Still asking what is Industry 5.0 or what the industry 5.0 meaning even is? Industry 5.0 is what happens when robots stop replacing people and start teaming up with them instead.
It’s the shift away from fully autonomous systems — and toward factories where people and machines actually play nice. We’re talking cobots, AI-powered production lines, and factories that don’t treat humans like slow-moving peripherals.
What is Industry 5.0?
Industry 5.0 is the next step in manufacturing, where humans and smart machines work together instead of getting in each other’s way. It’s not just automation 2.0. It’s a total reframe of how we build, assemble, and create.
So what is Industry 5.0, really? It’s the 5th Industrial Revolution, and it’s all about bringing manufacturing into an era where personalization, speed, and human control matter just as much as reliability, quality, and productivity.
Industry 5.0 centers around one thing: human-centric automation. Picture people working alongside collaborative robots (cobots), assisted by AI, and making products faster, safer, and more personalized than ever.
Unlike Industry 4.0, which was all about sensors, big data, and full digitization, Industry 5.0 manufacturing puts people back in the loop. You get the tech benefits without turning your factory into a sealed-off robot zoo.
Want to see how that’s already playing out? Take a look at what the future of robotics in manufacturing looks like — and yeah, it’s real.
Core principles of Industry 5.0
At its core, Industry 5.0 is about better intent. The goal is smarter production that lets humans come back into the room.
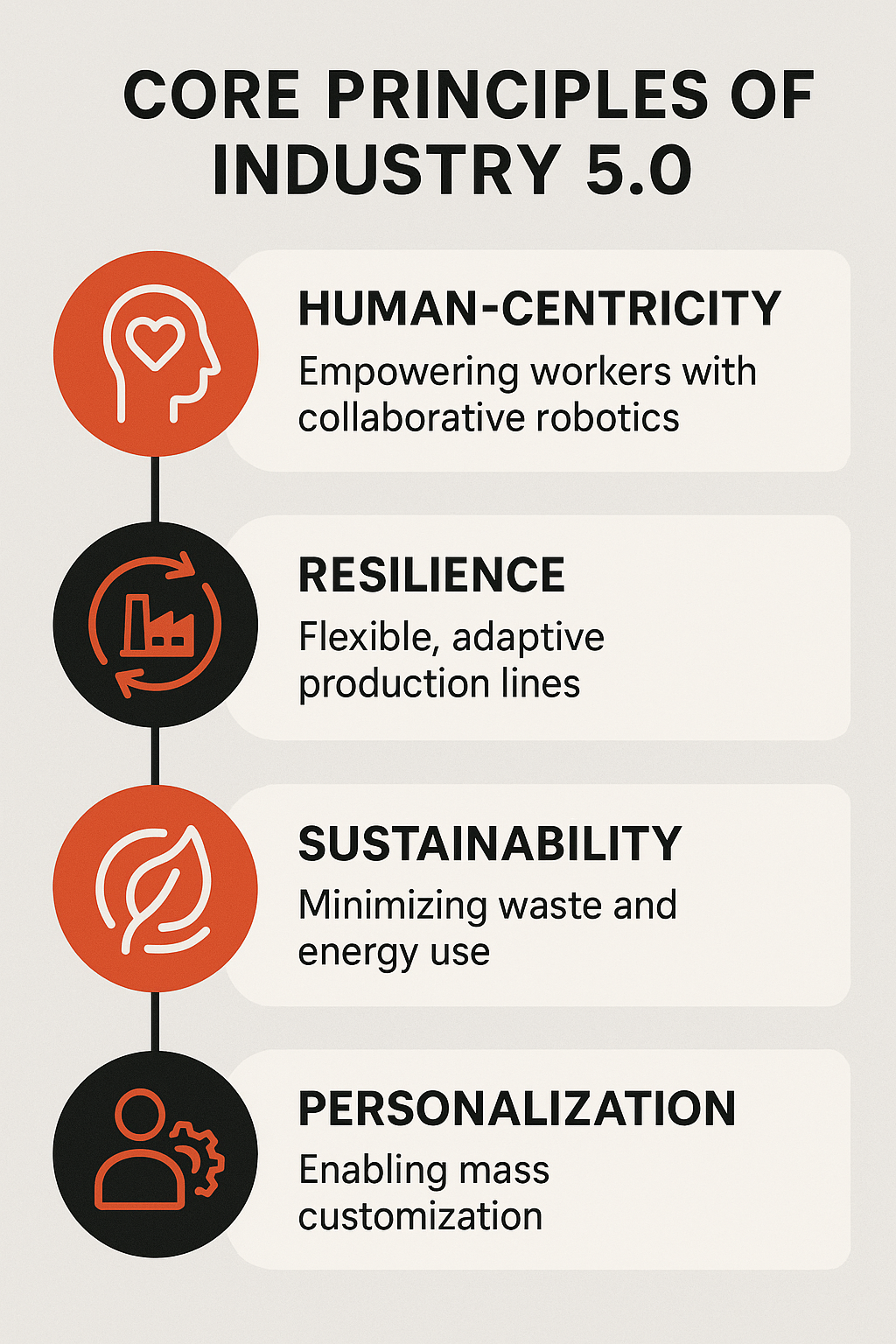
The pillars holding up the 5th Industrial Revolution
- Human-centricity: The biggest shift in Industry 5.0 manufacturing is putting people back in control; not just pushing buttons, but working with tech that actually adapts to them. Cobots, for example, aren't stealing jobs; they’re handing you the glue gun (then doing the boring parts). Take a look at how cobots work in real life.
- Resilience: Instead of designing systems that fall apart the second a sensor fails, Industry 5.0 builds for the unpredictable — flexible workcells, modular robots, and AI that reroute around the mess. You’re not stopping the line because someone changed a part.
- Sustainability: Expect way less waste and way smarter energy use. Smarter dosing, more efficient sanding, fewer “spray-and-pray” processes. (Looking at you, compressed air line.)
- Way more personalization: With cobots and AI on your side, it’s suddenly possible to produce high-mix, low-volume goods without turning the entire floor upside down. That’s real technology in the industrial revolution … but you know, 2025 — and beyond, if you check out these predictions.
Industry 5.0: Key enabling technologies & examples
Industry 5.0 runs on seriously high-end tech. What makes this one different is how these tools support people in real time, not just there to optimize spreadsheets or look cool with investors.
Real-world enablers powering Industry 5.0
- Cobots are literally in there with you: These aren’t factory arms locked in cages. Cobots work with people, handing off different jobs, reacting to motion, and not knocking you out in the process. For example, Standard Bots’ RO1 can swap between sanding, gluing, and CNC tending, alongside quite a few others.
- AI that makes good calls: Not just predictive maintenance. We’re talking dynamic rescheduling, adaptive flow control, and systems that think with you, not ahead of you.
- Digital twins you can break without calling maintenance: Build it digitally, break it digitally, then go live. For instance, SAP reports that 63% of manufacturers using digital twins reduce downtime by over 30%. Workers can test workflows, check loadouts, or simulate entire shifts without touching a part.
- Put on your AR goggles: Forget binders. AR overlays give real-time instructions, maintenance prompts, and alerts, right in the operator’s field of view. No scrolling. No guessing.
- Edge computing with zero lag: When milliseconds matter, cloud lag doesn’t cut it. Edge devices keep things local, which means faster reaction times and tighter human–machine sync.
Real-world examples of industrial technology like this are already live, in automotive paint lines, electronics assembly cells, and even high-speed bottling plants.
Industry 4.0 vs. Industry 5.0
Industry 4.0 got us data, automation, and smart machines, but it also kind of forgot about the humans. It was all, “Let’s connect everything to the cloud,” and suddenly operators were just … there. Watching dashboards.
Industry 5.0 hits different: It doesn’t kill the tech, it uses tech to make actual people more powerful. Not just by giving them tools, but by making the machines worth working with.
Industry 5.0 doesn’t make Industry 4.0 irrelevant, it patches the parts that made factories cold and weird. And if you’re curious what 4.0 got right (and wrong), this breakdown of Industry 4.0 benefits and the real Industry 4.0 challenges are both worth an in-depth read.
Benefits and challenges of Industry 5.0 adoption
Industry 5.0 benefits productivity, quality, morale, safety, and sustainability by pairing human skills with automation.
However, 5.0 brings challenges like high upfront costs, a steep skills gap, more cybersecurity risks, slow regulatory adaptation, and heavy reliance on quality data.
Let’s look at these in detail:
Which industries will benefit most from Industry 5.0?
If your industry makes things — fast, flexibly, or with people still involved — Industry 5.0 is probably headed your way.
Where are the biggest upgrades already landing?
- Supply chains that got roasted in 2020: Human–AI co-planning, edge tracking, and dynamic re-routing are making supply networks actually bend without snapping.
- Manufacturers stuck in 4.0 autopilot: Swapping out “fully automated but rigid” for “collaborative and responsive,” especially in mid-size factories where downtime still hurts.
- Health care without the fuss: Collaborative robots in labs, automated sample prep, and diagnostic cobots that assist (not replace) technicians. Still human-led, just less error-prone.
- Green tech that scales: From custom solar panel configurations to sustainable packaging lines, 5.0 helps make personalized green products … without tanking margins.
6 Steps to implement Industry 5.0 on your shop floor
You don’t need to tear your factory apart to get started — just start smarter. Here’s how to move from 4.0 to 5.0 without throwing your whole setup in the trash.
A step-by-step rollout plan that works
- Map where you’re at: Audit your current automation, team skills, and system flexibility. If everything still runs on spreadsheets and duct tape, start there.
- Set some attainable, real-life goals: Don’t aim for “more synergy.” Define clear human–machine goals, e.g., shorter cycle times, better uptime, safer handoffs, etc.
- Pick your bots wisely: Choose collaborative platforms that work with what you’ve got, like RO1, which integrates into CNC lines without a hitch.
- Sim before you commit: Use digital twins or basic simulations to preview your line’s response to 5.0 tech before you go live. Fewer regrets, fewer emergency emails.
- Train people like they matter (because they do): Operator-led improvements = fewer errors, better ownership, and no more mysterious UI breakdowns at 3 a.m.
- Track real KPIs: Measure productivity, scrap, energy use, and downtime, not just “vibes.” You need data to know when you’re getting somewhere.
The five industrial revolutions at a glance
Every big leap in manufacturing came with a vibe shift — and sometimes child labor. Here’s the full chaotic (sometimes chaotic evil) arc of the industrial revolutions that got us from spinning wheels to collaborative robots.
1st Industrial Revolution (1760–1840): Steam makes everything loud
Factories go from “small-town workshop” to “literal furnace.” Steam engines power spinning jennies, textile mills, and trains. For the first time, humans harness mechanical energy, and they immediately use it to mass-produce pants and T-shirts.
- Vibe: Coal dust, iron gears, zero safety rails
- Tech in play: Steam power, mechanized looms, early machine tools
- Human role: Still doing everything — just faster, hotter, and covered in soot
2nd Industrial Revolution (1870–1914): Electricity, oil, and the assembly line enter the chat
Now we’ve got power grids, internal combustion engines, and conveyor belts. Factories scale up hard. Ford builds the first moving assembly line and breaks the world. This is when “factory job” becomes shorthand for stability ... and repetitive stress injuries.
- Vibe: Sparks, steel, and company towns
- Tech in play: Electric motors, railroads, chemical processing, mass production
- Human role: Still essential, but now reduced to “repeat this one thing forever”
3rd Industrial Revolution (1950s–2000s): Computers start bossing us around
Automation hits. PLCs, microcontrollers, and CNC machines take over repetitive stuff. Manufacturing gets a brain, and it runs on silicon. This is when technology in the industrial revolution shifts from mechanical to digital.
- Vibe: Beige computers, green screens, and MS-DOS manuals
- Tech in play: Electronics, early robotics, CAD/CAM systems
- Human role: From wrench-wielding to keyboard-poking
4th Industrial Revolution (2010s–early 2020s): Data eats the factory
Machines start talking to each other. IoT sensors track everything. AI predicts when stuff breaks. It’s all optimized, automated, and … a little sterile. Humans mostly monitor and troubleshoot — if they’re still needed at all.
- Vibe: Dashboards, cloud connections, everything in real time
- Tech in play: Cyber-physical systems, big data, cloud, machine learning
- Human role: Pulled out of the process, until something crashes
5th Industrial Revolution (right now): Cobots and humans get a tag team moment
Industry 5.0 brings people back, not as backups, but as collaborators. Cobots help with assembly. AR shows you where to fix things. AI assists instead of replacing. It's the first time factories are designed to work with humans, not just around them.
- Vibe: Clean floors, smart arms, and way less stress
- Tech in play: Collaborative robots, AI decision support, AR, edge computing
- Human role: Central; leveled up, supported, and still calling the shots
How doe Standard Bots enable Industry 5.0?
Standard Bots enables Industry 5.0 by delivering flexible, human-friendly robots like RO1. This cobot safely collaborates with workers, adapts quickly to new tasks, and reduces waste through precision.
If the focus of Industry 5.0 is on collaboration, flexibility, and human-first automation — RO1 arrived ready. It was literally made for this.
How RO1 makes Industry 5.0 doable
- Cobots don’t flinch: RO1 uses vision systems and built-in collision detection to safely operate right next to humans — no cages, less risk, no lawsuits.
- Hot-swap superstar: One operator, some downtime, and RO1’s swapping from sanding to dispensing to CNC tending. That’s what flexibility looks like when you don’t need a full reprogram every time.
- Waste? Don’t know her. RO1’s precise adhesive flow control and hyper-consistent pathing reduce overuse and scrap; a quiet flex that makes your sustainability team love you.
- Downtime, who? Modular parts, remote diagnostics, and AI-driven health checks make RO1 stupidly easy to keep running, or reboot fast when something does go wrong.
- Tech your team won’t hate: The touchscreen interface is actually usable. RO1 doesn’t need a genius-level IQ to operate, just basic logic and someone not afraid to hit “Start.”
FAQs
- What role do cobots play in Industry 5.0?
They’re the glue holding it all together, metaphorically and sometimes literally. Cobots take the repetitive, tiresome stuff off human hands while letting people focus on higher-value work.
- Is sustainability central to Industry 5.0?
Absolutely. Less waste, smarter energy use, better materials handling; sustainability is baked into the structure. Efficient use of tools and smarter decision-making help you hit green goals without slowing production.
- What skills do workers need for Industry 5.0?
No one's asking operators to become AI experts. Instead, it's about confidence with intuitive interfaces, basic diagnostics, and problem-solving alongside machines. Upskilling, not full-on replacing.
- Can small manufacturers adopt Industry 5.0?
More than ever. Affordable cobots like RO1, low-code systems, and modular tools mean you don’t need a Tesla-sized budget to get started. Start small, scale fast.
- How can I start using Standard Bots’ RO1?
Book a trial, drop it into your existing line, and test real applications (you don’t need major upgrades, typically). RO1 is ready to go with CNC, dispensing, assembly, and more.
Summing up
Industry 5.0 blends human creativity with intelligent machines to make manufacturing more adaptable, personalized, and efficient. 5.0 shifts from full automation to meaningful collaboration, putting people at the heart of the process.
Industry 5.0 isn’t a concept for later, it’s already starting to influence how factories are run.
The core principles behind the 5th Industrial Revolution aren’t to push people out. This revolution is about giving humans smarter tools, safer environments, and actual creative input again. Industry 5.0 promotes resilient, sustainable, and flexible systems that elevate both productivity and job satisfaction.
Next steps with Standard Bots
RO1 by Standard Bots is the six-axis Industry 5.0-ready cobot upgrade you need to future-proof your shop floor.
- Affordable and adaptable: Best-in-class automation at half the price of competitors; leasing starts at just $5/hour.
- Precision and strength: Repeatability of ±0.025 mm and an 18 kg payload make it ideal for CNC, assembly, and material handling, and a lot more.
- AI-driven and user-friendly: No-code framework means anyone can program RO1 — no engineers, no complicated setups. And its AI on par with GPT-4 means it keeps learning on the job.
- Safety-minded design: Machine vision and collision detection let RO1 work side by side with human operators.
Schedule your risk-free, 30-day onsite trial today and see how RO1 can bring AI-powered greatness to your shop floor.
Join thousands of creators
receiving our weekly articles.