There’s a reason your favorite tech gadgets and car parts don’t look like a kid assembled them during a grade-school recess. It's because they weren’t. They were built by AI-driven assembly robots that don’t miss a step, don’t blink, and don’t ask for a raise when they have to work overtime.
Modern robotic assembly is faster, smarter, safer, and significantly more scalable.
With the International Federation of Robotics reporting that over 4 million robots are operating in factories worldwide (10% up from 2023), it’s plain to see that whether you’re building smartphones, sedans, or syringes, bots are now the kings and queens of heavy lifting.
In this article, we’ll cover:
- What assembly robots are
- Why factories are shifting
- Types of assembly line robots and core components
- Real-world applications
- How to implement robotic assembly
- Key challenges and the future of assembly robots
What are assembly robots?
Assembly robots are machines designed to automate the process of putting stuff together — whether it’s microchips or motor mounts. They’re the behind-the-scenes secret sauce of manufacturing — no fame, no flash, just real “get it done” energy.
While traditional automation relied on conveyor belts and fixed stations, robotic assembly lines evolved to handle more complex parts and variable production. Think less Henry Ford, more SpaceX.
Where did they come from?
Assembly robots first started appearing in the auto world back in the 1960s, mostly as glorified spot welders. Now they’ve leveled up with multiple axes of motion, machine vision, and software smarts that let them adapt to ever-changing jobs.
Industries that use (and love) assembly robots
- Automotive: For anything from engine assembly to windshield installation, robots do it cleaner and faster than human hands.
- Electronics: When components are the size of a Tic Tac and tolerances are nanometers, precision is life.
- Consumer goods: From vacuum cleaners to VR headsets, robots keep the line running without a drop in output quality.
- Medical manufacturing: Sterile, consistent, and exact — all robot specialties.
We’re past the point of “robots are coming.” In assembly line robotics, they’re already clocked in.
Why are factories shifting to robotic assembly?
Let’s be real — humans are great at inventing things, but not so great at assembling 40,000 of them a day with zero mistakes. That’s where robotic assembly’s benefits steps in: no burnout, no bad moods, no dropping screws into impossible places.
Here’s why factories are making the switch — and not looking back:
- Speed and consistency: Robots can outpace humans on repetitive jobs and do it with repeatable accuracy. Still, they don’t walk on water — they need proper programming, clean environments, and the occasional reboot. (Or kick up the chassis.)
- Fewer mistakes where it matters: Assembly bots rock at high-precision, high-volume work. They’ll place components with millimeter-level accuracy — assuming they’re working with reliable parts and rigorously tested instructions.
- Labor cost efficiency for the long game: While they’re not cheap upfront, robots reduce your dependency on hard-to-scale labor. Over time, they lower your cost-per-unit, especially when production needs climb.
- Better safety for tough jobs: When the job involves sharp parts, awkward reaches, or mind-numbing repetition, robots step in and lower injury risk. Just don’t skip out on proper training — even the friendliest robot arm can smack into someone if left unsupervised.
- Scales very well (but not infinitely): Robotic systems shine when you’re producing thousands of the same part. Custom jobs? Those might still need some human finesse or clever system design to work around the quirks.
Types of assembly line robots
From lightning-fast pick-and-place units to multi-jointed arms with wrist flexibility that would make a yoga teacher jealous, each robot type brings its own specialty to the assembly game.
Here’s a breakdown of the most common players in robotic production lines:
- Cartesian robots are straight shooters with ruler energy: These three-axis robots move in straight lines along the X, Y, and Z axes. They’re great for precise, repetitive motions like gluing, placing, or picking — but don’t ask them to dance.
- SCARA robots are speed specialists: They’re fast, accurate, and perfect for 2D assembly jobs like putting together circuit boards. Their small footprint makes them a hit in electronics and compact lines. Learn more about SCARA robots.
- Articulated robotic arms for multitasking: These flexible arms can twist, rotate, and reach with a full range of motion. Great for more complex assembly, especially when the parts come in at weird angles or need finesse.
- Delta robots, or the spiders of the production floor. Their tripod design makes them insanely quick for small-part handling. They’re used when you want to move lightweight stuff, really fast — like packaging or sorting.
- Collaborative robots (cobots) are friendly bots with manners: Cobots can work safely alongside human workers — they stop when you bump them and don’t swing elbows like traditional industrial arms. Ideal for flexible, small-batch assembly and dynamic workspaces. Take a look at our full guide to cobots.
Core components of a robotic assembly line
You wouldn’t build a sandwich without bread and cheese (unless you’re doing something cursed) — and you can’t build a solid robotic production line without the right parts either.
We've put together a quick overview of the components below.
Here’s what makes the modular squad tick:
- Robotic arms: These are the muscles of the whole assembly. Whether you’re picking up microchips or car doors, articulated arms bring strength, precision, and flexibility. Some even have wrist articulation smoother than a jazz pianist.
- End-of-arm tooling (EOAT): Grippers, suction cups, welders, screwdrivers — this is the robot’s “hand,” and it’s what gives each bot its specific job. For a deeper dive into EOAT, check out this guide on grippers.
- Vision systems: Robots don’t need eyes — but they’ve got them anyway. Camera-based systems help with part recognition, quality control, and guiding arms to the right spot (especially when parts come in crooked or randomly spaced).
- Conveyors + automated feeders: Without a steady stream of parts, your robot is just awkwardly waiting around. These systems keep everything flowing and make sure the robot always has something to grab.
- Controllers and software: Controllers interpret code and sensor data to direct movement, while the software handles programming, job planning, and adjustments. And yes, you can even simulate tasks before ever touching the real parts.
- Safety systems: Modern assembly lines include laser scanners, light curtains, and collision sensors to make sure no one gets whacked by an overenthusiastic robot arm. These are especially important for collaborative lines with both humans and bots.
Use cases: Real applications of robotic assembly solutions
From car factories to medtech labs, assembly robots are the quiet overachievers piecing together your daily essentials while the rest of us fumble with a laptop’s manual.
Here’s where they’re already crushing it:
- Electronics manufacturing: From smartphones to wearables, tiny parts are getting placed with terrifying accuracy by machines like FANUC’s LR Mate 200iD. These bots don’t flinch, sneeze, or misplace a resistor — which is probably why they’re trusted with your next phone’s internal circuitry.
- Automotive production: Robots aren’t just tightening bolts — they’re welding, routing wiring harnesses, and installing components in modern car plants like BMW’s Spartanburg facility. The whole process runs smoother than a freshly waxed hood.
- Medical device assembly: Clean rooms demand steady hands — or better yet, no hands at all. Universal Robots uses cobots to assemble items like insulin pens and surgical kits, ensuring sterility, precision, and zero sneezing fits.
- Consumer goods assembly: Whether it’s snapping together your electric toothbrush or aligning the hinge on your $300 headphones, robots are quietly handling millions of small plastic parts with soft-touch grippers and serious patience.
- Appliance and HVAC systems: Building your A/C compressor or water heater often involves a robotic arm doing the heavy lifting. Robots assemble valves, switches, and internal components while humans focus on QC and repairs.
- Packaging and logistics: You think humans are fast with a tape gun? Delta robots can pick, place, seal, and label at speeds that leave forklifts jealous — especially in food and pharma warehouses where hygiene and speed are non-negotiable.
How to implement robotic assembly in your factory
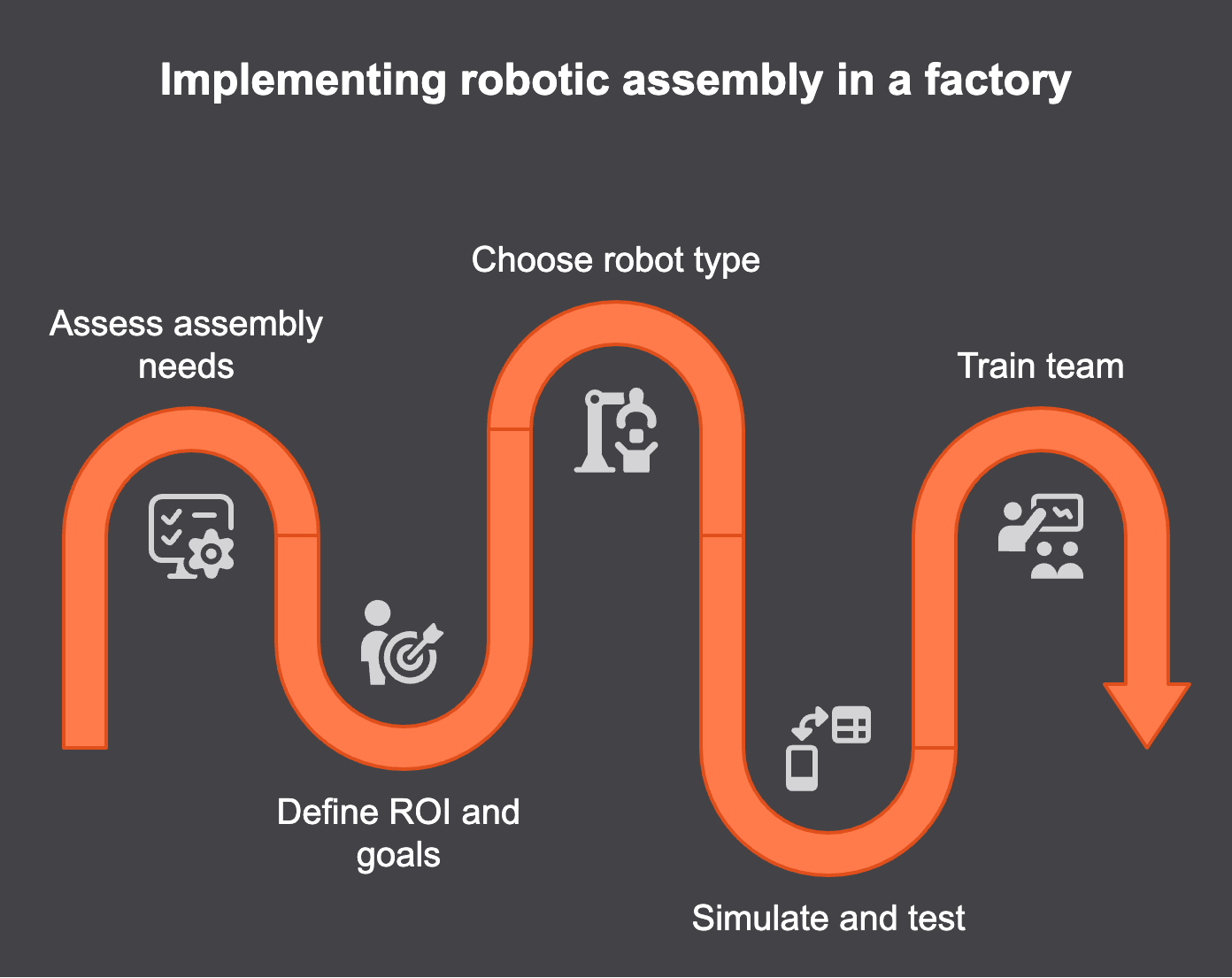
So you’re ready to implement robotic assembly — nice. But it’s not as simple as plugging one in and yelling “build stuff.” Start by pinpointing the boring, risky, or repetitive tasks, then set clear ROI-driven goals to guide your choices.
Pick the right robot and tooling for the job, run simulations to catch any surprises, and train your operators so no one panics when the robot casually waves hello.
Here’s your plug-and-play roadmap (minus the chaos):
- Assess your assembly process needs: Start by figuring out which parts of your line are slow, inconsistent, or just kinda miserable for humans. If it’s repetitive, boring, or dangerously hot — that’s robot territory.
- Define ROI and goals: Are you trying to speed things up? Improve quality? Cut labor costs? Knowing your “why” will help guide decisions on robot type, tooling, and integration. If your CFO doesn’t cry (in a good way) after the math, you’re probably on the right track.
- Choose your robot type and tooling: Cartesian, SCARA, articulated, or Delta? Each has strengths — and pairing it with the right gripper or EOAT makes all the difference. Don’t just pick what looks cool. Pick what works.
- Simulation and test integration: Before you roll out bots on the floor, test everything in a virtual sandbox. It’ll help avoid awkward “Uhhh, this arm is upside down” moments and smooth out timing bugs between systems.
- Train your team: Even if the robot runs on autopilot, your staff still needs to understand safety protocols, basic troubleshooting, and how to work with their new mechanical coworker (who, to be clear, will never bring donuts).
Key challenges of robotic assembly
Look, robotic assembly sounds amazing, and it is. But it’s not all slick code and laser-guided perfection. Getting bots on your line comes with a few spicy curveballs that every factory should be ready for.
Here’s what might trip you up (and how to avoid face-planting):
- Upfront costs that make your wallet wince: Robots aren’t cheap. Between hardware, integration, safety enclosures, and training, the initial price tag can feel like a punch to your CapEx. But long term? Most companies see major returns — especially once labor savings and reduced scrap kick in.
- Integration that’s part Tetris, part tech support: Plug-and-play? Sometimes. But most of the time you’ll need to match your existing line’s speeds, parts, and flow — and that can mean some custom engineering. Cobots help here, but even those need to be mapped properly into your system.
- Customization for short runs: If you’re producing 10,000 of the same thing every day, a robot is your soulmate. But for shops with smaller, highly variable batches, getting a robot to adapt without reprogramming everything can be, let’s say, “a journey.” Flexible EOATs and mobile cobots can help, though.
- Workforce reskilling and culture shifts: Robots don’t steal jobs — but they do change them. That means training folks to handle programming, maintenance, and working alongside automation. Some employees will love it. Others might need time — and, possibly, donuts.
The future of robotic assembly lines
Assembly robots are getting smarter, faster, and weirdly good at teamwork. AI optimization, cloud-based tracking, flexibility, and sustainability are defining the future of robotic assembly.
Here’s what the next few years of robotic assembly will probably look like:
- AI optimization becomes the new norm: Robots are starting to use AI to fine-tune their own movements, reduce cycle time, and adjust mid-job without human input. Think of it as your robot getting a brain upgrade — without a tech mogul chipping in.
- Cloud-based monitoring and control: Factory managers can now track performance, downtime, and maintenance needs remotely, often from a phone. Platforms like Standard Bots’ RO1 AI-enabled systems let you update programs without needing to put on safety boots.
- Much more flexibility via mobile and modular robots: Fixed robots are cool and all, but wheeled robots and modular designs are hotter than a soldering iron. Need to reconfigure your line fast? Just move your cobots around and tweak the code.
- Sustainability perks baked into automation: Assembly bots waste fewer materials, run on optimized energy cycles, and reduce factory emissions just by showing up. And since they’re super consistent, fewer bad parts end up in the trash — or worse, in your customer’s hands.
Summing up
Assembly robots are already deep in the trenches, tightening screws, placing components, and keeping production humming while humans focus on the big-picture stuff (like lunch breaks and Spotify playlists).
The long-term payoff: Fewer errors, faster cycles, less burnout, and way fewer “why did we do it this way?” meetings. Robots assemble better — and smarter — than ever.
Next steps with Standard Bots
RO1 by Standard Bots is your new six-axis coworker with elite assembly skills, AI brains, and no attitude.
- Affordable and adaptable: Skip the overpriced systems — RO1 delivers top-tier automation at half the cost, or lease it starting at just $5/hour.
- Precision and strength: With ±0.025 mm repeatability and an 18 kg payload, RO1 handles everything from circuit boards to engine components with dead-on accuracy. Welding, CNC machine tending, pick-and-place, painting, assembly? No problem.
- AI-driven and user-friendly: A no-code interface plus GPT-4-level intelligence means anyone can program RO1 — no engineering degree needed, no meltdown when specs change.
- Safety-minded design: Built-in machine vision, collision detection, and smart sensors make RO1 safe to work right alongside your human team.
Book your risk-free, 30-day onsite trial today and see how RO1 can turn your assembly line into a robotic efficiency machine.
Join thousands of creators
receiving our weekly articles.