Manufacturing robots are programmable machines that perform tasks like welding, assembly, and material handling on the factory floor.
In 2025, they’re no longer exclusive to big-budget operations. Robots like RO1 have made automation practical for small and mid-sized manufacturers by cutting labor costs and keeping production running around the clock.
According to the International Federation of Robotics, global robot density reached a record 162 units per 10,000 employees in 2023, more than double the number from just seven years ago.
What are robots for manufacturers?
Robots in manufacturing are automated systems that include robotic arms or other specialized machines. They take on the heavy lifting of production by handling repetitive, dangerous, or highly precise tasks that people cannot sustain for long periods.
By working with consistent accuracy, they help factories run faster, reduce errors, protect workers from hazards, and deliver higher quality output shift after shift.
Modern manufacturing robots handle everything from welding and assembly to machine tending and packaging. They're equipped with sensors, vision systems, and AI-powered controls that make them smarter and more adaptable than ever before.
Why are more manufacturers automating in 2025?
- Labor shortages are hitting hard. The average age of a skilled welder in the U.S. is 55, and there aren't enough younger workers entering manufacturing trades to replace retiring veterans. The National Association of Manufacturers projects that 2.1 million manufacturing jobs could go unfilled by 2030.
- Rising wages and benefits costs make automation more attractive. When you factor in overtime, insurance, and turnover costs, robots often pay for themselves within 18 months.
- Global competition demands efficiency. Manufacturers who don't automate are losing ground to competitors who can produce faster, more consistently, and with lower per-unit costs.
What does a factory robot cost in 2025?
Cobots: $25,000 to $75,000
- Entry-level collaborative robots start around $10,000 for basic functionality, with decent payload capacity.
- Mid-range cobots ($40,000 to $60,000) offer higher payloads, longer reach, or specialized features like force control for assembly tasks. For example, RO1 lists at $37,000 and includes built-in vision, no-code programming, and plug-and-play compatibility with standard grippers.
- High-end collaborative systems can hit $75,000 or more when you add advanced vision, AI capabilities, or specialized end effectors for complex applications.
Industrial systems: $100,000 to $500,000
- Traditional industrial robot systems cost significantly more, starting around $100,000 for a basic 6-axis system without peripherals.
- High-speed or heavy-payload robots easily reach $200,000 to $300,000, especially when you factor in safety systems, custom tooling, and integration work.
- Turnkey robotic cells with conveyors, safety systems, and custom programming can exceed $500,000 for complex applications like automotive welding or aerospace machining.
Total system costs: Installation, training, and end effectors
End effectors (grippers, welding torches, sanders) add $5,000 to $25,000, depending on complexity.
- Installation and programming typically run 20–50% of the robot's cost, but this can go even higher, at 50–100% of the base price. Simple setups might need just a few days of engineering time, whereas complex cells require weeks of integration work costing $10,000 to $50,000.
- Training your team is often overlooked but crucial. Budget 2–5 days of operator training and ongoing support, especially for the first few months.
- Hidden expenses include air compressors for pneumatic grippers, safety upgrades to meet current codes, and sometimes facility modifications for power or network access. Plan for an additional 10–15% of your budget for unexpected costs.
ROI calculation examples
A $40,000 cobot replacing one full-time operator at $60,000/year (including benefits) pays for itself in about 8–10 months. Add in reduced scrap, increased uptime, and the ability to run lights-out, and payback often drops to 6–18 months.
Real-world example: Dynamic Group, an injection molding company in Minneapolis, deployed three UR10 cobots for machine tending and kitting applications.
The company went from having three operators on a single shift to running three shifts per day with just one operator per shift, quadrupling production capacity with an ROI of just two months.
Real-world use cases of robots in manufacturing
Welding, cutting, and material handling
- Automotive and aerospace manufacturers have used welding robots for decades, but the technology has become accessible to smaller fabrication shops. Modern systems handle MIG, TIG, and spot welding with consistent quality that human welders struggle to match over long shifts.
- Heavy equipment manufacturers like Caterpillar use robots for both welding and material handling, moving parts that would require multiple workers or overhead cranes. The robots reduce injury risk while maintaining precise positioning for critical welds.
- Material handling in harsh environments is where robots truly shine. Steel mills, foundries, and chemical plants use robots to move materials in temperatures and conditions that would be dangerous or impossible for human workers.
CNC machine tending
- Machine tending represents the sweet spot for many manufacturers. Robots excel at loading blanks, removing finished parts, and keeping CNC machines running during unmanned shifts.
- Automotive suppliers like Tier 1 parts manufacturers have automated machine tending across hundreds of production cells. The consistent loading reduces setup variations and improves part quality while enabling 24/7 production.
- Job shops with high-mix, low-volume work benefit from robots that can quickly adapt to different part geometries. Modern cobots can switch between different part types in minutes rather than hours.
Packaging and palletizing
- Consumer goods companies rely heavily on packaging robots for case packing, labeling, and palletizing operations. Companies like Procter & Gamble use robots to handle thousands of product variations across their manufacturing network.
- Food and pharmaceutical manufacturers benefit from robots' consistency and cleanliness. Vision-equipped systems can reject defective packages while maintaining precise placement for downstream equipment.
- E-commerce fulfillment centers like Amazon's warehouses use robots for both picking and packing operations, handling the variable demands of online retail without the staffing challenges of traditional manual operations.
Common mistakes to avoid when automating for the first time
When automating for the first time, common mistakes to avoid include skipping safety checks, choosing complex tasks or equipment, or underestimating the available space.
Additionally, automation projects often fail when companies don't properly adjust their existing work processes, forget to budget for supplies and replacement parts, or expect instant results. These oversights can seriously hurt the success of any automation efforts.
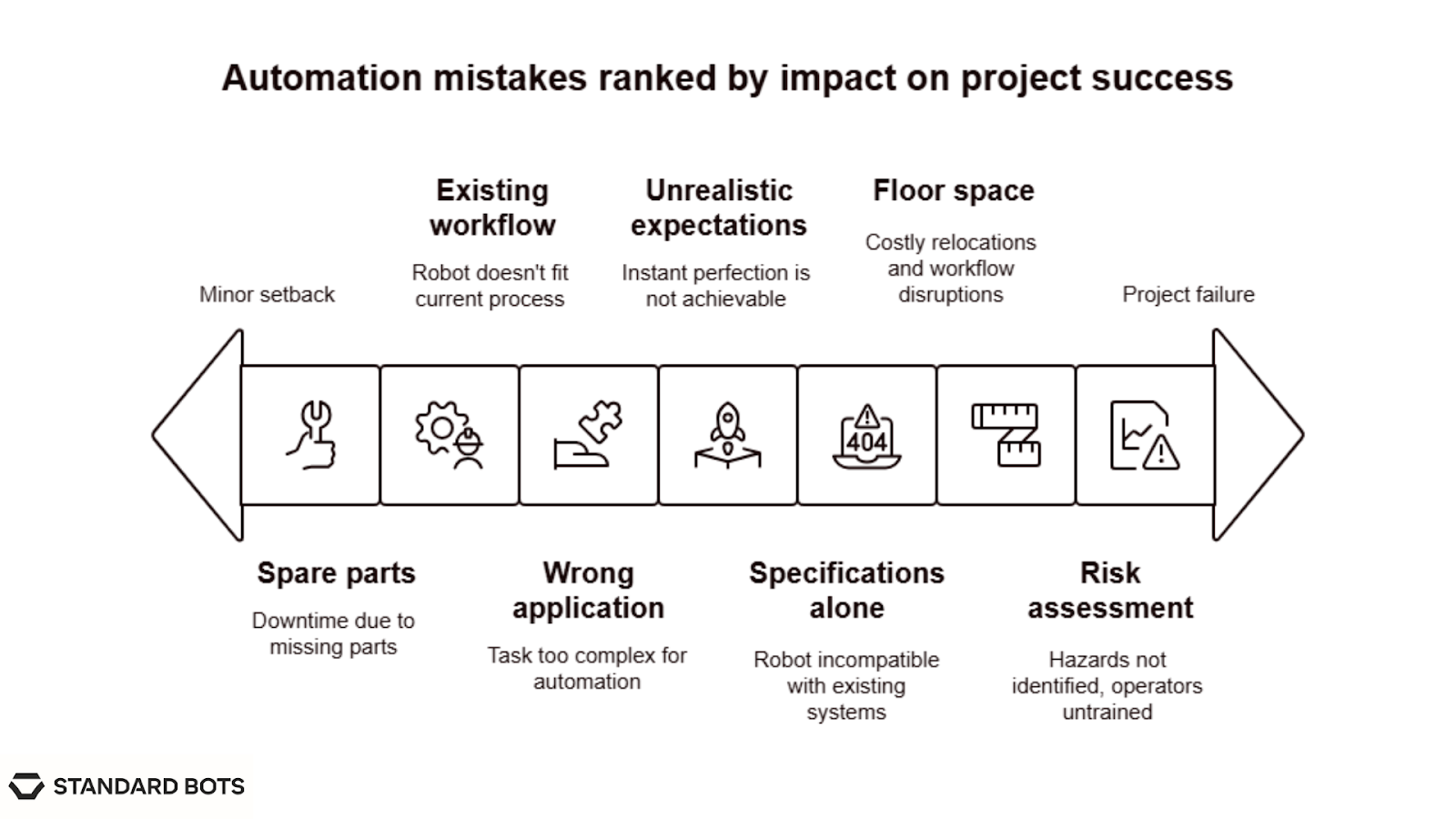
Common mistakes:
- Skipping the risk assessment: Even cobots require proper safety evaluation. Document potential hazards, establish safety protocols, and train operators on emergency procedures before deployment.
- Choosing the wrong application: The right application to start with is not your most complex process. Avoid tasks with high variation, frequent changeovers, or unclear success metrics. Begin with repetitive tasks that have consistent part geometry and measurable outcomes.
- Underestimating floor space requirements: Robots need room to move, and operators need access for maintenance. Measure twice, install once, or you'll face costly relocations and workflow disruptions.
- Ignoring your existing workflow: Don't force a robot into a process designed for humans. Analyze material flow, cycle times, and handoff points before automation. Sometimes, small process changes make automation much more effective.
- Buying based on specifications alone: The fastest robot isn't always the best choice. Consider programming ease, support quality, and how well the robot integrates with your specific equipment and software systems.
- Forgetting about consumables and spare parts: Budget for replacement grippers, filters, and wear items. Know your supplier's parts availability and lead times before you're stuck with a down robot waiting for a $50 component.
- Setting unrealistic expectations: Your first robot won't solve every problem immediately. Plan for a learning period and gradual optimization rather than expecting instant perfection.
Other alternatives: FANUC, ABB, KUKA, Yaskawa
- FANUC leads in reliability and service network, but comes with premium pricing and complex programming requirements that your team may need training on. Its yellow robots are everywhere in automotive plants, but small manufacturers often find them overkill.
- ABB excels in software integration and offers strong vision capabilities, but its systems require significant engineering support for deployment. They’re better suited for facilities with existing robotics expertise or dedicated integrators.
- KUKA robotics brings German engineering precision and excellent path planning software, but often requires custom integration that increases total project costs. They work best in large, engineered-to-order environments where precision matters more than plug-and-play ease.
- Yaskawa (Motoman) offers extensive industrial systems with good servo technology, but programming complexity keeps them primarily in high-volume applications. Their robots are a go-to for automotive and electronics manufacturing, where scale justifies the setup time.
Up-and-coming players making waves
- Neura Robotics is pushing cognitive capabilities and AI integration. Following its €120 million Series B funding round in January 2025, the company has begun limited commercial deployments alongside ongoing development work.
- Boston Dynamics continues to lead in mobility and dexterity research, but its systems remain primarily research-focused rather than practical manufacturing tools.
- Amazon Robotics dominates warehouse automation but doesn't sell systems to external customers; its innovations stay within Amazon's fulfillment network.
- Ubtech Robotics focuses on humanoid systems that are more suited to service applications than traditional manufacturing tasks.
Final thoughts
Robots in manufacturing are no longer limited to large factories. In 2025, cobots like RO1 make automation accessible for small and medium manufacturers by offering precision, flexibility, and quick ROI.
Costs vary by type and complexity, but most pay for themselves within one to three years. From welding and CNC tending to packaging and palletizing, robots improve safety, consistency, and output. For manufacturers ready to stay competitive, automation is now a practical and proven investment.
Is your operation ready for robots?
Looking to upgrade your automation game? Standard Bots’ RO1 is the perfect six-axis cobot addition to any manufacturing setup, delivering unbeatable precision and flexibility.
- Affordable and adaptable: RO1 costs $37K (list). Get high-precision automation at half the cost of traditional robots.
- Precision and power: With a repeatability of ±0.025 mm and an 18 kg payload, RO1 handles even the most demanding CNC jobs.
- AI-driven simplicity: Equipped with AI capabilities on par with GPT-4, RO1 integrates seamlessly with CNC systems for advanced automation.
- Safety-first design: Machine vision and collision detection mean RO1 works safely alongside human operators.
Schedule your on-site demo with our engineers today and see how RO1 can bring AI-powered greatness to your shop floor.
FAQs
1. How much does an industrial robot cost to buy and install?
An industrial robot’s cost ranges from $50,000 to $200,000. Including integration, safety systems, and training, total system costs typically fall between $150,000 and $500,000, depending on complexity and payload.
2. What is the average payback period for a manufacturing robot?
The average payback period for a manufacturing robot in 2025 is between 12 and 36 months. Cobots like RO1 often achieve ROI faster, typically within 6 to 12 months, because of lower upfront costs and the ability to operate during unattended shifts.
3. Which industries benefit most from collaborative robots?
Industries like metal fabrication, CNC machining, packaging, welding, and electronics assembly benefit most from collaborative robots. These sectors rely on repetitive, precision-driven tasks that cobots handle efficiently, often without safety cages or complex programming.
4. How do ABB, FANUC, KUKA, and Yaskawa robots differ in programming ease?
FANUC and Yaskawa offer intuitive programming with built-in welders and setup wizards. ABB supports offline programming through RobotStudio, whereas KUKA requires KRL scripting knowledge. RO1 simplifies the experience with no-code programming and built-in vision.
5. Do small and medium-sized manufacturers need in-house engineers to run robots?
Small and medium-sized manufacturers do not always need in-house engineers to run robots. Cobots like RO1 include no-code interfaces and pre-integrated systems so shop-floor operators can manage them. Complex setups may still benefit from integrator support, but daily operation typically doesn’t require engineering staff.
6. What safety certifications are required before deploying robots on the factory floor?
Safety certifications like ISO/TS 15066, ISO 10218-1, and ISO 10218-2 are required depending on the type of robot. Collaborative robots follow ISO/TS 15066, which governs safe human-robot interaction. Notably, ISO/TS 15066 content is being integrated into ISO 10218-1:2025.
Traditional robots must meet ISO 10218 standards for both robot design and system integration. U.S. facilities may also need to comply with OSHA 1910 Subpart O, and CE certification is common in the EU. A full risk assessment is required before deployment.
7. Can existing CNC machines be retrofitted with robots for tending?
Yes, existing CNC machines can be retrofitted with robots for tending via standard I/O, Ethernet, or fieldbus protocols. RO1 is already compatible with mills from Haas, Mazak, DMG Mori, and Okuma.
Join thousands of creators
receiving our weekly articles.