Robotic arm mechanisms are everywhere, from factory floors and surgical suites to research labs and theme parks.
Robotic arms work by performing complex, repetitive, or high‑precision tasks with consistent accuracy. Whether you’re buying, designing, or programming one, it’s important to understand the components, motion systems, and control methods that power them.
What is a robotic arm mechanism?
A robotic arm mechanism is a mechanical device built to mimic the movements of a human arm, only faster, stronger, and far more precise. Made up of segments connected by joints, it moves in multiple directions and can be programmed for anything from simple pick‑and‑place work to delicate surgical procedures.
It combines mechanical, electrical, and software systems to bring that motion to life, whether you need high speed, heavy payload capacity, or surgical‑level precision for complex, repeatable tasks.
Core components of a robotic arm mechanism
The core components of a robotic arm mechanism include the base, joints, links, wrist mechanism, and end effector.
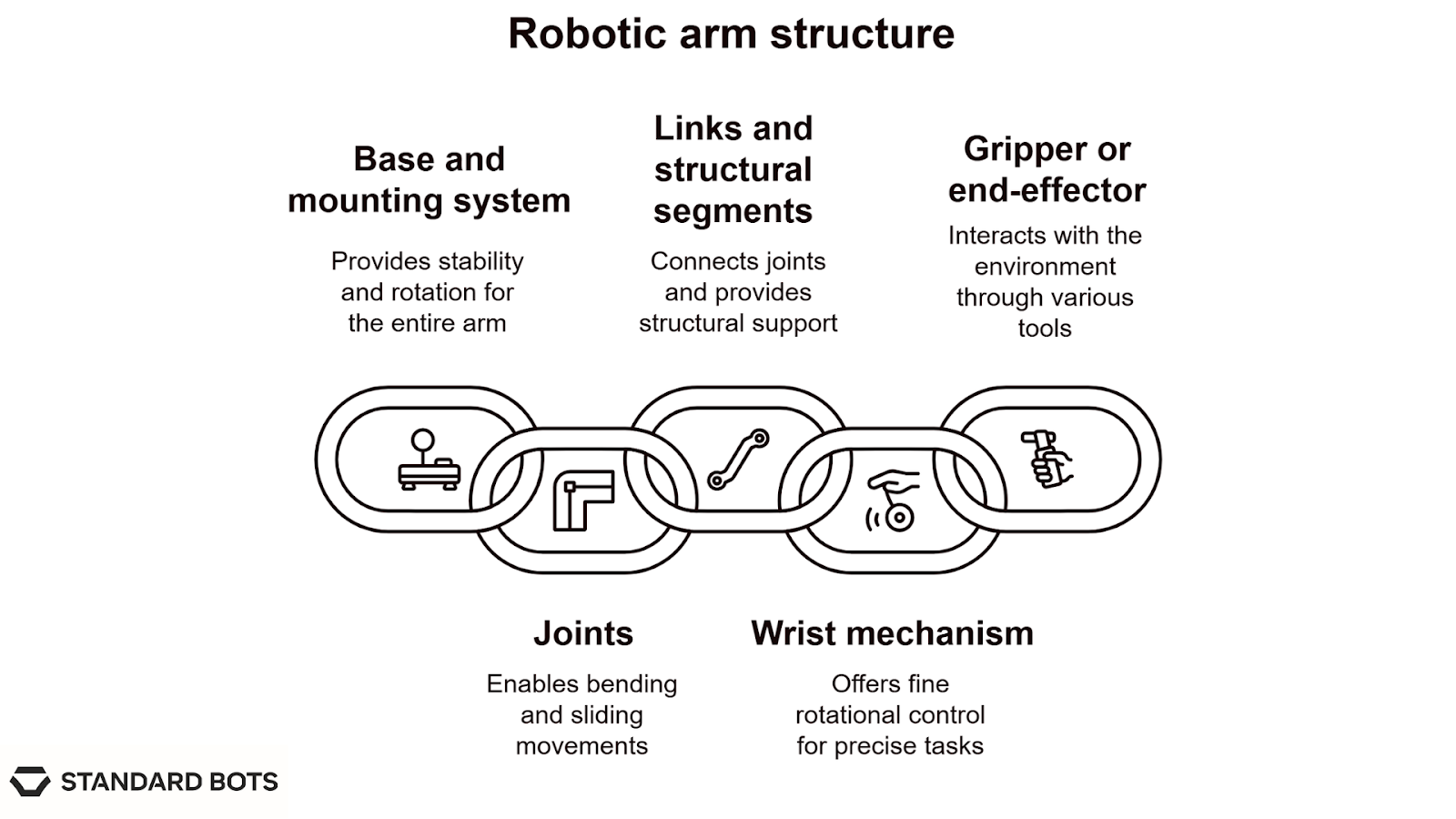
Let’s break down the main parts of the mechanism.
1. Base and mounting system
The base anchors the arm and often contains motors for rotating the entire unit. In factory setups, the base may be bolted to a floor, pedestal, or track system to enable mobility. The stability and torque handling of the base directly affect how precisely the rest of the arm can operate.
2. Joints (rotational, prismatic, or hybrid)
Joints define how the arm bends or slides. Most arms use rotational joints (revolute), allowing movement like a shoulder or elbow. Others may include prismatic joints that enable linear extension. Complex arms often combine multiple joint types to increase dexterity.
3. Links and structural segments
These are the rigid “bones” of the arm, connecting joints. Manufacturers typically make them from materials like aluminum or steel, but lighter alternatives like carbon fiber are growing in use to reduce inertia and improve speed.
For example, this carbon fiber robot arm offers a lighter frame without compromising strength.
4. Wrist mechanism
Positioned near the end of the arm, the robot wrist mechanism adds fine rotational control, often enabling three degrees of freedom (pitch, yaw, and roll). This is vital for tasks requiring precise orientation, such as screwdriving, inspection, or tool alignment.
5. Gripper or end effector
This is where the arm interacts with the world by gripping, welding, painting, or assembling. There are many types of robotic arm grippers, from simple parallel jaws to suction cups, magnetic pads, or adaptive designs for irregular objects.
Movement and kinematics
Movement and kinematics determine how a robotic arm translates joint rotations into precise end effector positioning.
A robotic arm follows a precisely calculated path defined by the system’s structure and math. This coordination of joints and links is governed by kinematics, the foundation of all robotic motion.
The first thing to understand is degrees of freedom (DoF), which is a way of measuring how many independent motions an arm can make. A basic 3-axis robot arm offers three directional movements and is well-suited for simple, repetitive actions like stacking or sorting items along a fixed path.
But when a task demands more flexibility, more axes are needed. A 7-axis robot arm, for example, behaves more like a human limb. It can bend, rotate, and reach around obstacles without having to reposition the base. This makes it ideal for workspaces or tasks where tool orientation needs constant adjustment mid-process.
To make these motions possible, engineers use two types of kinematic models:
- Forward kinematics calculates the position of the gripper based on known joint angles.
- Inverse kinematics works in reverse. When given a target location, it computes the angles each joint must take to reach it.
This math allows robotic arms to perform tasks like welding curved seams, inserting parts into tight assemblies, or following precise motion paths in real time.
The layout of joints also matters. In a jointed arm robot, movement is highly versatile, which is perfect for painting contoured surfaces, navigating awkward angles, or performing tasks with varying orientations. Combined with smart path planning, this setup defines the full range and smoothness of robotic arm movement.
Gripping mechanisms and versatility
The gripper or end effector is what turns a robotic arm into a working tool. It’s the part that physically handles objects, and the type of gripping mechanism you choose directly shapes the robot’s capabilities.
The most common option is the mechanical gripper mechanism, which uses jaws or fingers to grip an object. These are ideal for structured tasks involving consistent part sizes like bin picking or automated assembly. For softer or irregular items, adaptive grippers offer more flexibility by adjusting their grip using compliant materials or shape-conforming fingers.
Other common types include:
- Vacuum grippers, which lift items using suction, are ideal for packaging materials, electronics, or flat components.
- Magnetic grippers, which move ferrous parts without applying pressure, are useful in metalworking or environments where clamping isn’t practical.
In high-mix production environments, versatility is key. This is where quick-change gripper systems make a difference. They let operators swap tools in seconds with no manual recalibration or coding changes. This saves a lot of time in packaging, inspection, or assembly lines.
Most modern arms are modular by design. A well-integrated robotic arm gripper mechanism can evolve with your production setup, supporting tool changes, new materials, or tighter tolerances over time. That’s why understanding how the gripper fits into the larger system is essential.
The gripper also plays a huge role in factory robot arm performance, where speed, uptime, and safe handling are non-negotiable.
Actuation and motor control
At the heart of every robotic arm mechanism is its actuation system that drives joint movement. These motors determine how fast, how accurately, and how smoothly the arm operates. Selecting the right motor setup involves balancing torque, precision, speed, and cost.
The two main motor types are servos and steppers.
Servos give real‑time feedback for precise, adjustable motion in tasks like welding, surgery, and precision machining. Steppers move in fixed increments without feedback, offering lower precision but simpler, cheaper operation for predictable, repetitive jobs like pick‑and‑place or inspection.
In heavy-load or high-torque environments, the type of drive system also matters:
- Direct drive motors offer smooth motion with fewer mechanical components, which reduces backlash and wear.
- Geared motors, on the other hand, increase torque output and are better suited for lifting heavier payloads, though they introduce more complexity.
Actuation is about controlled movement. Motors work alongside encoders, force sensors, and control software to ensure that every motion is executed with the right force, direction, and timing. Whether it’s gripping a fragile object or applying consistent pressure in a weld, this coordination is what separates basic motion from reliable, repeatable performance.
Sensors and feedback systems
For a robotic arm to move with consistent accuracy, it needs real-time awareness. That’s where sensors provide constant feedback about the arm’s position, force, and surroundings, allowing it to adjust its actions on the fly.
- Force and torque sensors: These sensors monitor how much pressure the arm applies when gripping, inserting, or assembling parts. This prevents issues like over-tightening, dropped items, or component damage during tasks that involve tight tolerances or delicate materials.
- Encoders: Positioned on each axis, encoders measure rotational position and speed. They give the control system an exact reading of where every joint is at any moment. This is essential for accurate robotic arm movement in multi-axis systems.
- Tactile sensors: Often integrated into the robotic arm gripper mechanism, tactile sensors simulate the sensation of touch. They’re handy in environments like lab automation or electronics assembly, where the robot must hold fragile or oddly shaped items with care and adjust grip pressure dynamically.
- Vision systems: Cameras, LiDAR, or structured light sensors help the robot detect objects, identify their orientation, and inspect surface quality. With machine learning, these vision systems also adapt to part variation or unstructured layouts, enabling flexible automation even in non-repetitive environments.
The control system processes sensor data in real time to adjust motor actions and decision-making. This closed-loop system ensures that the robot doesn’t just follow a programmed path.
Programming and control
The performance of a robotic arm depends heavily on how it’s programmed. Behind every smooth, coordinated movement is a control system that translates instructions into precise motion.
- Teach pendants: Many robotic arms come with a teach pendant, a handheld device that lets operators manually move the arm through a task. The system records each position and replays it during operation. This method is fast, intuitive, and well-suited for repetitive processes like packaging, sorting, or palletizing.
- Robot-specific languages: More advanced systems use dedicated programming languages tailored to the hardware. These include:
- RAPID (ABB)
- KRL (KUKA)
- URScript (Universal Robots)
These languages provide low-level control over motion planning, I/O operations, sensor data, and safety logic, making them essential for customized industrial workflows.
- General-purpose languages: Some platforms support languages like Python or C++, allowing robotic arms to be integrated with external systems, databases, or vision tools. This is especially useful in research, flexible automation setups, or AI-powered applications where real-time data exchange is critical.
Engineers now program and test many robotic arms in virtual environments. Simulation tools help map out motion paths, identify collisions, and optimize cycle times, reducing risk during deployment.
Applications and industry examples
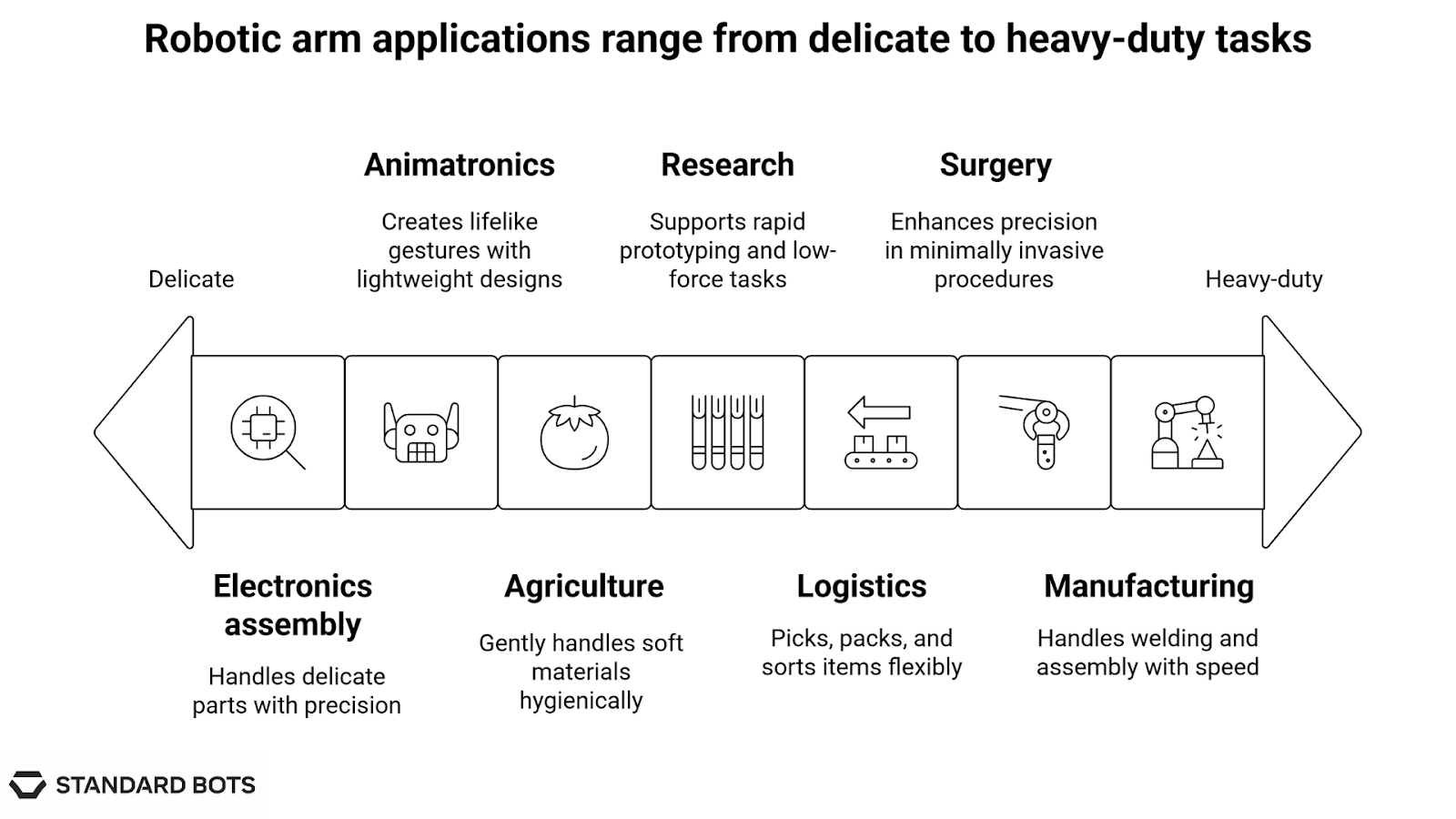
Here’s how robotic arms work across industries:
- Manufacturing and automation: Robotic arms handle welding, assembly, pick-and-place, and machine tending with speed and precision. With the right gripper mechanism, they can switch between parts or tools to improve uptime and throughput. These arms prioritize durability, repeatability, and payload handling.
- Surgery and medical robotics: In minimally invasive procedures, robotic arms enhance precision with articulated joints and force feedback. Their robotic arm movement is smooth and stable, often operating with sub-millimeter accuracy, helping surgeons perform with better control and less fatigue.
- Electronics assembly: For small, delicate parts like microchips and circuit boards, robotic arms use vacuum or magnetic grippers. Their motion is tightly controlled to reduce static, damage, or misalignment. Vision-assisted alignment is common in high-precision setups.
- Animatronics and expressive robotics: Animatronic arm mechanisms are built for lifelike gestures, not heavy lifting. Lightweight, compact designs enable smooth robotic arm movement, often used in displays, theme parks, or humanoid robots for expressive motion.
- Logistics and sorting: In warehouses, robotic arms pick, pack, and sort items using adaptive grippers and vision systems. These tasks demand flexibility and fast reprogramming, making modular robot gripper mechanisms a key advantage.
- Agriculture and food processing: Arms here need to be hygienic and gentle. While harvesting produce or packing items, the gripping mechanism must handle soft materials without damage while still maintaining output speed.
- Research and labs: In lab automation, robotic arms carry out sample prep, pipetting, and sorting. Modular robot arm parts and programmable joints support rapid prototyping and repetitive, low-force tasks.
Maintenance and design considerations
Final thoughts: Why the mechanism matters
A robotic arm is a programmable machine built to move with precision and consistency, often outperforming human capability in speed, strength, and accuracy. It works by coordinating its structural parts, motion systems, and control software to carry out specific tasks.
Joints and links provide movement, motors drive that motion, and sensors feed real-time data, so the arm can adjust on the fly. Programming methods, whether through manual teaching or code, define how it responds to instructions and adapts to different tasks.
When designed for durability and maintained properly, a robotic arm can operate reliably for years, handling anything from heavy manufacturing work to delicate surgical procedures. Its adaptability means it can be re-tooled or re-programmed for new applications, making it a long-term investment for industries that depend on precision, efficiency, and repeatable results.
Next steps with Standard Bots
Looking to upgrade your automation game? Standard Bots’ RO1 is the perfect six-axis cobot addition to any factory setup, delivering unbeatable precision and flexibility.
- Affordable and adaptable: RO1 costs $37K (list price). Get high-precision automation at half the cost of traditional robots.
- Precision and power: With a repeatability of ±0.025 mm and an 18 kg payload, RO1 handles even the most demanding CNC jobs.
- AI-driven simplicity: Equipped with AI capabilities on par with GPT-4, RO1 integrates seamlessly with CNC systems for advanced automation.
- Safety-first design: Machine vision and collision detection mean RO1 works safely alongside human operators.
Book your on-site demo with our engineers today and see how RO1 can bring AI-powered greatness to your shop floor.
FAQs
1. How do I choose between a servo and a stepper motor for my robotic arm?
Servo motors are better for high-precision tasks that require feedback and dynamic adjustment, like welding, inspection, or delicate assembly. Stepper motors are simpler and more cost-effective for fixed, predictable movements. Choose based on how much precision and responsiveness your application needs.
2. What safety standards apply to industrial robotic arms?
Safety standards that apply to industrial robotic arms are ISO 10218-1 and ISO 10218-2 standards for robotic safety. Additional certifications like CE, UL, or ANSI/RIA may apply depending on the region. These standards cover things like emergency stops, collaborative zones, and collision detection systems.
3. Can I swap grippers on a robotic arm without redesigning the whole system?
Yes, you can swap grippers on a robotic arm without redesigning the whole system. Many modern arms support quick-change gripper mechanisms, allowing you to switch tools without modifying the core structure. Just ensure compatibility with the arm’s flange type, payload limits, and control interface.
4. How much payload can a SCARA robot arm typically handle?
A SCARA robot arm typically handles payloads between 2 and 20 kilograms, depending on reach and motor configuration. Heavier-duty variants can go higher, but may sacrifice speed or precision.
5. Which programming languages are most common for robotic arm control?
Programming languages for robotic arm control may vary. ABB uses RAPID, KUKA uses KRL, and Universal Robots uses URScript. Many newer systems also support Python or C++ for easier integration with broader software platforms.
6. Why does kinematics matter for the accuracy of a robotic arm?
Kinematics matters for the accuracy of a robotic arm. It defines how joint movements translate to the position of the end effector. Accurate inverse kinematics ensures the arm reaches the right location every time. This is important in tasks like machining, surgery, or tight-tolerance assembly. Poor kinematic models lead to positional errors and inconsistent performance.
Join thousands of creators
receiving our weekly articles.