There are more types of welding robots than there are flavors of energy drinks. And sure, most of them promise precision, speed, and lower burn risk (to humans, anyway).
But which one actually works for your factory floor, and how much are we talking? We’re going to do a deep dive and tackle every question you’ve got.
What is a robotic welding machine?
A robotic welding machine is what happens when you give a robotic welding arm a torch and a game plan. Unlike traditional welders who blink and sneeze, these bots show up ready to lay beads all day. Zero smoke breaks, no skipped steps, and fewer complaints about the playlist.
You’ll usually see them as 6-axis arms, gantry rigs, or collaborative cobots, depending on what’s being welded (and how much budget you didn’t blow on custom fixtures).
The biggest upgrade? These bots repeat near-perfect welds with the kind of consistency that makes humans look like they're playing a different game.
The 7 main types of welding robots
Not every robotic welding machine shows up to work with the same energy. These are the core types, each with a different method, use case, and personality flaw.
What makes each type of welding robot useful (or dramatic)?
- Arc welding robot: These robots use electric current and shielding gas to fuse metals like steel and aluminum. They’re the default for structural work, automotive frames, heavy equipment, and anything that needs to survive a forklift bump.
- Spot welding robot: This one uses pressure and current to join thin sheets at lightning speed. It’s a common robot welder in high-volume production, especially in automotive body lines and appliance manufacturing.
- Laser welding robot: The precision king. Laser bots work fast and clean, with minimal distortion. Perfect for battery packs, electronics, and high-end sheet metal components.
- Plasma welding robot: This one hits hot and deep. It’s the choice for exotic alloys, aerospace builds, and any part that would melt under MIG.
- Ultrasonic welding robot: Instead of heat, it uses high-frequency vibration to join plastics. Think disposable medical gear, headphones, and tech gadgets you yell at.
- Friction welding robot: No arc, no flame, just rotational force and pressure. Ideal for rods, axles, and round parts where traditional methods get messy.
- Hybrid welding robot: Combo-bots that mix arc, MIG, or laser in one setup. Great for inconsistent joints or projects that need strength, speed, and surface quality at once.
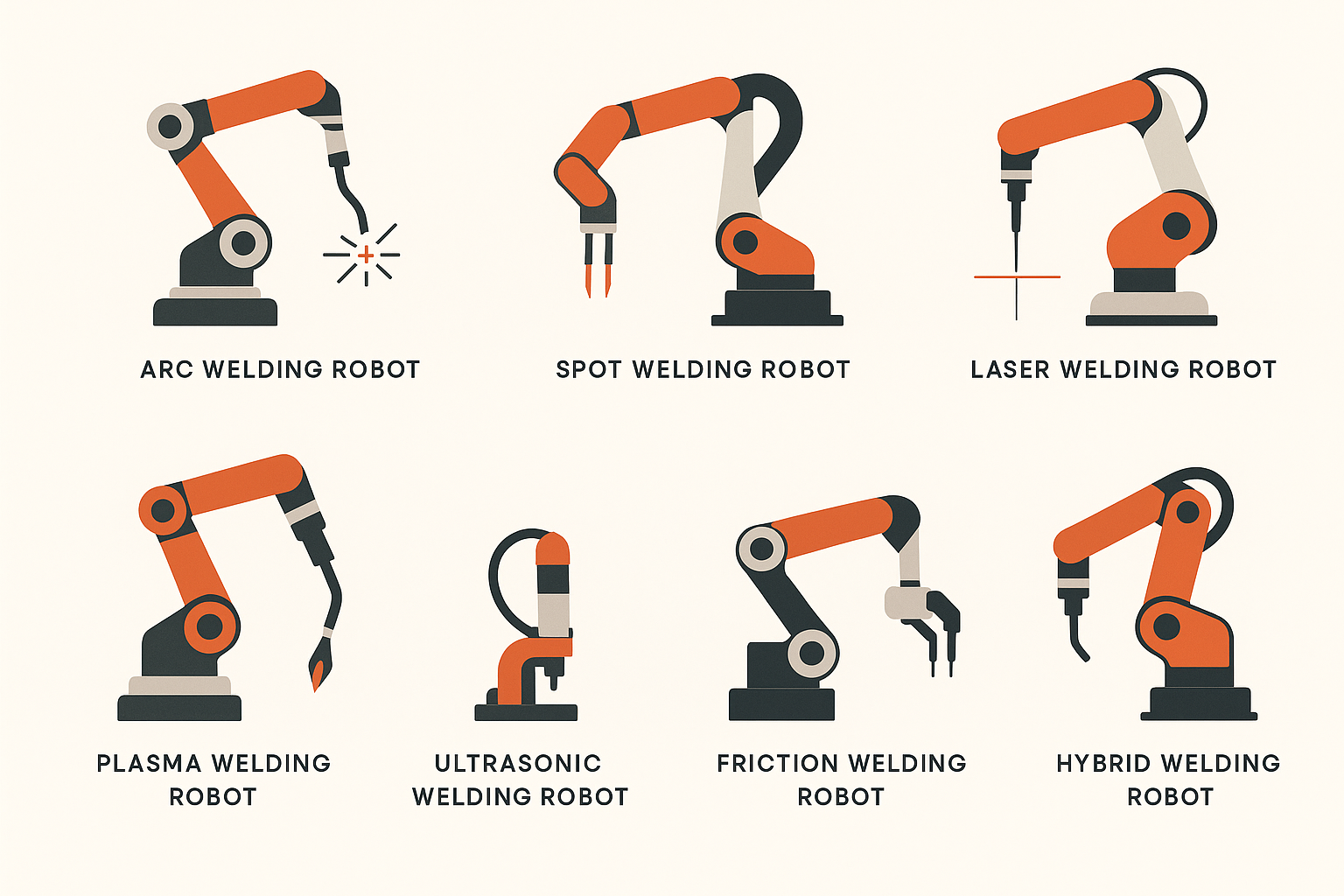
Honorable mentions
Resistance welding bots are still in use for low-complexity joints. Electron beam robots exist, too, but unless you’ve got vacuum chambers and a space program, they’re probably not on your shortlist.
Still curious why arc welding robots haven’t gone out of style? This no-fluff guide covers it in detail.
Considerations when looking for the right welding robot
Choosing a robot welder goes way beyond choosing a big-name brand and praying. It’s about what actually works with your parts, people, and plant layout.
What separates a smart buy from a six-figure mistake?
- Material and thickness tolerance: Not every robotic welding arm can handle cast aluminum and 3 mm stainless steel with the same grace. Know your metal, or get stuck with burn-throughs and warped edges.
- Geometry drama: Tight seams, weird angles, or multi-surface welds? That limits which bots (and end effectors) you can use, especially if it’s a cobot vs. industrial setup.
- Volume and cycle time pressure: Low-volume? A flexible cobot might make more sense. High-volume line? You’ll need a beast that can repeat welds without a twitch.
- Floor plan gymnastics: Do you have space for a cell? Can you isolate the bot? Do your forklift drivers respect physical barriers? These all matter.
- Staff experience (or lack of it): If your team’s never touched automation, don’t start them off on a 9-axis offline-programmed monster. Look for a no-code or teach-by-guiding setup.
- Budget and return window: Calculate ROI in months or years. Factor in integration, training, consumables, and what happens when someone drops the pendant.
Robotic welder cost breakdown
Let’s talk numbers, because no one’s dropping a bunch of money on a robotic welding machine without receipts.
Typical robot welder pricing tiers
- Entry-level cobot welders ($25K–$50K): These are flexible, easy to deploy, and often ideal for smaller shops or low-volume runs. But don’t expect them to handle heavy fabrication without some compromises.
- Industrial arms with welding heads ($60K–$120K): These are workhorses. Full-size robotic welding arms with longer reach, higher payloads, and tighter integration. The sweet spot for many mid-size factories.
- Full welding cells with enclosures, software, and safety ($150K–$250K+): When you need the whole show, including sensing, shielding, and real-time process control. Usually found in high-throughput OEM setups.
Other budget-eating extras
- Integration and software setup: Buying the bot is the easy part. Making it talk to your line and not crash into walls? That’s the fun bill.
- Maintenance, support, and retooling: Jigs break, torches wear out, and software updates don’t install themselves.
- Lease or buy? Leasing is gaining traction, especially with newer robotic welding companies putting out lower entry costs. But check the fine print, as some leases sneak in usage limits.
Need a breakdown of robot pricing across more than just welders? This guide’s got numbers that won’t age poorly. And this one covers average robot costs.
The best welding robots: TL;DR
The 5 best welding robots for 2025
1. Standard Bots RO1 — Best for shops that want smart automation without the corporate tax
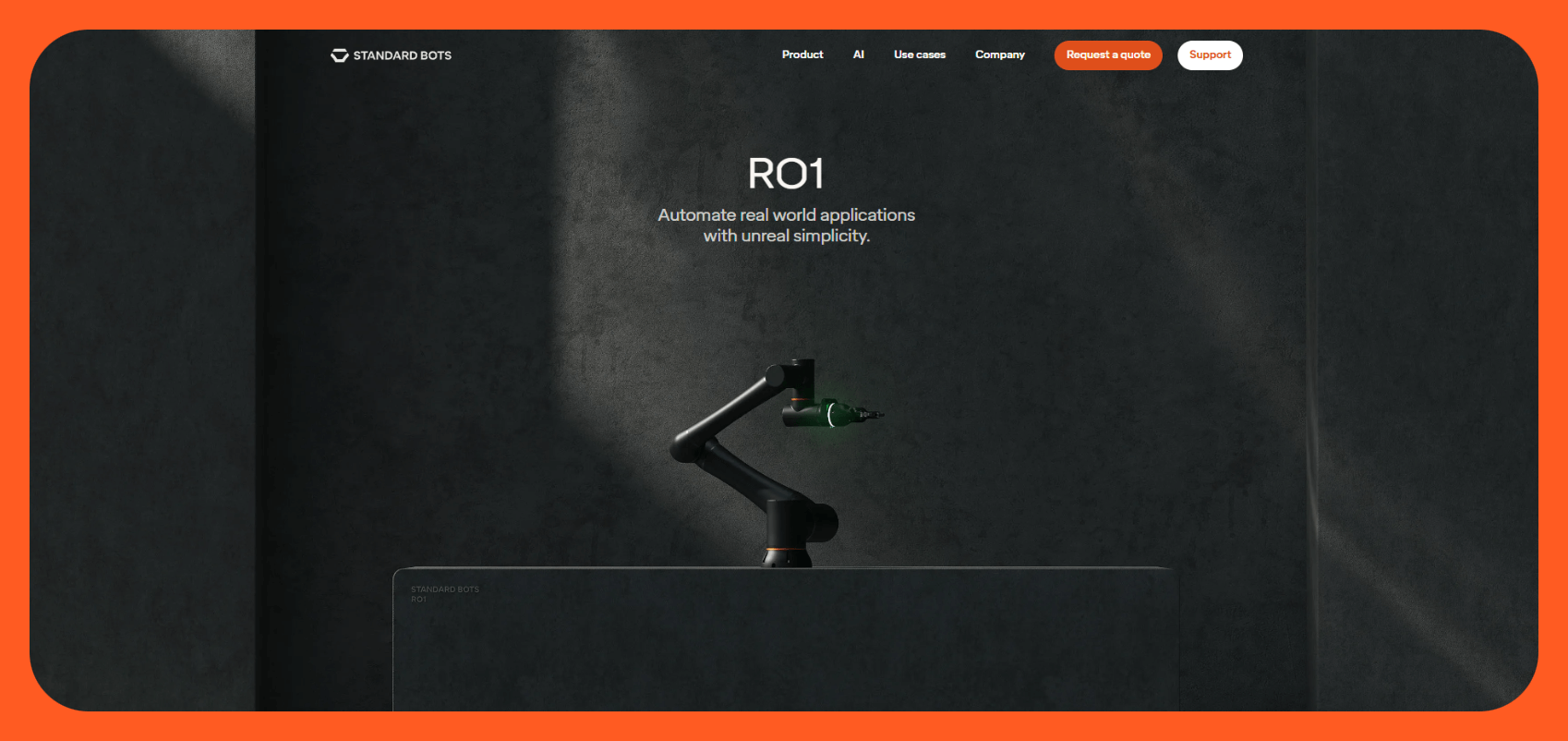
A lean, mean, six-axis robotic welding arm that doesn’t cost more than your shop’s yearly electricity bill. RO1 isn’t just another cobot, it’s loaded with AI on par with GPT-4, learns fast, and skips the usual software nightmares.
You can run this thing straight out of the box without a nervous breakdown.
Who it’s for: You run a CNC shop, small fab operation, or want to ditch inconsistent manual welds. But you don’t want to remortgage your house for a robot that needs five engineers to babysit it.
Why is it worth the hype?
- AI with good manners: Learns patterns without nuking your parts
- No-code swagger: Teach it with clicks, not scripts
- Tight tolerances: Repeatability of ±0.025 mm
- Solid lifting game: 18 kg payload gets the job done
How much are we talking?
Half of comparable models with a list price of $37K. → Pricing info
2. FANUC ARC Mate 100iD — Best for factories that worship speed and repeatability
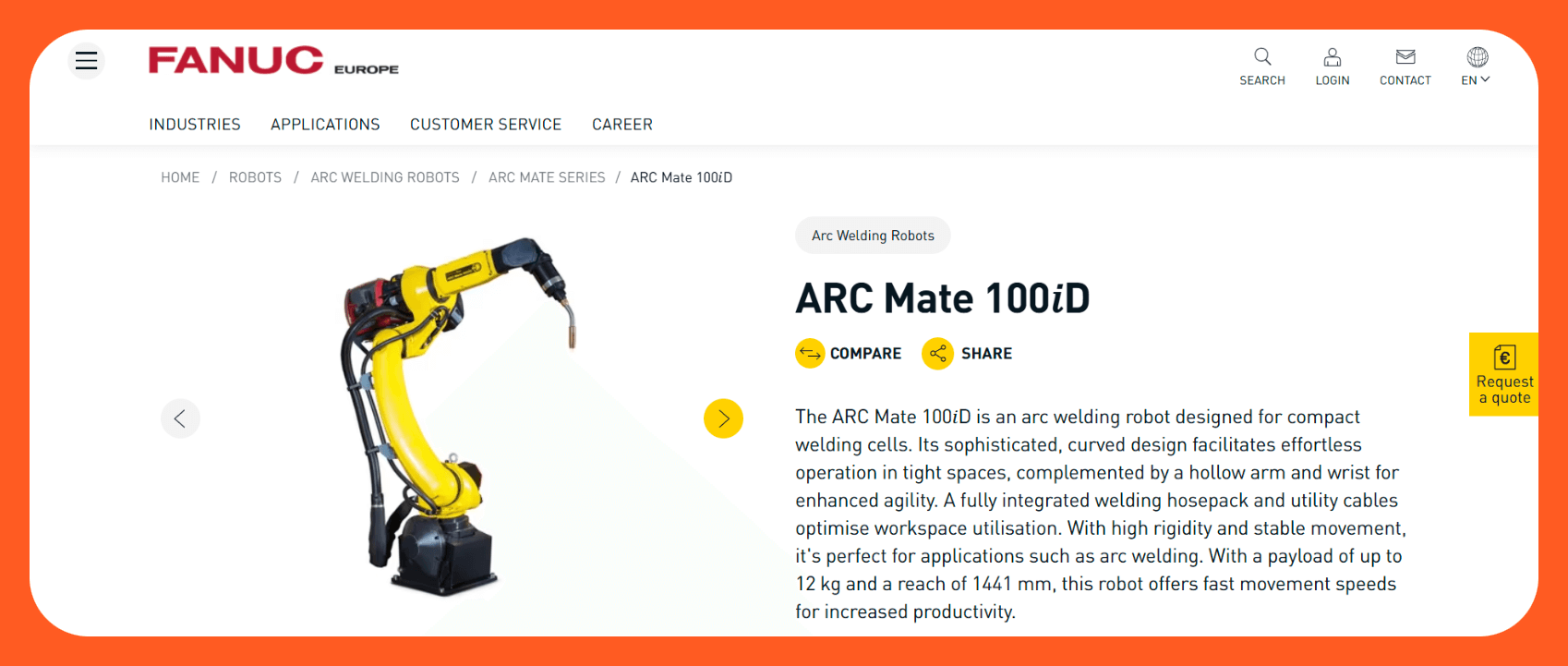
One of the most well-known industrial robot welders in the game. It’s basically the Toyota Camry of welding robots. It’s everywhere, reliable, and surprisingly agile.
Who it’s for: Big plants, automotive lines, or any operation pushing serious volume with no time for tech drama.
Why is it worth the hype?
- Seam tracking built in: Like a GPS for your welds
- Wrist cabling that doesn’t suck: Reduces snag risks
- Speed demon: Designed for high throughput on MIG/TIG
How much are we talking?
Most setups clock in around $25K and over, not counting extras like the controller or cell hardware.
3. ABB IRB 6700 — Best for welding absolutely massive things
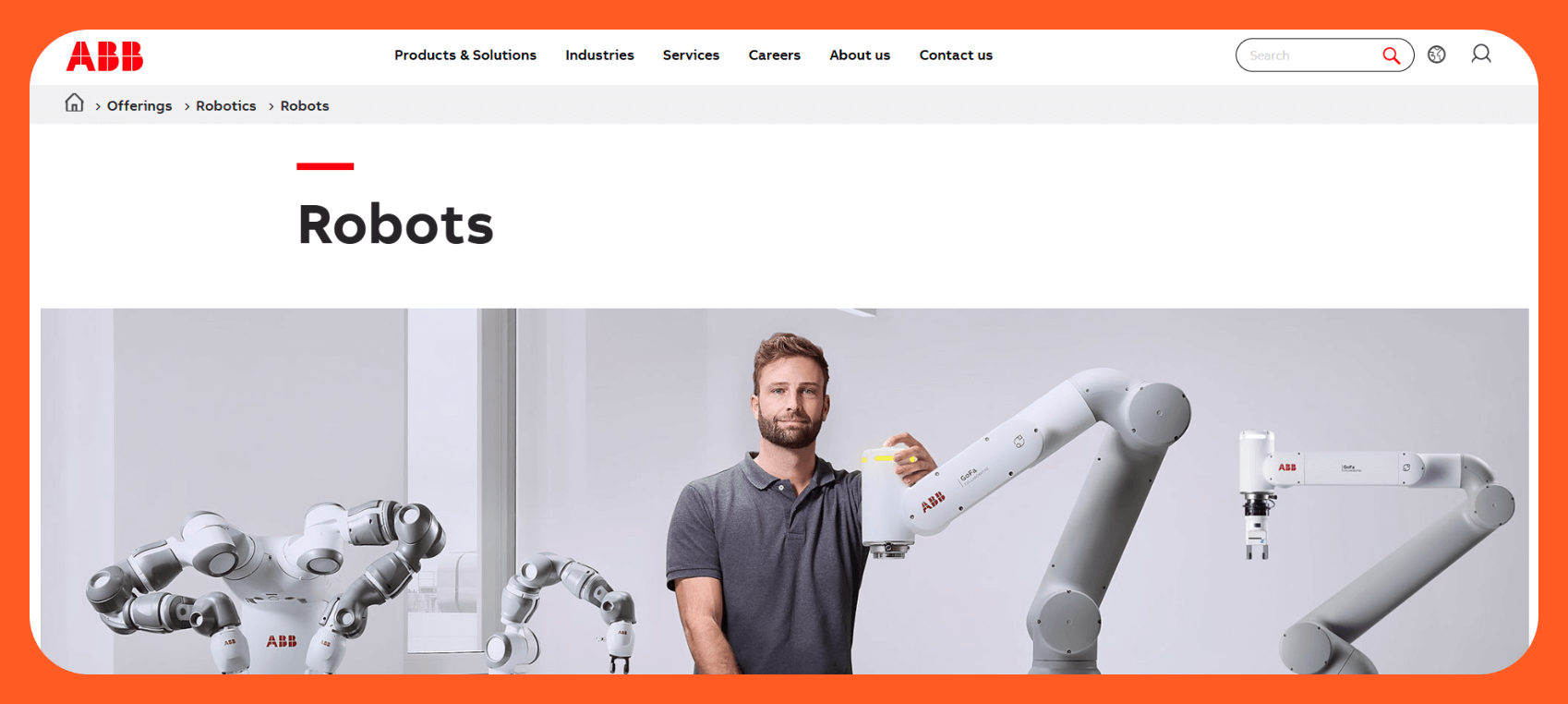
A heavy-duty industrial robotic welding machine that doesn’t flinch at long reaches, high payloads, or nasty environments. This is the robot equivalent of a long-haul trucker who welds steel beams in a sandstorm for fun.
Who it’s for: Large-scale metal fabricators, aerospace contractors, and anyone who needs strength and precision in the same machine.
Why is it worth the hype?
- Payload beast: Up to 300 kg, because why not
- Factory armor: Optimized for dust, heat, and noise
- Long reach: Up to 3.2 meters, depending on the model
How much are we talking?
Roughly $35K to $75K and over, depending on your config. Some vendors sell it for $90K and over — used.
4. Yaskawa AR1440 — Best for tight spaces and surgical welds
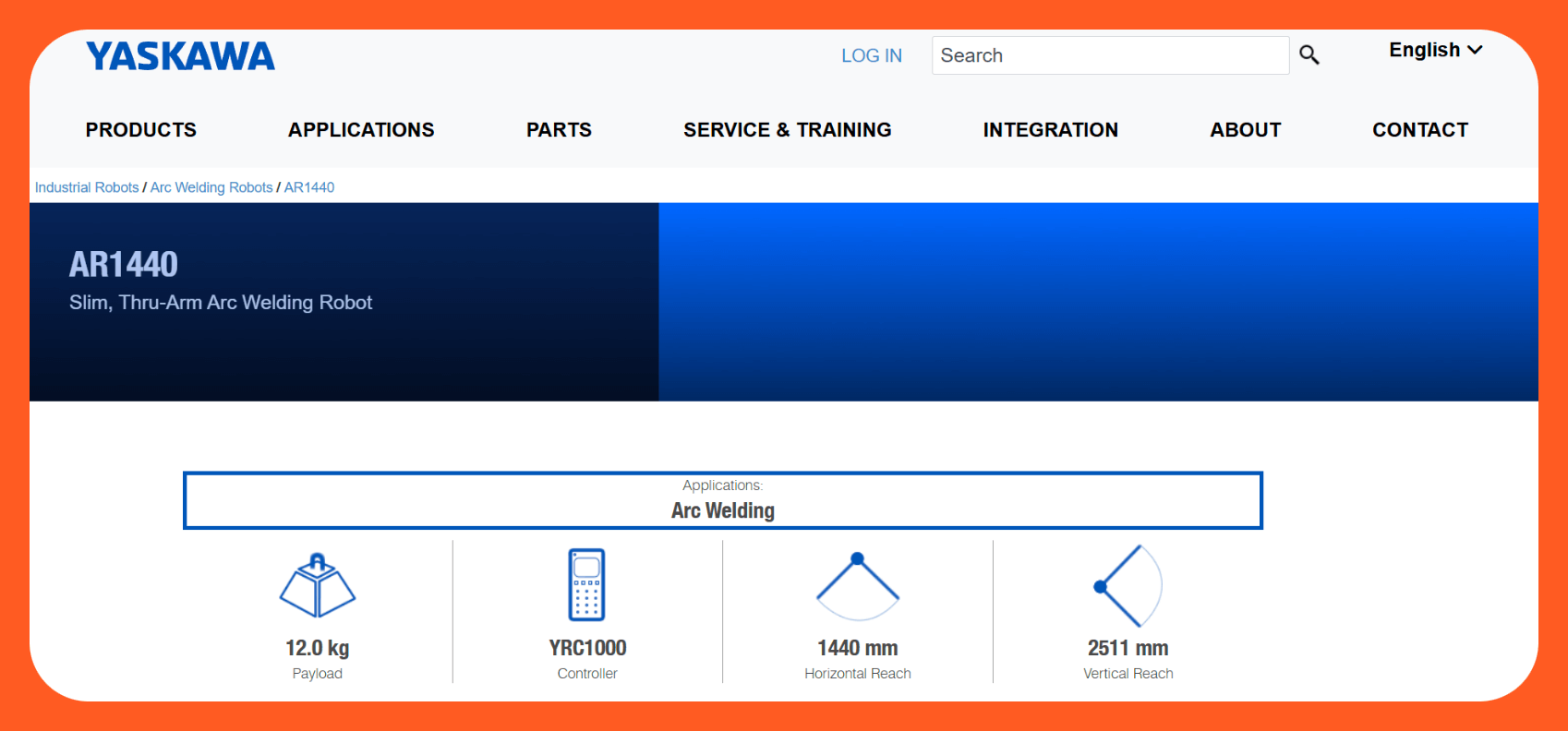
This compact bot hits the sweet spot for precision and speed, especially for smaller parts or trickier welds that still need industrial-grade quality.
Who it’s for: Mid-size metal shops, job shops, or anyone building complex weldments where clunky bots just won’t fit.
Why is it worth the hype?
- Super compact form: Fits in setups most bots would cry at
- 1440 mm reach: Covers a lot of ground for a small frame
- 12 kg payload: Not a brute, but it can definitely weld
How much are we talking?
Usually $25,000–$35,000, depending on accessories.
5. Universal Robots UR10e + Welding Kit — Best plug-and-weld setup for beginners
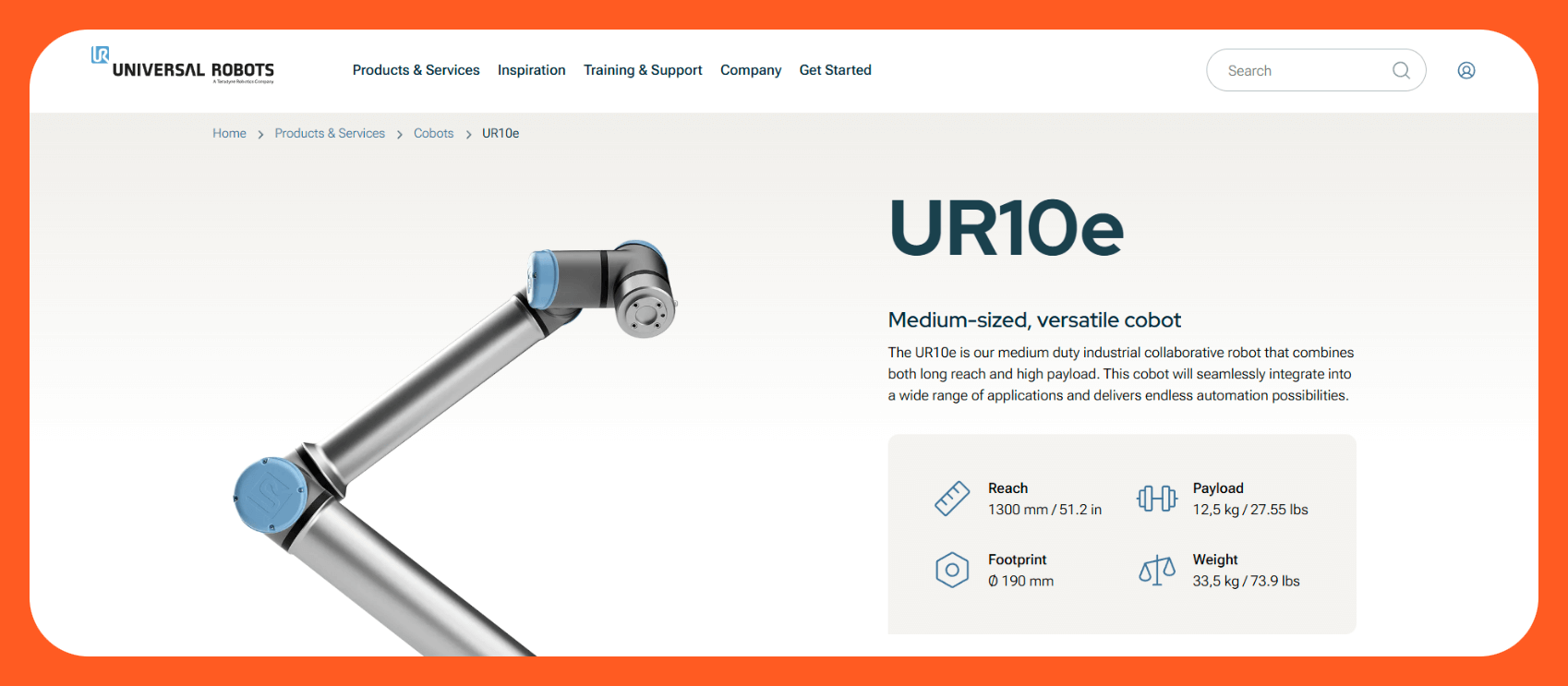
A collaborative robot welder that turns welding into something you can actually learn in a weekend. Add a welding kit from companies like Hirebotics or Vectis, and you’ve got a low-hassle starter system.
Who it’s for: Smaller shops that want to automate welding without reinventing their entire floor plan or hiring a robot whisperer.
Why is it worth the hype?
- Built-in force feedback: Detects pressure and adjusts
- Drag-and-drop UI: Literally teach by moving the arm
- Upgrade path: Scales well with third-party kits
How much are we talking?
UR10e is around $30,000–$50,000, welding kit adds $10,000–$25,000.
Summing up
The types of welding robots available in 2025 span from simple cobots to the flashiest, advanced multi-axis industrial arms. The best one isn’t the flashiest, it’s the one that nails your welds, doesn’t complain, and won’t bankrupt your floor manager’s soul.
Each robot offers specific capabilities for different materials, weld types, and factory needs. Meanwhile, costs range from a cool $25K for entry-level setups to real head-turners at $250K+ for full cells.
You’ll need to consider factors like part geometry, material tolerance, floor space, and your staff’s expertise to choose the right system.
Why you should care: Maybe you're eyeing a full robotic welding machine or just dipping into cobots, but the tools are smarter, cheaper, and actually usable, even if your crew still thinks ChatGPT is a crypto coin.
The real move? Skip the overpriced megabrands and grab something that welds tight lines, learns fast, and doesn’t lock you into a 900-page manual. Ahem, RO1.
Next steps with Standard Bots’ robotic solutions
RO1 by Standard Bots is the six-axis cobot upgrade your welding line needs to automate smarter.
- Affordable and adaptable: Best-in-class automation at half the price of competitors, with a list price of $37K.
- Precision and strength: Repeatability of ±0.025 mm and an 18 kg payload make it ideal for MIG, TIG, plasma, and small-batch fabrication.
- AI-driven and user-friendly: No-code framework means anyone can program RO1. No engineers, no complicated setups. And its AI on par with GPT-4 means it keeps learning on the job.
- Safety-minded design: Machine vision and collision detection let RO1 work side by side with human operators, even on high-heat, high-risk welding applications.
Book your risk-free, 30-day onsite trial today and see how RO1 will go above and beyond competing automation efforts.
FAQs
1. What’s the best welding robot for beginners?
RO1 from Standard Bots is the no-brainer pick. It's a smart robotic welding arm with drag-and-drop programming, built-in AI, and zero need for third-party engineering support. You can set it up between your morning coffee and lunch rush.
2. How much does a robotic welder cost in 2025?
Prices range from $30K for entry-level cobots to $90K+ for full-blown robotic welding machines. RO1 sidesteps the sticker shock, it's available for $37K (list price), and that’s half the cost of comparable systems.
3. Can you weld aluminum with a robot?
Totally, but not all systems handle it well. Aluminum needs tighter heat control and cleaner feeding. Types of welding robots like RO1 and the UR10e can manage aluminum if paired with the right MIG or TIG setup.
4. Do robotic welders need programming experience?
Not anymore. RO1, for example, uses a no-code interface that even your least techy shop guy can master. Most modern robot welders are designed to be trained by moving the arm, not writing scripts.
5. What’s the difference between a cobot and an industrial welding robot?
Cobots (like RO1) are designed to work with humans; they’re safer, easier to program, and usually cheaper. Traditional or industrial robotic welding machines are bigger, faster, and locked into fenced-off zones. Pick your fighter based on volume and footprint.
Join thousands of creators
receiving our weekly articles.