A pick and place robot moves objects from one place to another. They can grab anything from microchips off a tray or toss candy bars into boxes. These bots are 100% about speed, precision, and not needing wrist surgery after a 12-hour shift.
And no, they’re not just for massive factories anymore, we’ll show you how pick and place automation is flexing its way into every corner of manufacturing.
In this article, we’ll cover:
- What pick and place robots are and how they work
- Top applications and types of pick and place robots
- Benefits and adoption considerations
- How Standard Bots powers pick and place cobot automation
What is a pick and place robot?
A pick and place robot is exactly what it sounds like — a robot that grabs stuff and puts it somewhere else.
The goal? Speed, accuracy, and no dropped products. From microchips to muffins, these bots specialize in moving things fast and doing it the same way every single time.
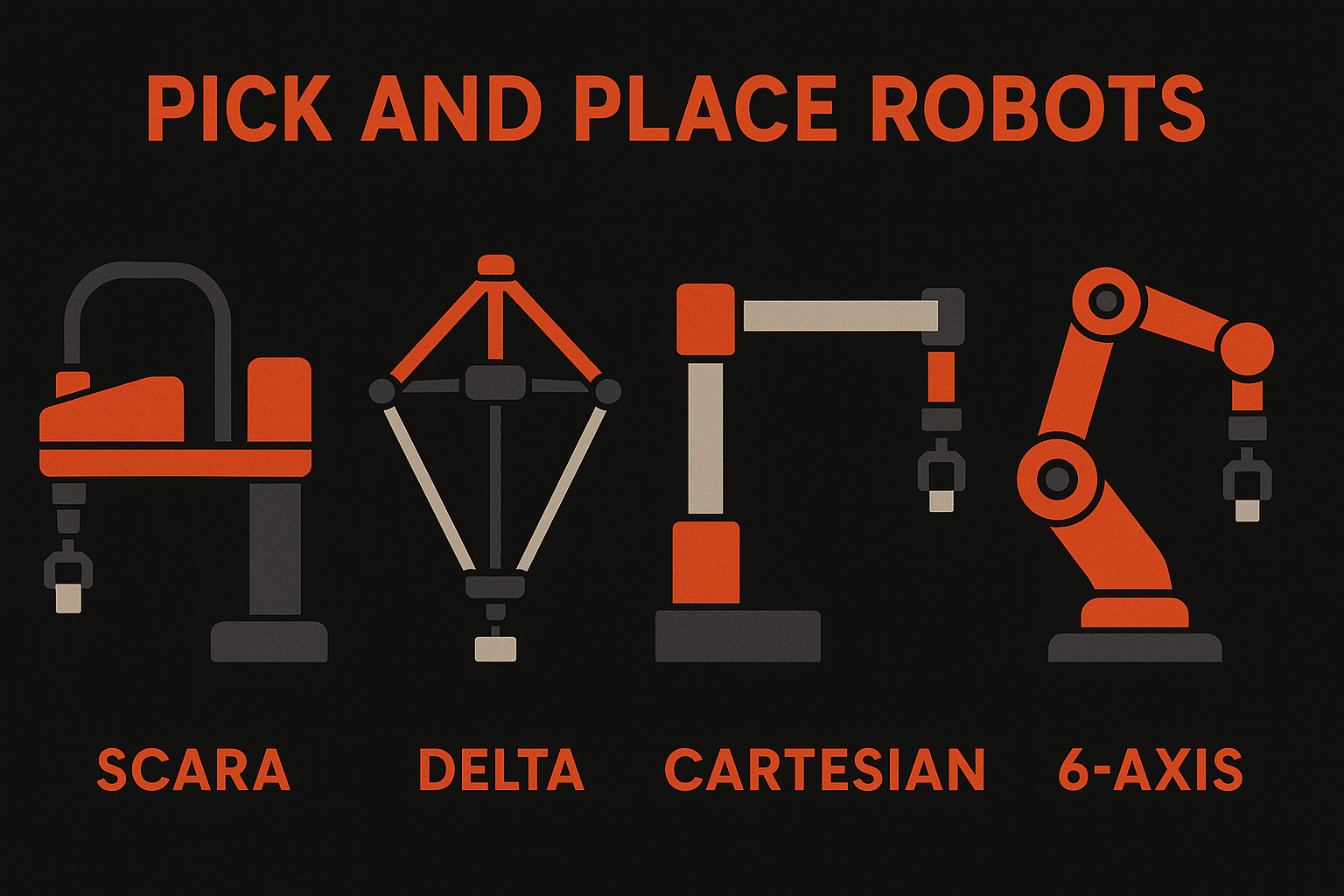
The tech stack behind the grab-and-go:
If you're curious about how these robots reach the kind of speeds that would make a human’s rotator cuff disintegrate, our high-speed breakdown has everything you need.
How pick and place robots work
Think of a pick and place robot like a speedrunner with a suction cup — it’s not winging it, it’s optimizing everything. Every grab, every drop, every conveyor sync is precision-timed, AI-adjusted, and faster than Dave in QA can even blink.
What’s happening behind that grab-and-go bonanza:
- Vision with main character energy: Cameras or 3D sensors spot the object, ID the position, and feed it straight to the robot’s control loop — almost no operator babysitting is necessary. But yes, humans are still in the loop.
- Movement so smooth it could host a jazz podcast: Once it knows what it’s picking, the robot calculates the most efficient path, dodging belts, corners, and other bots like it’s playing 4D Tetris. Doesn’t mean it won’t occasionally mess up, but it stumbles way less than humans.
- Conveyor tracking = live-action aim assist: The product’s moving? So is the bot. These systems track conveyor speed and adjust trajectories mid-swoop, like an F1 pit crew with an even higher IQ.
- Repeatability that would make a sniper jealous: These bots aren’t eyeballing anything. They’re accurate to fractions of a millimeter, especially when paired with custom end-of-arm tooling (EOAT).
Use cases for pick and place robots
Pick and place robots are the factory equivalent of hyperactive, speedrunning gamers — no breaks, no missed frames, and they never ask for a raise.
These use cases prove why they’re dominating modern manufacturing floors:
- Snack packaging without chip carnage: Frito-Lay uses ultra-fast robotic palletizers to haul snacks around with zero crunch damage and half the floor space. This is where a high-speed pick-and-place robot thrives — relentless pace, featherlight handling, and made to work every shift.
- Pharma lines that never sneeze: Pfizer’s sterile injectables are packed using robotic systems inside ISO-5 clean rooms, where precision and sterility are non-negotiable. With EOAT setups designed for clean handling and exact placement, this kind of robotic packaging helps scale vaccines instead of contamination.
- Electronics assembly with scary accuracy: At Foxconn, robotic pick and place systems deal with everything from microchips to phone lenses, way faster than human hands. A typical industrial pick and place robot makes thousands of near-perfect placements per hour.
- E-commerce fulfillment that actually keeps up: Locus Robotics supplies mobile bots to huge e-comm brands like Skims, helping workers pick and sort SKUs at ridiculous speeds. Combined with robot grippers that can adapt to clothing, boxes, and weirdly shaped items, they’re pushing pick and place automation to warehouse-dominating levels.
Types of pick and place robots
Not all pick and place robots move the same way, some fly like caffeinated spiders, others glide like plotters from 1995. Choosing the right one depends on your layout, product, speed demands, and whether you’re stacking yogurt cups or microchips.
Here’s the cheat sheet (with links if you wanna go deep):
How Standard Bots powers pick and place cobot automation
Most pick and place robots either overpromise or underdeliver; they’re either locked into rigid motions or buried under a 12-step setup process. RO1 isn’t like that. It brings high-end performance to real-world lines, minus all the typical robo-drama.
Why RO1 actually fits into real factories (not just demos):
- Unflinching flex-a-thon: With its full six-axis motion, RO1 tackles awkward bin angles, tight corners, and high-mix assembly flows.
- AI figures it out fast: RO1 uses vision and motion planning to adapt on the fly, without human intervention. Conveyor tracking and object recognition are built-in, not bolted on.
- Precision holds up under pressure: Its ±0.025 mm repeatability makes it a top-tier option for robotic packing, circuit placement, or medical kitting. Just choose your gripper wisely.
- Costs less than your coffee habit: You can lease RO1 starting at $5/hour, and you don’t need to call in a systems integrator every time you move a table.
- It’s not theory, it’s shipping now: RO1 already works across multiple industrial pick and place robot deployments, from robotic packaging setups to e-comm sort lines.
Benefits of robotic pick and place systems
When matched to the right environment, pick and place robots bring consistency, safety, and scale in ways human teams physically can’t, even if they risk their joints.
Here’s what they bring to the table:
- Packing speed that doesn’t gas out: In high-volume lines like snack foods or cosmetics, consistent motion is everything. Pick and place systems maintain steady output — 60 to 120 cycles per minute — without lag or rework, even after 12-hour shifts. That’s the difference between a perfect pack and a crushed product avalanche.
- Accuracy where it actually matters: Whether it’s aligning circuit boards or handling delicate syringe kits, these robots hold sub-millimeter tolerances across thousands of movements. And they don’t lose focus after they’ve had a hefty lunch.
- Workplace injuries? Nope: Human arms weren’t designed to do the same reach-and-drop 9,000 times a day. In food and drink lines especially, this leads to chronic injuries. Robotic systems take over the brutal stuff — not the jobs, just the joint pain.
- Savings that stack quietly: Upfront costs used to be a blocker, now you can lease full systems by the hour. Factor in lower defect rates, fewer labor bottlenecks, and higher throughput, and the ROI isn’t theoretical, it’s week-over-week data.
- Stress-free scale-ups: Growth shouldn’t mean another round of onboarding. With well-configured cobots, you can duplicate cells, expand product lines, and add shifts without reshuffling your entire floor plan.
- Reliability to last: These aren’t demo toys. With proper maintenance, most pick and place units run for years with minimal intervention — no burnout, no turnover, no drama.
- Adaptability for even the biggest mess: These systems aren’t plug-and-pray anymore. With vision systems and better path planning, even low-volume, high-mix shops can integrate automation without going full sci-fi.
Considerations when choosing a pick and place robot
There’s no such thing as a one-size-fits-all robot. Your ideal setup depends on what you’re picking, how often you’re moving it, and how much room you’ve got to make it happen. Go too small and you bottleneck your output. Go too big, and you just bought a flex that doesn’t fit your floor.
What to keep in mind before pulling the trigger:
- Payload isn’t optional, it’s the whole game: If your product weighs 5 kg and your robot maxes out at 6, you’re already at risk. Always spec for worst-case weight (plus EOAT), not best-case marketing.
- Reach is more than just arm length: Don’t just measure the distance from A to B. Account for how your end-of-arm tooling will angle, rotate, and clear obstacles, or you’ll be retooling your whole cell three weeks in.
- Your product mix changes everything: Single SKU lines? Easy. But if you’re running a high-mix, low-volume setup with lots of variation, you’ll want a system that adapts quickly, preferably with built-in vision and flexible grippers.
- Software is where a lot of robots lose you: If the UI looks like it was built for 1998 NASA engineers, skip it. A clean, no-code interface cuts ramp time, operator errors, and “how do I even run this thing?” moments.
- Integration vs. “Wow, that’s easy”: Some robots require an entire army of systems integrators just to set up a basic pick and place loop. RO1 is plug-and-play ready — fast deployment, easy learning curve, and no $40K support invoice after install.
Where is pick and place robotics going next?
Pick and place tech ain’t coasting no more, it’s picking up speed. We’re talking smarter vision, smoother integration, and cobots that fit into real teams and real floors, not just showroom demos.
What the future of pick and place actually looks like:
- AI that adapts instead of crashing: Newer systems can handle object variation, bin chaos, and conveyor weirdness without throwing a digital tantrum. They learn from data, not from rules, so your robot can keep improving, even when your product mix changes weekly.
- Cobots that get along with humans (for real this time): The latest collaborative arms are safer, more reactive, and designed to work side by side with operators — no cages, no shutdown zones, yes, thank you.
- Machine vision that sees the full picture: Today’s systems identify orientation, categorize product types, and even detect flare-ups mid-motion. That’s huge for electronics, pharma, and anyone dealing with fragile or variable goods.
- Flexibility that doesn’t collapse under pressure: Modern lines don’t run one SKU at a time. From boutique packaging to custom device assembly, pick and place setups now need to pivot fast — and the best ones handle it without tanking throughput.
- Easier programming: Interfaces are finally catching up. You’ll see more drag-and-drop tools, visual workflows, and AI-assisted pathing, so operators don’t need to code or call in IT every time a conveyor shifts six inches.
FAQs
- Are pick and place robots expensive?
They can be, but they don’t have to be. Leasing models like RO1’s $5/hour setup make pick and place automation viable even for smaller shops.
- Can a pick and place robot do quality checks?
Not solo, but with the right vision system, they can flag misalignment, missing parts, or placement errors in real time.
- What kind of grippers work best for packaging?
It depends on your product. Vacuum grippers dominate in robotic packaging lines for lightweight or sealed goods, while adaptive fingers work better for weird shapes or fragile objects.
- What is the speed of a pick and place robot?
On average, anywhere from 60 to 120 cycles per minute (some models can handle 30, others can handle 200). The speed depends on the robot type, product weight, and how close the parts are spaced.
- How accurate are pick and place robots like RO1?
RO1 clocks in at ±0.025 mm repeatability, which is plenty for electronics, medical packaging, or anything that needs clean placement at scale.
- Can pick and place robots handle multiple SKUs?
Absolutely, as long as you’ve got dynamic programming, solid sensors, and a flexible gripper. Robotic pick and place setups are getting way better at high-mix handling.
- What makes Standard Bots’ RO1 different?
It’s the rare combo of powerful and practical: AI vision, six-axis reach, no-code UI, and pricing that doesn’t punch you in the wallet.
Summing up
Pick and place robots are lightning-fast, ultra-precise machines built to grab anything from microchips to cupcakes. And, they move with sniper-level accuracy, all while dodging conveyors like they’re playing 4D Tetris.
Powered by AI, vision systems, and custom grippers, pick and place robots are changing everything from snack packaging to pharma lines with relentless speed and zero burnout. Plus, they bring the kind of repeatability humans can only dream of.
When every product variation, packaging tweak, or shipping rush hits the floor, these systems stay dialed in. If your production line still breaks down every time volume spikes, it’s probably time to give the robots a real shot.
Next steps with Standard Bots
RO1 by Standard Bots is the six-axis cobot upgrade your factory needs to automate smarter.
- Affordable and adaptable: Best-in-class automation at half the price of competitors; leasing starts at just $5/hour.
- Precision and strength: Repeatability of ±0.025 mm and an 18 kg payload make it ideal for CNC, assembly, and material handling, and a lot more.
- AI-driven and user-friendly: No-code framework means anyone can program RO1 — no engineers, no complicated setups. And its AI on par with GPT-4 means it keeps learning on the job.
- Safety-minded design: Machine vision and collision detection let RO1 work side by side with human operators.
Book your risk-free, 30-day onsite trial today and see how RO1 can take your factory automation to the next level.
Join thousands of creators
receiving our weekly articles.