setup time and cost, making it practical for small shops to automate. These systems run around the clock, reduce injuries, and maintain tight tolerances.
Machine tending automation with Standard Bots
Looking to upgrade your automation game? Standard Bots’ RO1 is the perfect six-axis cobot addition to any CNC setup, delivering unbeatable precision and flexibility.
- Affordable and adaptable: RO1 costs $37K (list). Get high-precision automation at half the cost of traditional robots.
- Precision and power: With a repeatability of ±0.025 mm and an 18 kg payload, RO1 handles even the most demanding CNC jobs.
- AI-driven simplicity: Equipped with AI capabilities on par with GPT-4, RO1 integrates seamlessly with CNC systems for advanced automation.
- Safety-first design: Machine vision and collision detection mean RO1 works safely alongside human operators.
Schedule your on-site demo with our engineers today and see how RO1 can bring AI-powered greatness to your shop floor.
FAQs
1. What types of machines work best with automated tending?
CNC mills, lathes, and machining centers are ideal for automated tending because they run predictable cycles and have standard interfaces. RO1 integrates directly with popular mills like Haas and supports universal I/O protocols for most modern equipment.
2. How long does it take to implement a machine-tending system?
RO1 installations can take hours instead of days due to the mobile base and no-code programming. Traditional systems may require weeks for installation, programming, and commissioning.
3. Do I need special training to operate a machine-tending robot?
No, RO1's intuitive touchscreen interface requires minimal training, typically 4-8 hours for operators to become proficient. The no-code programming approach eliminates the need for specialized robotics knowledge.
4. How reliable are machine-tending robots for production use?
Modern systems like RO1 are designed for industrial environments with built-in safety systems and remote diagnostics. Expect above 95% uptime with proper maintenance, and extensive support ensures quick resolution of any issues.
5. Can robots work safely around human operators?
RO1's collaborative design includes collision detection and force limiting that automatically stops movement when contact occurs. As a cobot, RO1 works safely alongside people in most shop environments. No cages required.
6. What other applications can machine-tending robots handle?
Beyond CNC tending, robots excel at pick and place operations, palletizing, welding, deburring, sanding, and polishing applications. RO1's versatility allows it to handle multiple applications with quick changeovers.
7. How does automated machine tending compare to manual operations?
Automated machine tending provides consistent quality compared to manual operations. It eliminates fatigue-related errors and enables 24/7 operation. Manual tending costs $25–35/hour per operator, but automated systems can operate for significantly less while providing superior precision and reliability.
Join thousands of creators
receiving our weekly articles.