A cobot welding cell is an automated workspace that combines a collaborative robot with welding equipment to handle repetitive welding tasks safely alongside human workers.
These cells can increase welding productivity by 4x while addressing the 330,000 welder shortage hitting U.S. manufacturing.
Think of a cobot handling 200+ bracket welds daily while your skilled welder focuses on complex custom work. That's the reality for smart fabrication shops using these systems.
What is a cobot welding cell? The 30-second answer
A cobot welding cell is a self-contained automation system that uses a collaborative robot to perform welding operations. Cobot cells work safely next to human operators thanks to built-in sensors and force limiting, unlike traditional industrial welding robots that require safety cages.
Bottom line: These cells automate the boring, dangerous welding jobs, so your skilled welders can focus on complex work that actually needs human expertise.
Cobot welding cell: Key components
Every effective cobot welding cell includes these core elements:
- Collaborative robot arm: Six-axis arms with 15–25 kg payload capacity handle most welding applications
- Welding power source: MIG, TIG, or arc welding equipment integrated directly with the robot
- Safety sensors: Collision detection, area scanners, and emergency stops ensure safe human-robot collaboration
- Programming interface: No-code software lets operators set up new welding patterns without experience in robotic welding programming
- Fixturing system: Jigs and clamps hold parts in position for consistent weld quality
How does a cobot welding cell work?
Cobot welding cells follow a straightforward process that integrates hardware, software, and safety protocols for smooth human–robot collaboration. It's way simpler than traditional robotic welding setups and, well, it crushes productivity goals.
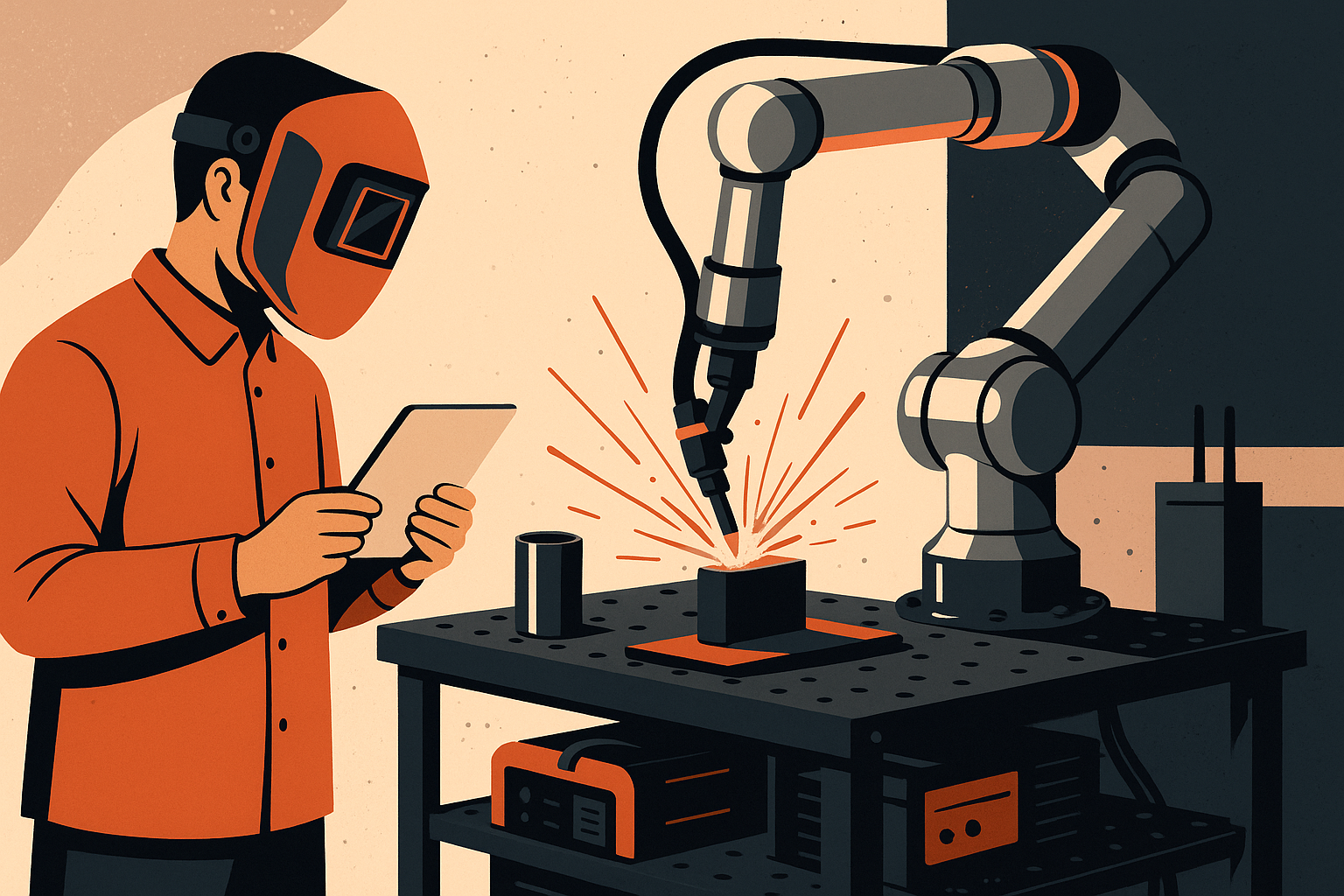
Cobot welding cell: Step-by-step breakdown
Step 1: Part loading
Operator places the workpiece in the fixture. These fixtures are often designed for consistent part positioning, but it depends on your cobot. Typically, the cobot system then runs automated calibration checks to nail tool center point accuracy.
Step 2: Pattern execution
Cobot follows the programmed weld path with precise speed and positioning. The cobot maintains optimal stick-out distance (e.g., 10–15 mm for MIG welding), while monitoring arc stability through integrated sensors.
Step 3: Quality monitoring
Built-in sensors track weld quality and detect issues in real-time. The cobot’s system does continuous quality checks and enables real-time weld assessment with automatic parameter adjustments.
Step 4: Safety oversight
Continuous monitoring stops the robot if humans enter the work area. Cobot welding cells use multiple safety systems, including collision detection, which uses force/torque sensors that detect contact with humans and stop motion within milliseconds.
Step 5: Part removal
Operator removes finished parts and loads the next batch. Automated cycle management optimizes throughput. In fact, with proper fixture design and dual-station setups, you can have continuous operation. One station loads while the other welds.
Real example: At a local fabrication shop, their RO1 cobot handles 200+ bracket welds per day. The operator loads parts, hits start, and the robot completes perfect welds in 45 seconds each. No programming knowledge required.
Cobot welding cell vs. traditional robotic welding: what's the difference?
Traditional robotic welding dominated for decades, but cobot cells are winning on flexibility and cost.
Winner: Cobot cells for most manufacturers. They're faster to deploy, easier to program, and don't eat up valuable floor space with safety barriers.
Cobot welding cell: Benefits and limitations
Pros
- Programming is very simple: I programmed a new weld pattern on the Standard Bots RO1 in under 20 minutes. No coding, no complex menus, just guide the arm and hit record.
- Flexibility beats everything: Switching between aluminum brackets and steel frames took 5 minutes. Try doing that with a traditional robot cell.
- Safety features actually work: The collision detection stopped instantly when I accidentally bumped the arm. No damage, no drama, just smart safety.
- ROI hits fast: Typical ROI for cobots ranges from 18 to 24 months, with many shops seeing payback even faster.
Cons
- Speed isn't everything: Traditional robots weld faster on high-volume runs. Cobots prioritize safety over raw speed.
- Payload limits matter: Most cobots max out around 25 kg. Heavy structural welding still needs traditional systems.
- Arc-on time trade-off: While cobots improve consistency, manual welders only achieve 10–20% arc-on time compared to cobot cells reaching 70%+.
Should you use a cobot welding cell? My take
Cobot welding cells make sense for 80% of fabrication shops, especially those struggling with the welder shortage or repetitive work that's burning out their skilled staff.
Cobot welding cells are perfect for
- Small to medium shops doing batch work with frequent changeovers
- Manufacturers with welder shortages who need to maximize existing talent
- Businesses welding similar parts repeatedly, like brackets, frames, or enclosures
- Operations that want 24/7 production without paying overtime rates
Skip cobot welding if you
- Need maximum speed on high-volume runs — traditional robots still win here
- Work primarily with exotic materials requiring specialized welding techniques
- Have unlimited skilled welders and no turnover issues (lucky you)
Alternative recommendation: Consider traditional robotic cells for pure speed, or hybrid setups combining both approaches.
How to set up a cobot welding cell in 5 steps
Step 1: Assess your space and power requirements. Most cells need 10×10 feet minimum and 220V power. You’ll need proper ventilation (6 to 10 air changes per hour with fume extraction).
Step 2: Choose your cobot and welding equipment. Match payload and reach to your largest parts.
Step 3: Design fixtures and tooling. Consistent part positioning is critical for weld quality. Set up safety zones and I/O configurations.
Step 4: Program initial weld patterns. Start with simple joints before tackling complex assemblies. (Check out our tutorial on how to train your robot.) Notably, RO1 comes with pre-programmed welding schedules for different materials.
Step 5: Train operators on safety protocols. Verify and test the safety systems, as even collaborative robots need proper safety procedures.
Pro tip: Start with your most repetitive welding job. Success there builds confidence for tackling more complex applications.
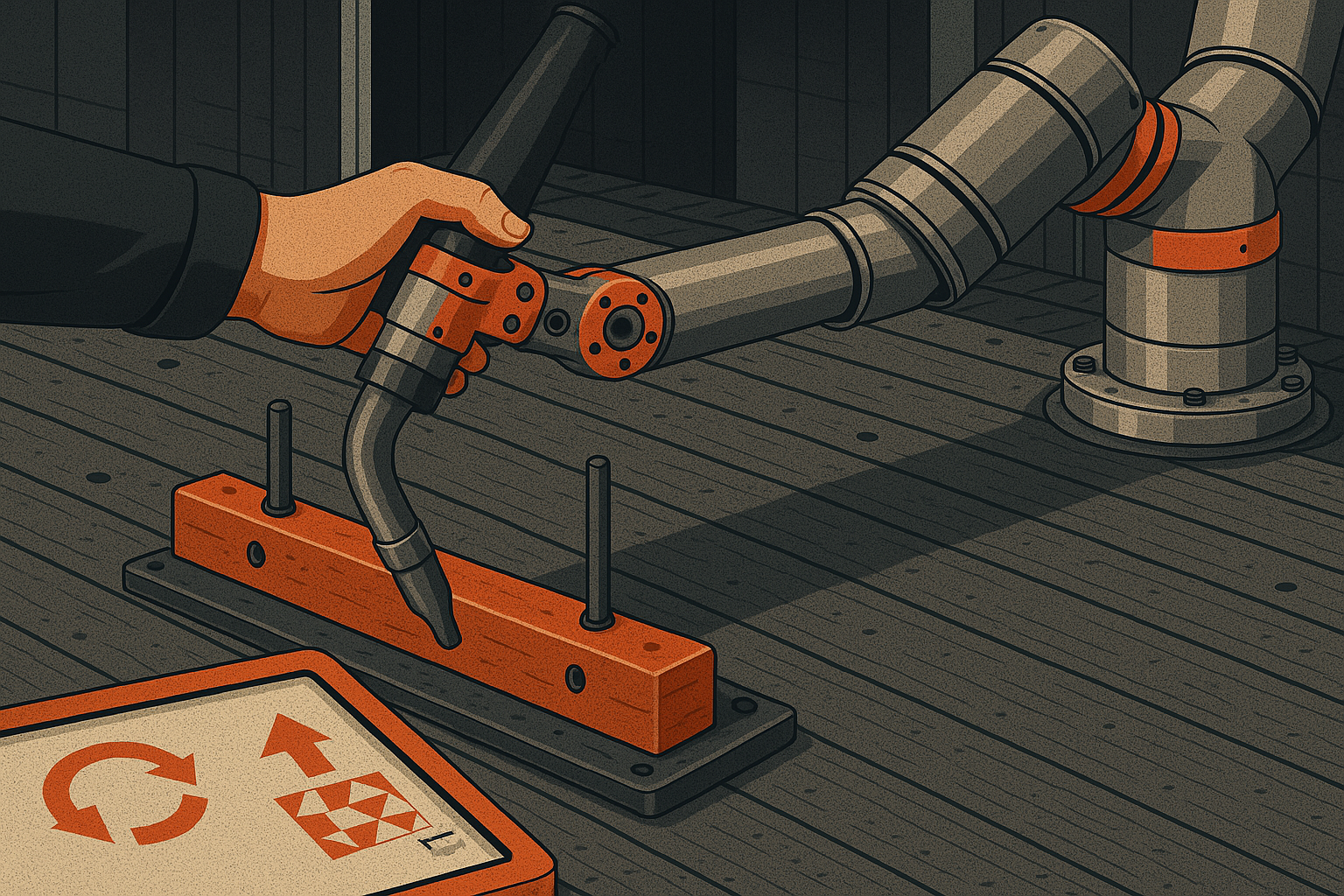
Cobot welding best practices I wish I’d known earlier
- Consistent part preparation: Clean, properly fitted joints make all the difference in weld quality
- Regular torch maintenance: Dirty contact tips and worn liners cause more failures than robot issues
- Proper fixture design: Rigid, repeatable positioning prevents weld defects and robot errors
- Preventive calibration: Monthly accuracy checks catch drift before it affects production
Common mistakes to avoid
- Skipping safety training: Collaborative doesn't mean careless; operators still need proper protocols
- Overloading the work envelope: Trying to weld parts at maximum reach reduces accuracy
- Ignoring environmental factors: Drafts, temperature changes, and vibration all affect weld quality
My verdict on cobot welding cells
Cobot welding cells are game-changers for shops that embrace them properly. The combination of safety, flexibility, and reasonable cost makes them accessible to manufacturers who couldn't justify traditional robotic welding.
Best choice
Standard Bots RO1 delivers the best balance of capability, ease of use, and value I've tested. The built-in vision and no-code programming work exactly as advertised.
When do alternatives work better?
High-volume production still favors traditional robots, and truly custom work needs human welders.
Bottom line: If you're manually welding repetitive parts and struggling with welder availability, a cobot cell pays for itself faster than almost any other automation investment.
Ready to automate your welding with Standard Bots?
Cobot welding cells eliminate the most dangerous, repetitive welding tasks while freeing your skilled welders for complex work that actually requires human expertise.
Standard Bots’ RO1 is the perfect six-axis cobot addition to any shop floor, big or small.
- Affordable and adaptable: Available at half the cost of comparable robots, with a list price of $37K.
- Precision and power: With a repeatability of ±0.025 mm and an 18 kg payload, RO1 handles even the most demanding jobs, like welding, palletizing, and pick-and-place. You name it.
- AI-driven simplicity: Equipped with AI capabilities on par with GPT-4, RO1 integrates perfectly with production systems for even more advanced automation.
- Safety-first design: Machine vision and collision detection mean RO1 works safely alongside human operators.
Schedule your on-site demo with our engineers today and see how RO1 can bring AI-powered greatness to your shop floor.
FAQs
1. How much does a cobot welding cell cost?
Complete cobot welding cell costs range from $35K to $75K, depending on welding equipment and accessories. Standard Bots RO1 starts at $37K, and makes automation accessible even for smaller shops.
2. Can cobots do TIG welding?
Yes, cobots excel at TIG welding thanks to their precise positioning and smooth motion control. The consistent travel speed and torch angle produce higher quality TIG welds than most manual welders can achieve.
3. Do cobot welding cells require safety fencing?
No, collaborative robots do not need safety fencing or cages because cobots are designed to work safely alongside humans. Built-in force limiting and collision detection allow operators to work directly with the cobot during setup and part loading. Plus, all welding operations must comply with OSHA 29 CFR 1910.252 fire prevention and safety requirements.
4. How long does it take to program a cobot welding cell?
Programming simple weld patterns takes 15 to 30 minutes with no-code systems like RO1. However, complex multi-pass welds might require 1 to 2 hours of programming and testing to optimize parameters.
5. What's causing the welder shortage?
The welder shortage is mostly caused by the aging workforce. The American Welding Society reports we’ll likely need 330,000 new welders over the next four years due to the aging workforce (average age 40 to 55) and a lack of interest from younger workers entering the trade.
Join thousands of creators
receiving our weekly articles.