A dead man’s switch can shut down a machine, stop a train, or trigger an emergency signal without anyone touching it. It’s found in factories, vehicles, and even your inbox, and it’s one of the simplest yet most critical safety tools in automation.
We discuss how a dead man’s switch knows when something’s wrong. And, we’ll review why it’s still required in 2025, when AI and sensors are everywhere.
What is a dead man’s switch?
A dead man's switch is a safety mechanism, either mechanical or electronic, that is designed to activate when a human operator becomes incapacitated or unresponsive. It is typically used to prevent accidents or trigger an alert when the operator is no longer in control of a device or system.
There are different types depending on how and where they’re used. Mechanical versions use pedals, levers, or handles that must be continuously held down. Electronic and digital designs rely on sensors, timers, or software signals that detect user input or the lack of it.
You’ll find these in industrial robots, trains, cobots, CNC machines, and even in software platforms where digital dead man switches send alerts or execute pre-set actions if there’s no check-in.
Modern versions come in all formats:
- Trigger switches are used in power tools like angle grinders.
- Software-based switches that protect data or send alerts during downtime.
- Push buttons on forklifts, cranes, or robotic arms like those used in die casting.
- Foot pedals in collaborative robot arms are used for pick-and-place or automotive tasks.
In short, a dead man's device is a principle. If the human lets go, the system takes over to keep things safe.
How does a dead man’s switch work?
Digital dead man’s switches can be integrated into both physical and virtual systems, activating safety measures, securing data, and maintaining operational reliability when no user activity is detected.
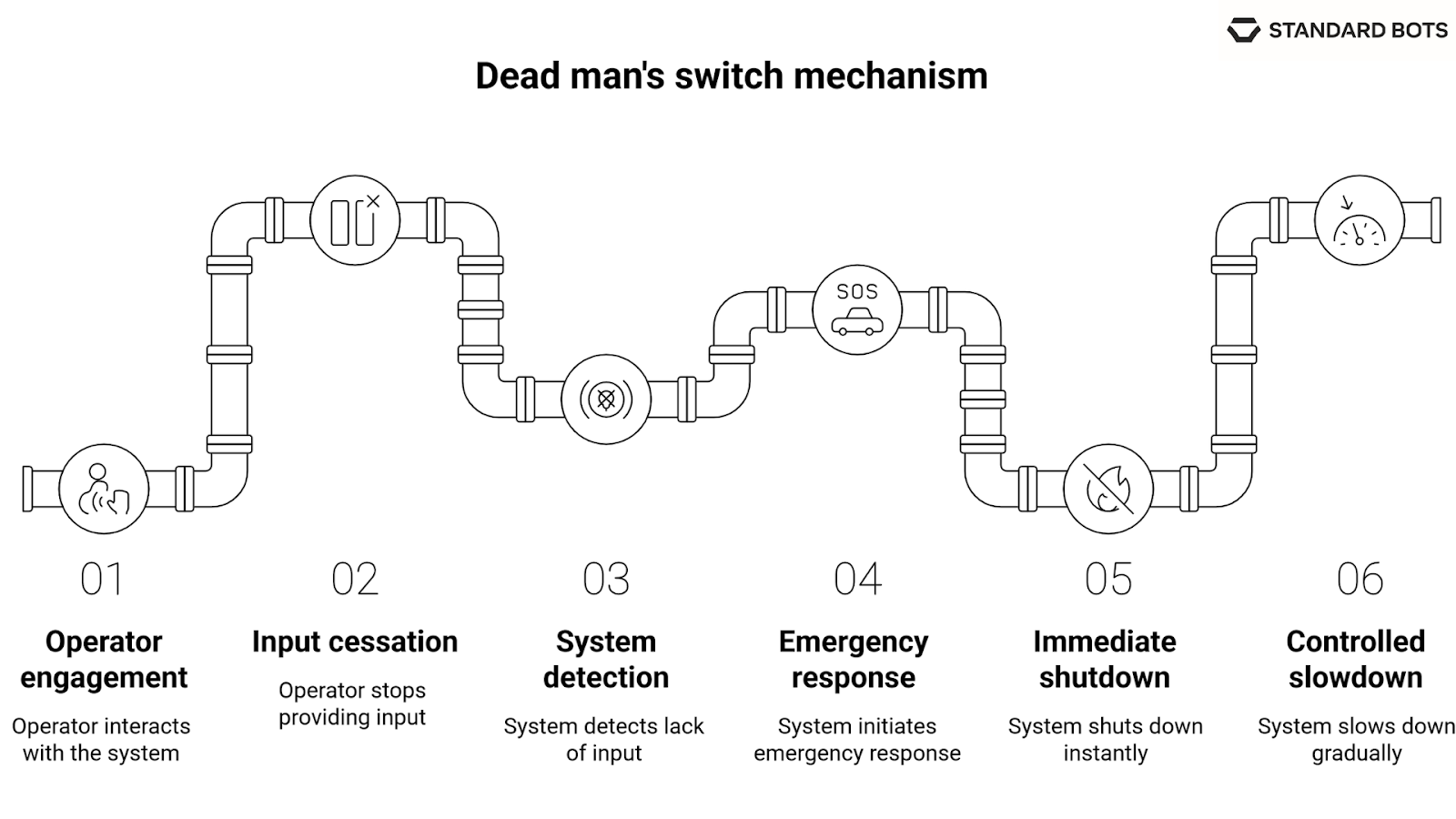
A dead man’s switch works on a fail-safe principle: if the operator stops providing input, the system assumes something’s wrong and reacts immediately to prevent damage or injury.
In mechanical systems, the mechanism usually relies on constant pressure or contact:
- On an industrial grinder, releasing the trigger disengages the motor instantly.
- A train driver must keep pressing a handle or foot pedal. If they let go, the system cuts power and applies the brakes.
In modern automated setups, sensor-based and digital systems monitor operator engagement.
These might include:
- Pressure sensors in seats or grips
- Motion or eye-tracking in vehicle control systems
- Timed software checks (like a scheduled “check-in”) that, if missed, activate an emergency response
Depending on the risk level, the response can be:
- Immediate shutdown: Used in power tools or industrial robots where even a second of delay could cause injury.
- Controlled slowdown: More common in transport or heavy machinery to avoid sudden mechanical stress.
In collaborative automation such as pick-and-place systems, the dead man switch often works alongside safety-rated sensors and soft stops to ensure human workers can safely intervene at any time.
Common uses of a dead man’s switch in 2025
1. Trains and locomotives
Trains and locomotives use dead man’s switches to automatically apply brakes if the driver releases a control pedal or lever. If they faint, fall asleep, or let go, the system assumes a problem and triggers braking. Most modern locomotives include dead man pedals or vigilance systems that escalate to emergency stop if the operator doesn’t respond in time.
2. Industrial tools
Power tools like grinders, drills, and saws often include trigger-type dead man switches. They stop running the moment the operator releases the button. These switches are not optional. In many jurisdictions, they’re legally required in industrial-grade tools.
3. Heavy machinery and robots
Forklifts, cranes, and robotic systems all use versions of dead man controls. In collaborative robots, like those used in automotive plants, the operator may hold a pressure-sensitive button while manually guiding the robot, releasing it instantly halts motion.
Cobot arms used in factory automation or die casting often integrate both dead man buttons and collision detection, offering layered safety.
4. Software and digital automation
Not all dead man switches are physical. In software systems, a digital dead man’s switch may be programmed to send an email, upload files, or shut down access if no user input is detected over a set period.
These are common in personal security tools, data backups, and even server management, ensuring action happens even if the user can’t intervene.
You’ll see this in industrial automation, where a robot may stop if the operator doesn’t log in or confirm readiness within a timeframe.
Dead man’s switch vs. kill switch
A dead man’s switch differs from a kill switch in that it activates automatically when the operator is inactive, whereas a kill switch is pressed manually in an emergency.
Industrial safety standards for the dead man’s switch
Dead man’s switch safety standards are set by organizations like OSHA, ISO, and IEC to ensure fail-safe operation in industrial settings.
- In the U.S., OSHA mandates automatic shutoff controls for machines like forklifts and power tools. If the operator can’t act, the system must stop, which is where a dead man's device comes in.
- Globally, ISO 13849-1 and IEC 60204-1 set standards for how these systems must behave: fail-safe activation, redundant design, and immediate interruption of hazardous motion.
- In Europe, EN 60947-5-5 outlines performance requirements for control switches, including dead man components used in robots and machinery.
Cobots used in factory automation must include safety-rated inputs like dead man buttons when humans are nearby. Robot makers like ABB and KUKA build these into their control interfaces, meeting international safety norms.
Digital dead man’s switches
A dead man’s switch operates in a sequence that detects the loss of operator input, triggers an emergency response, and safely stops or slows down machinery to prevent accidents.
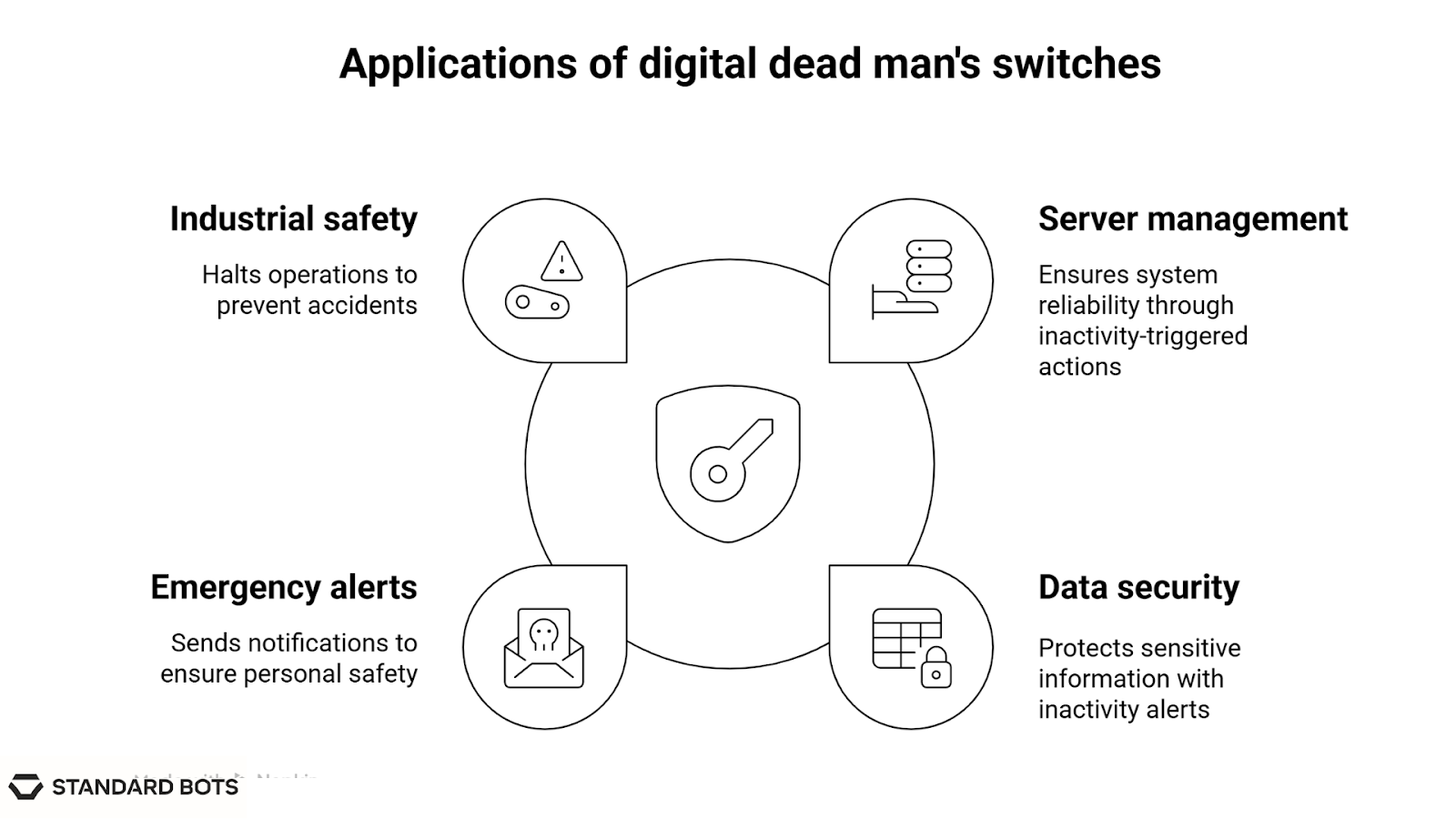
These are often used in:
- Server management, where inactivity can trigger shutdown or failover procedures.
- Data security, where the system sends an alert or releases encrypted information if no check-in is received.
- Emergency alerts, like sending automated emails or location pings if someone doesn’t confirm safety.
For example, a dead man’s switch email might be configured to send sensitive instructions to a lawyer or colleague if no login or activity is detected for 72 hours. This kind of dead man’s switch software is popular among journalists, whistleblowers, or individuals storing critical access credentials.
In industrial settings, digital dead man switches can halt operations if the operator doesn’t interact with the machine’s interface or confirm readiness, offering another layer of passive safety.
These systems don’t replace physical dead man buttons. They extend the same principle into digital workflows, where operator presence must be verified without physical contact.
Retrofitting a dead man’s switch
Retrofitting a dead man’s switch involves adding mechanical, sensor-based, or software systems to older equipment to improve safety.
For mechanical systems like grinders or forklifts, retrofitting typically involves:
- Adding spring-loaded foot pedals or grip handles
- Integrating cutoff relays tied to hand-operated controls
- Replacing standard switches with pressure-sensitive triggers
For robot arms and industrial machines, it might mean installing an external dead man push button or integrating safety relays with the controller. In many cases, the add-on connects directly to the emergency stop circuit, making it an affordable upgrade without a full redesign.
Software-based systems can also be added with minimal cost. For example, adding a dead man switch to a robot interface might involve timeout-based scripts or login confirmation prompts. Some digital platforms even offer ready-to-deploy dead man’s switch software for email, cloud backups, or secure access control.
When weighing the cost, compare it to the machine’s total value. If you’re upgrading a $20,000+ robot arm, retrofitting a $200 safety switch is often a no-brainer, especially if it helps meet current standards.
Routine maintenance
Dead man’s switch maintenance includes regular inspections, cleaning, and testing to ensure the system responds instantly when needed.
For mechanical switches (like pedals or trigger grips), routine checks should include:
- Cleaning dust or debris from moving parts
- Inspecting springs for tension loss or corrosion
- Verifying that the release immediately cuts power
For sensor-based or digital switches, maintenance includes:
- Recalibrating thresholds if the response feels delayed
- Testing sensor response times and signal transmission
- Reviewing logs or system alerts to catch skipped activations
Wiring, insulation, and connectors should be checked quarterly, especially in high-vibration environments or where the switch is frequently used.
Some setups also require logged tests, where operators simulate release events to verify correct shutdown. This is often part of routine compliance for collaborative robots or machines with human-in-the-loop systems.
Whether it’s a foot pedal on a die-casting robot or a dead man button in a cobot teaching interface, scheduled maintenance keeps it functional and keeps your safety guarantees intact.
Final safety tips for homemade or DIY dead man’s switches
Homemade dead man’s switches must be built with rated components, proper wiring, and thorough testing to ensure reliability in real-world use.
If you’re building your own dead man’s switch, keep these safety rules in mind:
- Don’t bypass factory safety features: Disabling interlocks or modifying existing wiring can create hazards and void equipment warranties.
- Use only tested components: Stick to industrial-grade push buttons, spring-loaded triggers, or momentary switches rated for your voltage and load.
- Insulate and ground everything properly: Faulty wiring can lead to shock, short circuits, or equipment failure.
- Know the load limits: Make sure your switch can safely interrupt the current without overheating or wearing out prematurely.
- Test under real-world conditions: Don’t assume it works. Verify that motors stop, power cuts, or alerts trigger exactly as expected.
- Avoid cutting corners on reliability: Safety systems must work the first time, every time.
Next steps with Standard Bots’ robotic solutions
Looking to make your automation safer? Standard Bots’ RO1 is the perfect six-axis cobot addition to any production line, delivering unbeatable precision and built-in safety features, including support for dead man controls during manual operations.
- Affordable and adaptable: RO1 costs $37K (list price). Get high-precision automation at half the cost of traditional robots.
- Precision and power: With a repeatability of ±0.025 mm and an 18 kg payload, RO1 tackles demanding industrial jobs with ease.
- AI-driven simplicity: Equipped with AI capabilities on par with GPT-4, RO1 integrates smoothly into workflows for advanced, responsive automation.
- Safety-first design: Machine vision, collision detection, and dead man control compatibility make RO1 safe to operate alongside human teams.
Schedule your on-site demo with our engineers today and see how RO1 can bring safe, AI-powered automation to your shop floor.
FAQs
1. What legal standards govern the use of dead man’s switches in industrial environments?
The legal standards that govern the use of dead man’s switches include OSHA in the U.S., ISO 13849-1, IEC 60204-1, and EN 60947-5-5. These standards define when a switch is required and how it must behave in industrial control systems.
2. Can existing power tools be retrofitted with a dead man’s switch, and how?
Yes, existing power tools can be retrofitted with a dead man's switch. The most common methods include replacing the standard trigger with a spring-loaded dead man's trigger or installing an external shutoff device. When retrofitting, always ensure the replacement switch and wiring are rated for the tool's voltage and current load to maintain safety and functionality.
3. How does a digital dead man’s switch send automatic email alerts if I’m incapacitated?
A digital dead man’s switch sends automatic email alerts by monitoring user activity through a countdown timer system. When you don't provide the required input (like a password or check-in) within the preset time window, the software automatically triggers the programmed alert or action, such as sending emergency emails to designated contacts.
4. What routine maintenance should be performed on a dead man’s switch to ensure reliability?
Routine maintenance for a dead man’s switch includes checking spring tension for proper resistance, cleaning mechanical parts to prevent debris buildup, testing sensor response times, and reviewing software logs if applicable. This maintenance schedule ensures the switch will activate correctly when the operator becomes inactive and prevents false triggers during normal operation.
5. Is a dead man’s trigger the same as a kill switch, or are there functional differences?
No, a dead man's trigger is not the same as a kill switch, and there are important functional differences. A dead man's switch activates automatically when the operator becomes inactive or releases pressure, whereas a kill switch requires manual activation by pressing a button during an emergency. Dead man's switches provide passive safety, whereas kill switches require deliberate action.
6. Are dead man’s switches mandatory on trains and locomotives, and how do they work in that context?
Yes, dead man's switches are mandatory on most trains and locomotives worldwide. The operator must maintain continuous pressure on a pedal or hold a control handle. If this pressure is released for more than a few seconds, the system automatically applies the emergency brakes to bring the train to a safe stop. This prevents runaway trains if the operator becomes incapacitated.
7. What safety precautions should I follow when building a homemade dead man’s switch?
When building a homemade dead man’s switch, use properly rated electrical components that match your system's specifications, never bypass existing factory safety features, and conduct thorough testing under realistic conditions. Additionally, consult relevant electrical codes and consider having the system inspected by a qualified electrician to ensure it meets safety standards and will function reliably when needed.
Join thousands of creators
receiving our weekly articles.