Welding has had its glow-up — and plasma arc welding is part of the reason. By (literally) turning up the heat, plasma arc welding delivers tighter welds, deeper penetration, and cleaner seams on tricky materials like stainless steel or titanium.
Still wondering, “What is plasma welding?” and why manufacturers are adding it to their lines? We’ll break down everything welding-related like an ionized gas — and dish out info on the best cobot for the job.
We’ll cover:
- What is plasma arc welding?
- The plasma welding process and how it works
- Automation and robotic integration
- Plasma arc welding vs. other welding methods
- When to use plasma welding and choosing the right system
- Plasma arc welding: advantages and limitations
- The future of plasma welding in manufacturing
What is plasma arc welding?
Also known as PAW welding, the plasma arc welding process uses a superheated, constricted arc of plasma to melt metal with darn-near-surgical precision. The result? Narrow, deep welds that look like they were drawn on with a laser pointer. Imagine TIG welding, but with more edge, more heat, and more control — that’s PAW welding.
Here’s where it gets spicy: Plasma is the fourth state of matter — past solid, liquid, and gas. It’s what happens when gas gets so energized that its atoms lose their chill (and their electrons).
This is what makes a plasma arc hit harder than standard arc welding — it’s basically a lightning bolt you can control.
Key terms that’ll come up a lot:
- Plasma arc: The actual ionized gas that delivers the welding heat.
- Plasma welding: A more intense and controlled form of arc welding using a constricted nozzle and torch design.
- PAW welding: The acronym for plasma arc welding — you’ll see this in technical docs and robotic welding machine specs.
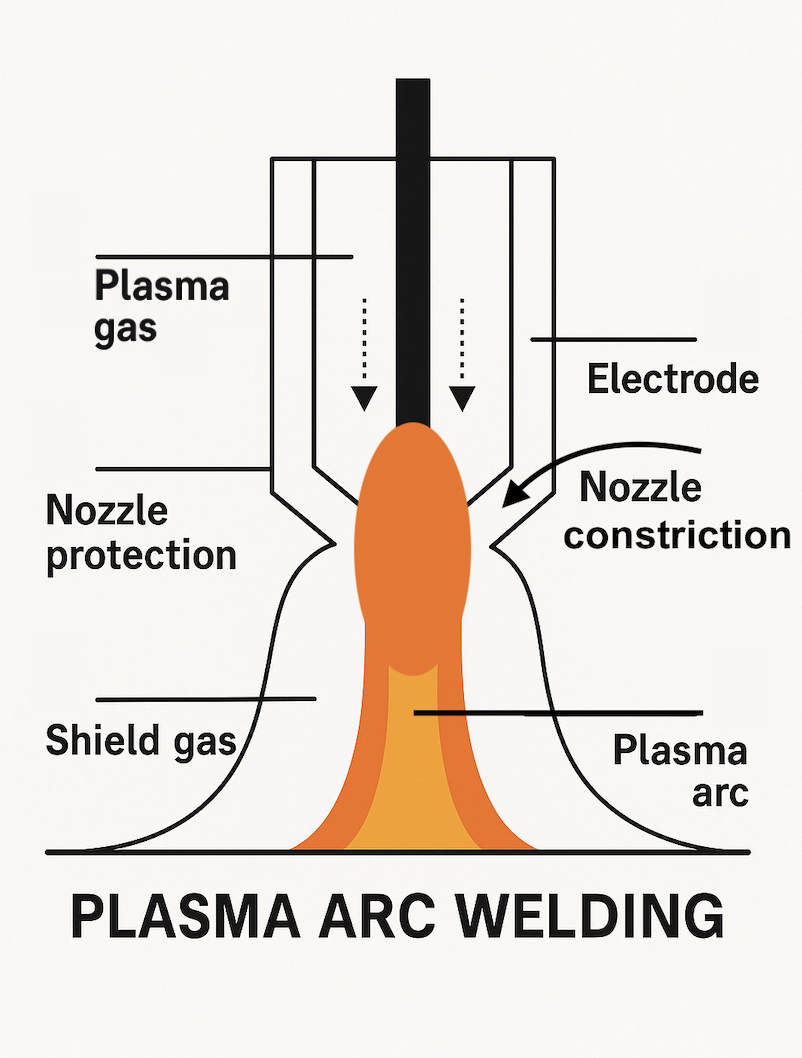
Plasma welding might not be as mainstream as MIG or TIG, but it's already carving out a solid niche in industries where precision is everything — from aerospace fuel lines to surgical-grade stainless steel parts.
It’s also much more compatible with cobot end effectors for manufacturers itching to automate the process without jumping through hoops.
The plasma welding process: How it works
In PAW welding, plasma goes through a tiny nozzle — and melts metal like it’s butter on a frying pan. Controlled. Precise. Kinda terrifying. Very cool.
Here’s how plasma arc welding gets down to business:
- Pilot arc goes bzzzt: It kicks things off with a tiny, low-current arc between the electrode and the nozzle. This doesn’t weld — it just preps the gas to go full plasma mode.
- Full arc engagement: Once the pilot arc stabilizes, the real arc jumps to the metal. This is where the magic (and melting) happens.
- Double-gas strategy: Plasma gas forms the arc. Shielding gas protects it. Argon, helium, hydrogen — it’s like a tiny chemistry party right at the weld pool.
- Heat with precision: The arc gets squeezed through a nozzle so tight it could cut through your soul. But mostly it just delivers concentrated heat with very high accuracy levels.
- Guided motion: CNC or robot arms glide the torch along the weld — it’s like poetry in motion, even if it’s (never) 100% flawless, but it does reach 99%.
Here are the components that every plasma welding rig is rockin’:
Automation and robotic integration
Let’s be real — plasma arc welding sounds like a dream, but babysitting it isn’t. That’s why manufacturers are handing it off to the one teammate who never takes lunch, never blinks, and doesn’t flinch at 20,000 to 30,000 °C. The robot.
Plasma welding and automation are a strong match — not because robots are flawless, but because they’re way better at maintaining consistency when the setup is tight and the process is repeatable.
Why plasma + robots = chef’s kiss:
- Solid consistency with less fatigue risk: While even robots need maintenance and recalibration, they tend to deliver more consistent welds over long runs compared to humans — especially in high-volume production.
- Better heat management through controlled motion: Plasma can run hot and intense, but a robot’s steady movement helps reduce distortion and keeps those welds cleaner — assuming your setup's dialed.
- Safe collaboration with cobots: In setups where cobots are integrated, humans and robots can safely share workspace. Just don’t expect the robot to instinctively dodge elbows — that’s what sensors and safety zones are for.
- Process visibility through monitoring: Robotic plasma systems often support real-time parameter logging (like arc time, travel speed, and heat input), helping engineers fine-tune the process without guesswork.
- Less reliance on highly specialized welders: Plasma welding isn’t beginner-friendly, but automation reduces how much knowledge of welding folklore is required. You still need a skilled operator — they’re just programming the weld instead of manually executing it.
Plasma arc welding vs. other welding methods
There’s no single “best” welding method — only the best one for the job. Plasma arc welding (PAW) shines when the spec sheet screams “no room for error,” but there are plenty of times you’d be better off with good ol’ MIG or TIG.
Here’s how plasma compares in the robot battle royale of welding:
Plasma’s biggest flex? That sweet middle ground between TIG quality and laser-level control — without requiring a moonshot budget or a full R&D department to run it.
When to use plasma welding
Not every weld needs that extra level of precision — but for the ones that do, plasma arc welding is hard to beat.
It’s a little extra compared to MIG or TIG, but that “extra” pays off when the part has to survive a rocket launch, a surgery, or 1,000 hours of vibration testing.
When plasma earns its keep on the shop floor:
- When you’re working with tough or exotic metals: Titanium, Inconel, stainless steel — PAW handles them without flinching (as long as your setup’s right).
- You need tight control on thin materials: Plasma’s narrower arc and focused heat input mean less distortion and cleaner welds on delicate parts.
- Your parts need to look as good as they hold: Aerospace and medical-grade components can’t afford cosmetic flaws — plasma’s precision helps meet both function and form standards.
- Repeatability matters: For high-volume runs where the weld has to be the same every time, PAW can provide more consistent results than some manual methods — especially when automated.
- Deep joints or tight corners? Yeah, plasma: Plasma’s constricted arc lets you reach spots other processes might burn or under-penetrate.
Plasma welding isn’t the default — but in industries like aerospace, automotive, and medical devices, it’s often the big-brain choice.
Plasma arc welding: advantages and limitations
Plasma arc welding doesn’t play around — it delivers elite weld quality when precision, control, and depth are the absolute minimum requirements.
But like any high-performance tool, it has quirks, costs, and limits that might not vibe with every factory setup.
Let’s run through the pros and cons before you fire up the torch:
Best-case scenarios? Complex parts, high-spec materials, and environments where automation thrives. But if you’re just spot welding mild steel brackets all day? MIG works perfectly fine.
Choosing the right plasma welding system
Buying a plasma welding setup isn’t like picking a toaster — you’re not just looking for something that gets hot and doesn’t explode. You’re investing in a system that fits your material, your throughput, and how much automation you want to bake in.
Here’s what actually matters when shopping for a plasma welding system:
- Power range: Don’t max out for fun. Match your output to the material and duty cycle — welding sheet metal doesn’t need a 300A beast.
- Duty cycle and cooling: If you're planning to run non-stop, go water-cooled and look for a high-duty cycle rating. Otherwise, prepare to wait out cooldowns like it’s 1997 dial-up.
- Gas types and compatibility: Argon, helium, hydrogen — different combos yield different results. Get a machine that plays nice with the gas you actually plan to buy and can afford.
- Automation compatibility: Planning to automate TIG welding down the line? Make sure your plasma system supports remote operation, CNC or robot control inputs, and modern feedback loops.
- Integration with robotics: Robots don’t just “plug in” — they need coordination. That’s where understanding how robotic arms work helps you buy smarter and avoid buyer’s remorse on day two.
- Support, not just specs: All the bells and whistles in the world mean nothing if the vendor vanishes when your torch throws an error code mid-shift.
The future of plasma welding in manufacturing
Plasma welding isn’t fading into retirement — it’s hitting the gym. Between AI upgrades, robotic compatibility, and hybrid tech mashups, plasma arc welding is carving out a whole new role in the smart factories of the future.
What’s actually next for plasma arc welding:
- Smarter systems that adapt in real time: New PAW machines are starting to include closed-loop feedback and machine learning to tweak heat input and travel speed on the fly. Less guesswork, more precision. One study published in The International Journal of Advanced Manufacturing Technology showed how AI can predict keyhole stability in plasma welding — yeah, that’s a thing now.
- Hybrid welding setups are becoming legit: Plasma + MIG or plasma + laser setups are letting manufacturers get creative with how they handle difficult materials and weld profiles. A more metal type of fusion cuisine.
- Cobots are getting cozy with plasma torches: Collaborative robots are starting to handle plasma arc welding tasks in environments where big, fenced-off cells would’ve been overkill.
- Demand’s heating up: The global market for plasma welding is projected to hit $2.1 billion by 2032, riding that sweet 6.0% CAGR. Why? Because manufacturers want deeper welds with cleaner edges — and plasma loves delivering just that.
Summing up
Plasma arc welding is a powerful, highly precise process that’s finally getting the recognition (and tech) it deserves. PAW uses a superheated plasma arc for accurate, deep welds, and is ideal for high-spec jobs like aerospace and medical parts. It’s more a lot more complex and pricey than MIG or TIG, but PAW excels in automation and consistency.
But it ain’t a fix-it-all solution: It takes a tuned setup, operator knowledge, and smart equipment choices to make it shine. That’s where automation and cobot integration are making the difference — dumbing down the complex stuff and making PAW more accessible to modern production floors.
Plasma arc welding has evolved into serious contender territory — not just for elite aerospace projects, but for any manufacturer ready to weld smarter.
Next steps with Standard Bots
RO1 by Standard Bots is the six-axis cobot upgrade your factory needs to get in on the automation action.
- Affordable and adaptable: Best-in-class automation at half the price of competitors; leasing starts at just $5/hour.
- Precision and strength: Repeatability of ±0.025 mm and an 18 kg payload make it ideal for CNC machine tending, welding, material handling, and a lot more.
- AI-driven and user-friendly: No-code framework means anyone can program RO1 — no engineers, no complicated setups. And its AI on par with GPT-4, which means it keeps learning on the job.
- Safety-minded design: Machine vision and collision detection let RO1 work side by side with human operators.
Book your risk-free, 30-day onsite trial today and see how RO1 can take your plasma welding operations — and everything else — to the next level.
Join thousands of creators
receiving our weekly articles.