Painting robots apply coatings faster, more precisely, and with less waste than manual methods, transforming industries from automotive to construction.
In 2024, the global painting robot market stood at $3.1 billion and is expected to grow to $5.8 billion by 2029, a CAGR of 13.1%, driven by surging demand for precision and efficiency in coating applications. Whether painting cars, walls, or murals, these systems deliver smoother finishes, lower overspray, and safer worksites.
Types of painting robots: TL;DR
What is a painting robot?
A painting robot (spray or coating robot) is an automated system with a robotic arm designed to apply paint, coatings, or other finishes to various surfaces. These robots are used in diverse industries like automotive, aerospace, and manufacturing to achieve consistent and precise application of coatings.
Unlike semi-automatic sprayers or handheld tools, robotic painting systems follow precise, pre-defined paths. They control flow rate, angle, distance, and speed, which are optimized for uniform coverage and minimal waste. This results in fewer touch-ups, less overspray, and faster cycle times, especially in high-volume environments.
Painting robots are a key part of broader painting automation, especially in industries where finish quality and repeatability directly affect the final product, like automotive manufacturing, aerospace, and metal fabrication.
Types of painting robots in 2025
1. Industrial robotic spray painting systems
Industrial robotic spray painting systems are the most widely used in industries like automotive paint shops, aerospace plants, appliance manufacturing, and metal fabrication lines. These robots are typically mounted with arms with 6 or 7 axes of movement, designed to follow complex 3D paths across curved surfaces like car bodies or aircraft parts.
The robot arm is paired with an advanced spray system, which is often electrostatic or high-volume low-pressure (HVLP) to apply paint evenly while reducing overspray. Vision systems or pre-loaded CAD data help define spray paths, and operators can adjust parameters like flow rate or angle to match different coatings or substrates.
Typical features include:
- Integrated process cables, air lines, and paint hoses
- Atomizers or rotary bell sprayers for ultra-fine coating
- Multi-axis arms with high repeatability (±0.1 mm or better)
- Compatibility with solvent-based, water-based, or powder coatings
A good example is the FANUC P-250iB, built for automotive applications, or the ABB IRB 5500, optimized for high-speed car body painting. These robots can paint a car in under 2 minutes, with near-zero human intervention.
Pricing: A fully integrated industrial painting robot system can cost between $50,000 to $200,000+, depending on configuration. This includes the robot, atomizer, booth setup, and safety equipment. While the upfront cost is high, ROI often arrives within 12 to 18 months thanks to faster throughput and reduced material waste.
2. Wall-painting robots
Wall-painting robots are built to handle large, vertical surfaces like warehouses, airports, construction sites, and infrastructure projects. These are mobile, lightweight, and designed to paint high walls and wide spans without ladders or scaffolding.
These robots typically roll on wheels, tracks, or use suction-based climbing mechanisms. Many come equipped with gyroscopic stabilization, edge-detection sensors, and mobile apps that let you upload designs or room dimensions for fully automated coverage. They can apply both solid-color coats and precision graphics.
One well-known example is the MYRO wall painting robot, which uses smart sensors to follow walls and apply paint accurately using a built-in roller or spray nozzle. It supports both manual guidance and autonomous painting once calibrated.
What makes wall-painting robots useful:
- Reduces worker fatigue and fall risk
- Speeds up repetitive, large-surface jobs
- No need for scaffolding in high-ceiling environments
- Compatible with latex, emulsion, or water-based paints
However, these robots still have limitations. Most struggle with highly textured walls or very uneven surfaces, and they may require some prep work or masking by humans beforehand.
3. House painting robots
House painting robots are designed for small-scale, residential use, both inside and outside the home. They’re typically smaller than their industrial or construction-grade counterparts, with an emphasis on ease of setup, portability, and safe operation around humans.
These systems can include track-based rollers, mobile sprayers, or even handheld robotic attachments that maintain consistent speed and pressure. Some newer models combine vision sensors with basic AI to detect wall edges, windows, or outlet plates, reducing the need for masking and supervision.
Examples of house painting robots:
- OKIBO (recent release): Intended for indoor use, this robot autonomously navigates and paints drywall surfaces.
- DIY robot painter kits: Some consumer-grade devices offer automated spraying or roller coverage for interior repainting.
Why homeowners and contractors are exploring these:
- Minimizes paint drips and roller streaks
- Reduces painter fatigue on ceilings or repetitive coats
- Can be operated by a single user with minimal training
- Speeds up single-room repaints without hiring a full crew
Having said that, house painting robots are still in their early stages. They’re not yet replacements for professional painters, especially when it comes to detail work, trim, or textured finishes. Many still require some level of human guidance or pre-planning.
4. Art and mural painting robots
Art and mural painting robots are designed to automate large-scale artwork, signage, and custom wall designs. These systems combine robotic movement with digital art files to reproduce detailed images on walls, billboards, and even curved surfaces.
These robots typically use stepper motors or track systems to move horizontally and vertically while spraying or dabbing paint in controlled patterns. The artwork is uploaded via software, often in vector or raster format, and the robot breaks it down into precise motion commands.
Popular use cases include:
- Branded office wall designs and retail signage
- Event graphics or pop-up venue customization
- Public art installations and government mural commissions
- School or stadium murals are applied quickly without scaffolding
One example is Scribit, a wall-drawing robot designed for homes and interiors. Though more of a plotter than a sprayer, it shows how robotic artists can translate digital art into wall-scale visuals. On the industrial side, companies like Robot Muralist use larger systems to complete multi-story murals in days, not weeks.
While these bots offer speed and reproducibility, they lack the improvisational flexibility of human artists. Custom color blending, brushwork nuance, or artistic interpretation still requires a manual touch.
5. Specialized coating robots
Specialized coating robots apply functional finishes such as corrosion protection, powder coating, or marine-grade coatings. They are used in industries where surface durability and performance are as important as appearance, including pipelines, shipyards, aerospace, and furniture production.
You’ll find them in:
- Pipeline and tank maintenance crews
- Shipyards applying anti-corrosion coatings
- Aerospace hangars using flame-retardant coatings
- Furniture and appliance lines using powder coating booths
These robots often work inside enclosed, high-safety environments and are integrated into automated paint systems with conveyors, curing ovens, and electrostatic applicators. They may feature explosion-proof designs, closed-loop feedback systems, or dual-mode heads for spraying and sanding.
In powder coating lines, a robot may electrostatically charge fine powder particles and apply them evenly to grounded parts, followed by curing in high-temperature ovens. Compared to manual coating, this method improves material adhesion and finish durability.
Key benefits:
- Reduced exposure to hazardous materials
- Uniform coat thickness for functional finishes
- Greater control over drying and curing stages
- Compatibility with automated QA and inspection tools
Pricing varies widely based on the application. A basic robot for powder coating may start at $60,000, while those handling marine or chemical-resistant coatings can exceed $200,000, depending on payload and safety ratings.
Benefits of automated painting systems
The benefits of automated painting systems include higher coating quality, faster production, improved worker safety, and reduced paint waste. Whether you’re painting car panels, drywall, or powder-coated parts, robotic systems deliver results that manual methods can’t match.
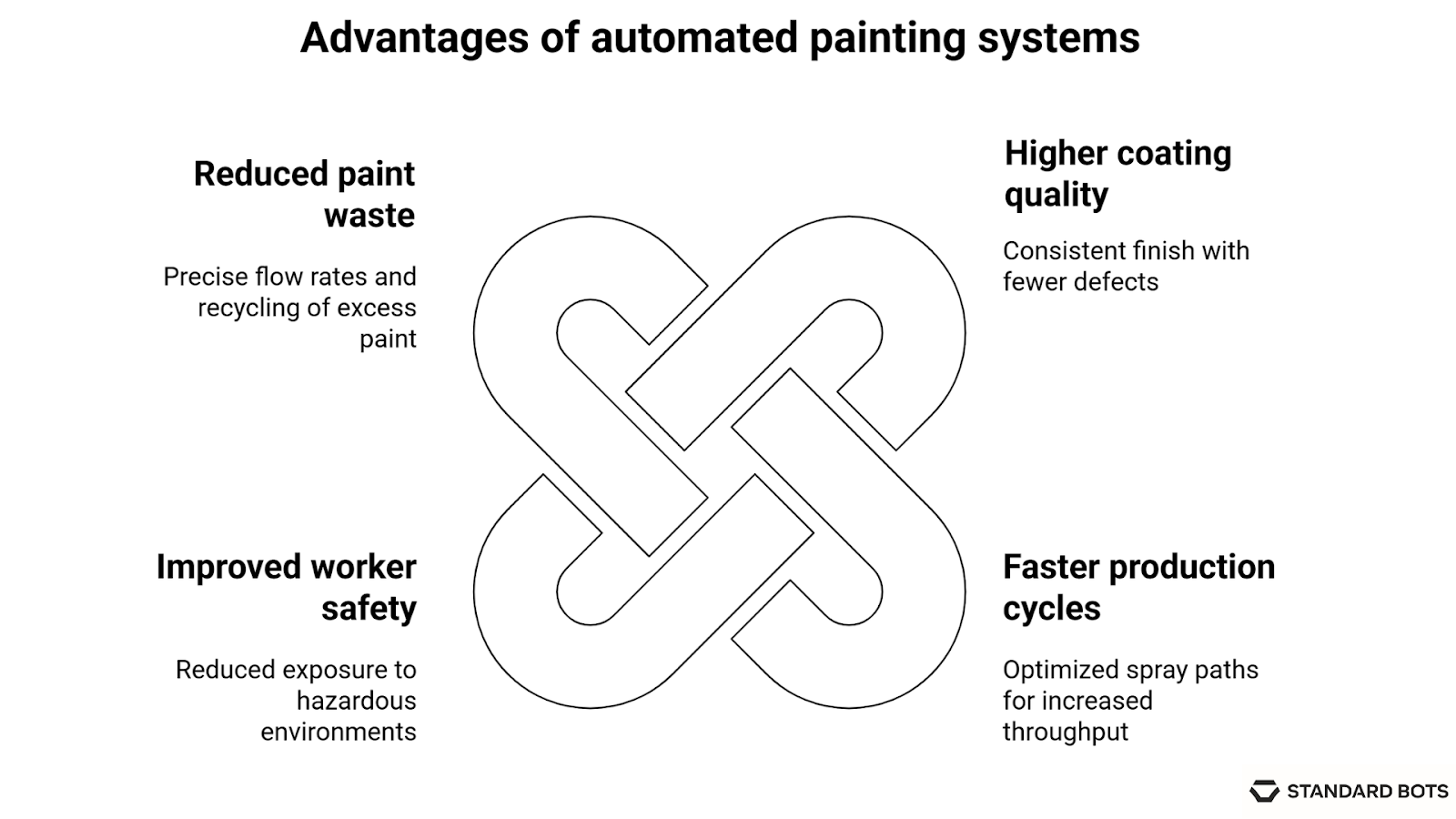
- Consistent finish, fewer defects: Robots follow the same path every time. No missed spots, uneven coats, or streaking. This reduces rework and ensures a higher first-pass yield, especially in high-spec industries like automotive or aerospace.
- Faster production cycles: With optimized spray paths and no breaks between shifts, painting robots boost throughput. One robot can replace multiple manual painters, running continuously during multi-shift operations.
- Safer working conditions: Manual painting exposes workers to paint fumes, flammable solvents, and confined spaces. Robots limit human exposure to hazardous environments, reducing the risk of respiratory issues and accidents.
- Lower paint waste and better cost control: Precise flow rates and optimized spray angles cut overspray. Many robotic paint systems recover or recycle excess paint, saving money over time, especially in facilities with frequent color changes.
Key factors to consider when choosing a painting robot
Choosing the right painting robot comes down to matching its capabilities to your production needs. Consider the weight and reach it must handle, the coating types it will apply, how easily it integrates into your workflow, and the availability of support and spare parts to keep it running with minimal downtime.
- Payload, reach, and axis configuration: Start with the basics: How heavy is your spray head? How far does the robot need to reach? For large objects or tall surfaces, look for robots with 6+ axes and extended horizontal reach. Small parts or tight spaces? Compact arms or tracked mobile units may be more efficient.
- Coating compatibility: Not all robots handle every type of paint or finish. Some are optimized for liquid coatings (like automotive basecoats), while others handle dry powder, gel coatings, or even specialty chemicals. Make sure your robot supports the paint flow, pressure, and application method you need.
- Programming and integration: Can your team operate it? Some painting robots support no-code interfaces or teach pendants, while others require full CAD integration. If you’re adding it to an existing production line, check compatibility with conveyors, PLCs, or MES systems.
- Maintenance and spare parts: Downtime kills ROI. Choose a robot with accessible service plans, local support, and spare parts that can be delivered quickly. Look for models with built-in diagnostics or predictive maintenance tools.
Final thoughts: trends in painting automation
Painting robots have evolved into essential tools for high-volume manufacturing and large-scale projects alike, delivering consistent finishes, reduced waste, and safer working conditions. The right choice depends on your coating type, part size, and integration needs, but in every case, automation offers measurable gains in quality and efficiency.
Looking ahead, several key trends are shaping painting automation in 2025 and beyond:
- AI-powered defect detection: Vision systems adjust spray patterns in real time to correct runs, gaps, or uneven coverage.
- Lightweight, mobile painting bots: Portable units for high-rise interiors, warehouse walls, and hard-to-reach ceilings without scaffolding.
- Flexible programming for mixed-batch jobs: No-code and easy reprogramming make high-mix, low-volume production viable for automation.
- Eco-conscious spray technologies: Low-VOC coatings and closed-loop recovery systems to meet stricter environmental standards.
Next steps with Standard Bots’ robotic solutions
Looking to automate your painting process? Standard Bots’ RO1 is the perfect six-axis cobot addition to any paint shop, delivering unbeatable precision and flexibility.
- Affordable and adaptable: RO1 costs $37K (list price). Get high-precision automation at half the cost of traditional robots.
- Precision and power: With a repeatability of ±0.025 mm and an 18 kg payload, RO1 handles even the most demanding spray-painting jobs.
- AI-driven simplicity: Equipped with AI capabilities on par with GPT-4, RO1 integrates smoothly with automated painting systems for advanced control.
- Safety-first design: Machine vision and collision detection mean RO1 works safely alongside human operators in spray booths.
Schedule your on-site demo with our engineers today and see how RO1 can bring AI-powered precision to your painting line.
FAQs
1. What industries benefit most from painting robots?
The industries that benefit most from painting robots are automotive manufacturing, aerospace, furniture production, appliance assembly, and commercial construction.
In these sectors, consistent finish quality, reduced paint waste, and faster production cycles directly impact profitability. Robots can handle large-scale, repetitive coating tasks without fatigue, ensuring high first-pass yields while minimizing labor and safety risks.
2. How much does a painting robot cost in 2025?
A painting robot in 2025 typically costs between $70,000 and $200,000 for an industrial setup, including the robot, spray system, and safety equipment. Smaller wall-painting or residential models range from $5,000 to $50,000. Final pricing depends on factors like reach, payload, coating type compatibility, and integration needs within your existing production line or facility.
3. Can painting robots work on textured or irregular surfaces?
Yes, painting robots can work on textured or irregular surfaces if equipped with vision systems, force sensors, or adaptive spray heads. These tools adjust nozzle distance, angle, and flow rate in real time. However, extremely rough or porous materials may still require human pre-treatment or touch-ups, especially for consumer-grade or smaller wall-painting robot models.
4. Are wall-painting robots suitable for residential projects?
Yes, wall-painting robots are suitable for residential projects when working on smooth, flat walls with uniform textures. They can speed up single-color repainting, ceilings, or large rooms, reducing manual effort. However, they may need human oversight for edges, trims, or textured finishes. Some units also require pre-masking around doors, windows, and outlets to maintain precision.
5. How do robotic spray systems maintain a consistent finish?
Robotic spray systems maintain a consistent finish by following pre-programmed paths at fixed speeds, angles, and spray distances. These settings remove human variability, ensuring uniform paint thickness. Many systems also use closed-loop flow control, atomizer adjustments, and vision-based defect detection to adapt to surface changes, delivering an even, high-quality coat across complex shapes.
6. Can existing spray booths be automated with painting robots?
Yes, existing spray booths can be automated with painting robots if they meet space, ventilation, and safety compliance requirements. The upgrade usually involves installing a robotic arm, integrating spray controls, and ensuring compatible airflow for paint curing and overspray capture. Many modern robots can adapt to older booths with minimal structural modifications or downtime.
7. What safety measures are needed when operating painting robots?
Safety measures for operating painting robots include proper fume extraction, explosion-proof enclosures for flammable coatings, and collision detection systems. Emergency stop buttons, motion limiters, and light curtains help prevent accidents. Operators should be trained in safe robot interaction and wear appropriate PPE to guard against paint mist, chemical exposure, and unexpected robot movement.
Join thousands of creators
receiving our weekly articles.