Manual welding vs. robot welding is more than a tech debate. It’s the real-world difference between Iron Man and a guy with a torch and a good playlist.
In 2025, we’re talking about which gets the job done faster, safer, and with fewer reworks, not which is better in theory. Manual welding excels at flexible, custom, or irregular jobs, whereas robotic welding offers higher consistency and long-term affordability for repetitive tasks. But that’s just the start.
We’ll cover everything from torch control and speed to training and ROI. So whether you're team arc flash or team automation, you'll walk away with a clear winner.
Manual vs. robotic welding: TL;DR
What is manual welding?
Manual welding (also called hand welding) is exactly what it sounds like. A person, a torch, a steady hand, and some old-fashioned patience.
It’s how most welders start out, and it’s still the go-to for jobs that require flexibility, quick setup, or good ol’ human improvisation. You’ve seen it in fab shops, garages, construction sites, basically anywhere there’s metal and fire. (That’s not a Metallica concert, at least.)
Common manual welding methods
- MIG welding (GMAW): Fast and relatively easy to learn. Good for steel, stainless, and aluminum. Often the first stop for new welders.
- TIG welding (GTAW): Slower but cleaner. More control, more precision. It’s perfect for detailed welds on thinner materials.
- Stick welding (SMAW): The no-nonsense method. Rugged, portable, works even if the surface is dirty or rusty. Great for field repairs.
- Flux-cored arc welding (FCAW): Like MIG but with self-shielding wire. It’s great for outdoor jobs or thicker metals.
Basically, manual welding still thrives in settings where parts vary, access is awkward, or a human’s instinct makes the difference. For repair work, prototyping, or weird one-offs, the flexibility is hard to beat.
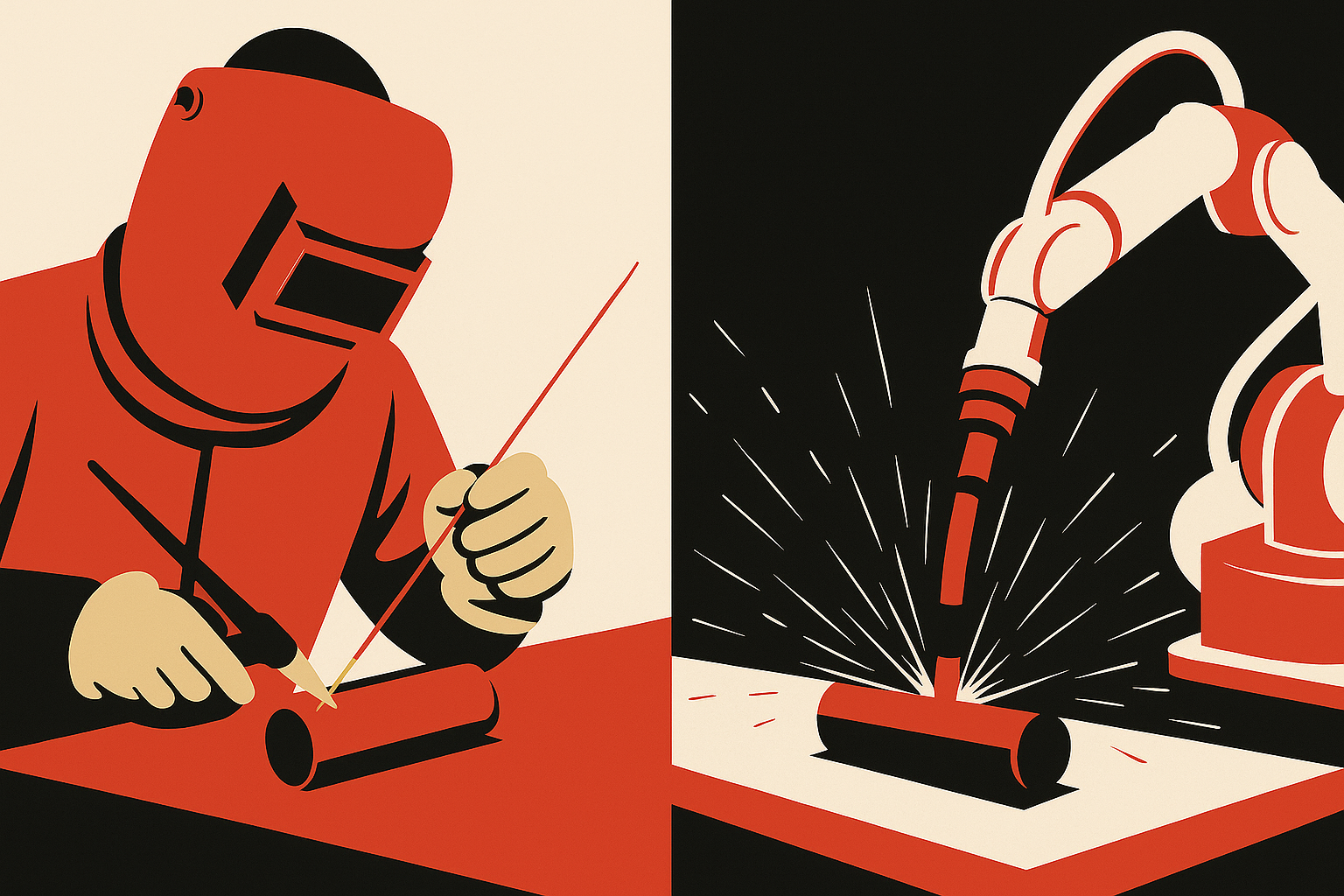
What is robot welding?
Robot welding is what happens when a robotic arm takes over torch duty. It automates the entire weld cycle from positioning to puddle control.
We’re talking the whole gamut from a fully enclosed six-axis beast or a friendly cobot working next to your crew, the goal’s the same. Robots create consistent, repeatable welds without human error or burnout. (Of course, errors happen, that’s life, and even robots mess up.)
It’s not just for big factories anymore. Thanks to systems like RO1, robotics welding now fits on shop floors where the biggest machine used to be a MIG cart with a Bluetooth speaker duct-taped on.
Types of welding robots you’ll see in the wild
- Articulated arm robots: These look like something out of Pacific Rim, multijointed, ultra-flexible, and built to work across all planes. Great for large parts or multi-angle welds.
- Gantry robots: These glide overhead like a rail shooter. Perfect for linear welds or parts that require high-speed consistency. Check out how gantry robots actually work for a deeper dive.
- Collaborative robots (cobots): These play nice with humans. Smaller, safer, and easier to program. RO1 is a prime example, a robotic arm welder that can switch from welding to CNC tending mid-shift while asking for seconds.
Manual vs. Robotic Welding: At a glance
Here’s the showdown. One’s a guy in a helmet with steady hands, the other’s a six-axis robot that doesn’t take bathroom breaks.
Manual welding vs. robotic welding: Feature-by-feature comparison
Weld quality: Manual vs. robotic
A good weld means consistency, penetration, and knowing you won’t have to grind off the bead and start over. Both manual and robotic welding can deliver great results, but they get there in different ways.
What affects weld quality in real-world jobs?
- Manual welds depend heavily on the operator: A skilled manual welder can produce excellent results (especially in TIG or stick). But human factors like fatigue and part variation introduce inconsistency, often in the ±1–2 mm range.
- Robotic welding delivers repeatability across shifts: Most robotic arms hold tolerances within ±0.1–0.3 mm, making them ideal for long runs or any job where bead consistency and cosmetic finish matter. Weld paths are pre-programmed, so there’s no drift, even at the end of a shift.
- Advanced setups offer even tighter control: Higher-end systems, including robotic MIG and robotic TIG welding platforms, support adaptive welding features like seam tracking and arc sensing, which adjust in real time to improve weld integrity.
Winner: Robotic welding takes the edge for consistency and visual quality in repeatable jobs. But for irregular parts or specialty welds, manual welding still holds its ground.
Training: Manual vs. robotic
There’s a learning curve, but the question is how steep, and how much time (and money) you’re willing to spend climbing it.
How long does it actually take to get productive?
- Manual welding takes years to master: Programs like those from AWS estimate 1–3 years to become proficient, especially in TIG and pipe welding. You’re learning hand position, puddle control, metal behavior. All by feel. It’s a skill, and it shows.
- Robot welding can be taught in a day: Most modern systems, especially those using UIs or drag-and-drop programming, require just a few hours to get started. Advanced platforms support both operators and engineers, so you can scale from simple jobs to fully integrated automation.
- Upskilling is faster with robotics: Shops can get newer employees productive quickly, even without prior welding experience. Plus, training time doesn’t spike if the part changes, you can swap in a new file or tweak parameters instead of re-teaching muscle memory.
Winner: Robotic welding wins on time-to-productivity, especially in small-to-medium shops that need to scale without waiting on a journeyman.
Safety: Manual vs. robotic
Welding isn’t exactly known for being gentle on the human body. Between the UV exposure, flying sparks, toxic fumes, and repetitive motions, a long welding career often comes with a back brace and a cabinet full of eye drops. But robots don’t breathe or flinch; they’re the cool guys that can look at explosions.
How does safety compare in day-to-day reality?
- Manual welding exposes workers to everything: Fumes, arc flash, extreme heat, and repetitive strain injuries are all part of the deal. Even with PPE and fume extractors, risks remain, especially in tight spaces or high-volume jobs. OSHA flags welding as one of the highest-risk skilled trades.
- Robotic systems isolate the risk: Whether it’s a full industrial cell or a collaborative setup, robotic welding reduces operator exposure. The human sets up, the robot does the hot, dangerous part. Systems follow ISO 10218 safety standards, and many include built-in collision detection, light curtains, and auto-shutoffs.
- Cleaner shop, less exposure: Robots don’t need fans, breaks, or coffee. That means enclosed systems are easier to ventilate, and they don’t track fumes all over the workspace. In high-output environments, this makes a real difference for air quality and long-term team health.
Winner: Robotic welding. The less your team is directly exposed to heat, fumes, and physical strain, the safer (and more productive) everyone becomes.
Cost: Manual vs. robotic
Welding might look like sparks and metal, but the real burn comes from the bill. And while manual welding has a low entry cost, it racks up fast with labor, rework, and downtime. Robotic welding flips the script. You pay more up front, but you’ll pay way less per part.
What do the numbers look like across a year?
- Manual welding = ~$60K/year per operator: That includes salary, taxes, benefits, consumables, and the overhead of slowdowns, sick days, and rework. And if you’re doing high-volume jobs, you’ll need multiple welders.
- Robotic welding systems = $35K–$150K total investment: Collaborative welding setups start around $35K–$50K. Fully integrated industrial cells can go to six figures. But once installed, they can run 24/7 with little human input. Maintenance is low, and programming time drops with each job.
- Cost per part favors robots fast: In batch production, the robot wins after the first few dozen parts. Less rework, less waste, less labor. Add in lower consumable use and higher uptime, and the robot’s true ROI starts kicking in within 12–24 months for most shops.
Winner: Robotic welding, if you’re producing more than just one bracket a week. Manual still wins for small shops doing irregular, short-run jobs with tight budgets.
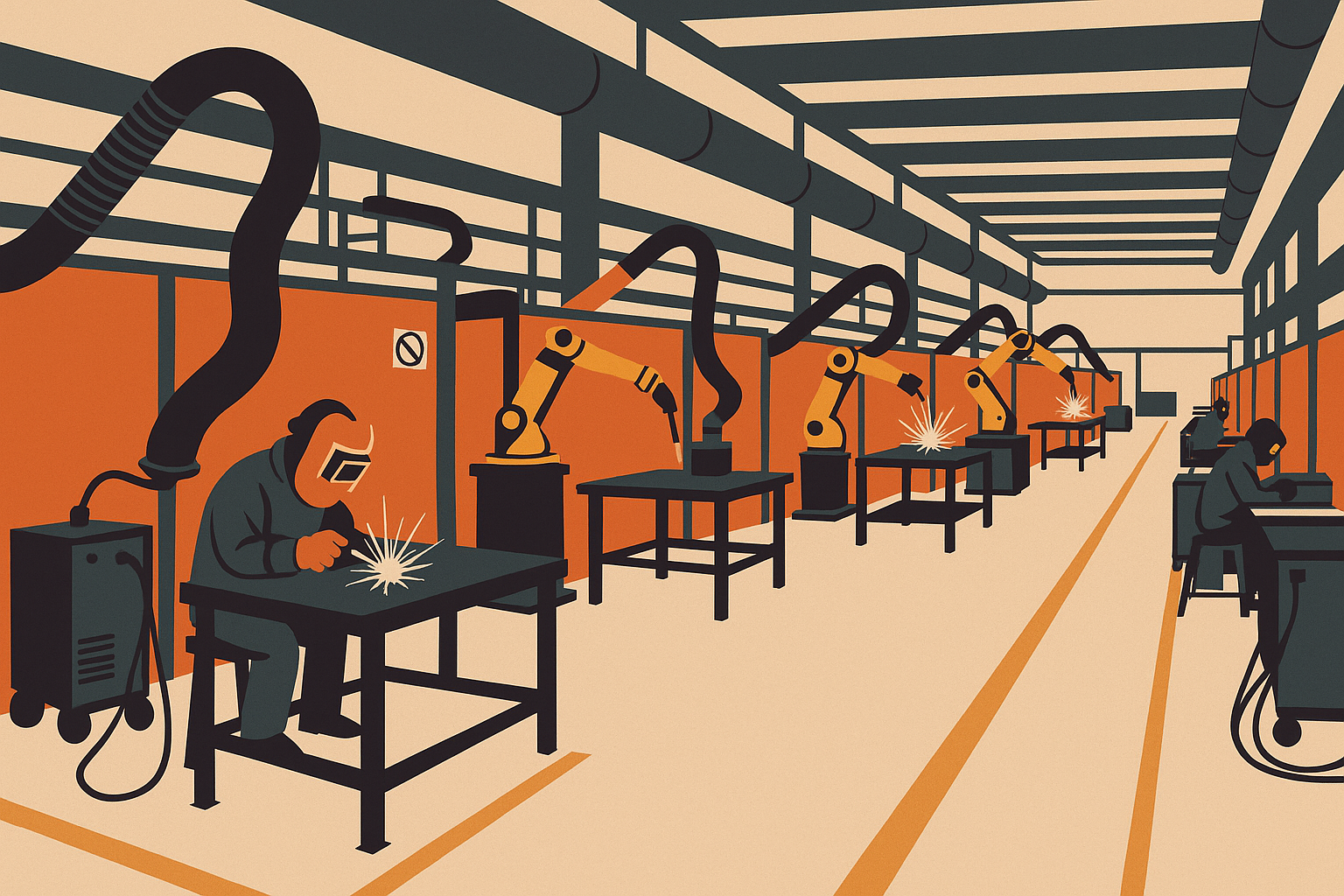
Best for: Manual or robotic?
If you're still on the fence, think about this less like “which is better?” and more like “which one actually fits your shop without making your life harder?” Here’s where each tool makes the most sense.
Go manual if you need
- Repair and maintenance work: Field jobs, welds in awkward spots, or quick patch jobs aren’t worth programming; just pick up the torch.
- Low-volume or one-off jobs: Prototyping and R&D still need some love. You don’t program a robot to weld one part that’ll never exist again.
- Tight or irregular geometries: Sometimes, nothing beats a human’s ability to adapt on the fly when the angles get as weird as a Nolan movie.
Go robo-welder if you’ve got
- Repeatable parts and batch production: Once a weld path is dialed in, the robot never drifts, no coffee breaks, no call-outs.
- Labor-strapped shops: When finding and keeping skilled welders is tough, a robotic cell fills the gap without lowering quality.
- Scaling up MIG/TIG on steel or aluminum: Perfect for medium-to-high volume runs where speed and consistency beat creative torch work.
User reviews
Manual welding: What welders actually say
- “Yeah, that is what’s happening … once I put my mask down and start the arc, I tense up and start shaking.” SuperheroR08 discussing tremors and shakiness during hands-on welding in American Welding Society.
- “I guess my only option is to try another job.” A 72‑year‑old welder explaining how tremors impact his ability to MIG in tight spots – Welding Tips and Tricks.
Pros highlighted
- Adaptability in odd spaces: Users often note that manual welding allows them to weld in cramped or unconventional setups without needing a programmed path.
- Immediate startup: One forum post emphasized that with manual welding, you literally “pick up the torch and go.” No cell setup or code.
Cons commonly voiced
- Hands get tired: As shared by SuperheroR08, physical strain affects bead control and consistency.
- Health risks are real: Forum users frequently mention wrist strain, back pain, and long-term joint issues, with one user noting, “fatigue is the biggest danger of all.”
- More age = more unsteadiness: A user explained that mobility issues and shaky hands forced him out of certain weld types as he got older.
Robotic welding: The operators weigh in
From a Reddit user weighing options for a small robotic setup:
- “A cobot would definitely be advantageous for you … Most are just move the head to the start and then program traverse speed.”
And from industrial robotics threads about vendor selection:
- “The best robot is the one you can obtain, program, and get service & parts for …” RobotforumEng-Tips.
Pros noted by the field
- Robots don’t tire, they run the same weld, hour after hour
- Shops report safer environments with less worker exposure
- One operator can manage multiple robots
Cons operators point out
- “Initial setup … may require significant investment of time and resources” (Reddit)
- Robots can struggle with odd geometries without reprogramming
- Reliability depends heavily on vendor support (“avoid bundles if the vendor might disappear”) RobotforumEng-Tips
Real ROI: Is robotic welding worth it for small shops?
For small shops, robotic welding seems like a big-company move. High price tag, long setup, probably needs a guy in a lab coat. But here’s the part no one tells you, manual welding gets expensive fast, especially when the jobs start stacking.
What you’re already spending:
- One full-time welder = $60K+/year: That’s wages, taxes, benefits, and downtime. Doesn’t include rework from fatigue or the cost of losing your best guy mid-shift.
What automation actually costs:
- A robotic welding system = $35K–$150K, all-in: That includes the arm, welder, table, fixturing, and software. If that sounds steep, remember that’s one time; not per year.
Payback math (not theory):
- Break-even happens in 12–24 months (but could be as soon as 6 months!) for most batch-production shops. Once it’s running, the robot doesn’t need breaks, doesn’t burn out, and doesn’t care if the job is boring AF.
What you stop paying for:
- Rework from sloppy fatigue welds
- Lost time from sick days or labor shortages
- PPE, insurance bumps, injury downtime
- Multiple welders on one job that a robot could handle solo
Still unsure? Here’s a quick checklist
If you’re stuck deciding between manual welding vs. robot welding, don’t overthink it. Just answer these. Fast.
Still balancing trade-offs? Good. That means you’re building the right system for how you actually work.
Next steps with Standard Bots’ robotic solutions
Looking to upgrade your automation game? Standard Bots’ RO1 is the perfect six-axis cobot addition to any CNC setup, delivering unbeatable precision and flexibility.
- Affordable and adaptable: Available at half the cost of comparable robots, with a list price of $37K.
- Precision and power: With a repeatability of ±0.025 mm and an 18 kg payload, RO1 handles even the most demanding CNC jobs.
- AI-driven simplicity: Equipped with AI capabilities on par with GPT-4, RO1 integrates seamlessly with CNC systems for advanced automation.
- Safety-first design: Machine vision and collision detection mean RO1 works safely alongside human operators.
Schedule your risk-free, 30-day on-site trial today and see how RO1 can bring AI-powered greatness to your shop floor.
FAQs
1. How accurate are robotic welds compared to manual welds?
High-end robotic welding nails tolerances around ±0.1 mm, think laser-guided Sharpie lines. Manual welders average ±1–2 mm once fatigue and hand shakes kick in, so robots win on consistency.
2. What types of welding can robots perform?
Robotic systems tackle MIG, TIG, flux-core, and even plasma welding if you’ve got the gear. Their robotic arm welder setups swap torch heads faster than you can say “spatter.”
3. Can a robot replace a skilled welder?
Robots can replace skilled welders for repeatable parts (or repetitive tasks). They crush batch production and hygiene-grade consistency. However, for oddball geometry, a skilled manual welder still brings the necessary human touch.
4. How much does robotic welding cost?
Expect $35K–$150K per system, with arm, power source, fixturing, and software included. Entry-level cobots hit the low end; full industrial cells climb to six figures fast.
5. Do I need a fixture for robotic welding?
Absolutely. Fixtures lock part position, so the robot doesn’t daydream mid-pass. No fixture = no repeatability = scrap city.
Join thousands of creators
receiving our weekly articles.