The biggest difference is that Industry 4.0 is all about data and connectivity, whereas Industry 5.0 is bringing humans back into the picture, with extra emphasis on being human-centric. Both 4.0 and 5.0 are currently fighting for custody of your production line.
Welcome to the era of Industry 5.0 vs. Industry 4.0, where smart factories evolve from “machine efficiency” to “machine + people, working weirdly well together.”
Key differences between Industry 4.0 and Industry 5.0
Industry 4.0 gave us robots that could work alone. Industry 5.0 gives us robots that text us back. Same machines, different priorities, and honestly, way better vibes for the humans involved.
Here’s how Industry 5.0 vs. Industry 4.0 breaks down (and no, this chart won’t put you to sleep):
Want more proof? Here’s what collaborative robots are doing in real factories right now, and how the human-robot thing works out in real life.
What is Industry 4.0?
This was the revolution where your factory stopped being mechanical and started being self-aware. Sensors showed up. Dashboards exploded. And suddenly, machines were talking to machines — right there, in actual real time.
What is Industry 4.0? It’s cyber-physical systems, smart automation, and cloud-synced everything. The Industry 4.0 meaning is simple: digitize everything, then make it all talk.
Industry 4.0 kicked off in the early 2010s when German industry leaders and policymakers coined the term to describe the shift toward digital, interconnected factories. It followed the rise of automation and electronics in the late 20th century, but this time, everything got a sensor, a data feed, and a cloud login.
How does industrial automation 4.0 work?
Industrial automation 4.0 brings faster decisions, tighter control, and potentially fewer mystery shutdowns. No promises, but definitely more visibility.
- Machines that overshare: Sensors feed pressure, heat, uptime, cycle time; if it moves, it’s probably tracked.
- Less guessing, more forecasting: Predictive maintenance can flag issues before they hit, if your data’s clean and the setup’s dialed.
- Dashboards everywhere: From plant managers to line techs, everyone’s got a screen telling them something’s 87.3% normal (on a good day).
- Robot arms doing their thing: Pick, place, weld, glue. And yes, this guide breaks down what robotic arms can actually do.
What is Industry 5.0?
Industry 5.0 is what happens when we stop trying to replace humans and start designing tech that vibes with them. Less “eliminate the operator” — more “make the operator 10x faster, happier, and less likely to throw a wrench.”
So, what is Industry 5.0? It’s the next phase of smart manufacturing, focused on human–machine collaboration, personalization, and building factories people don’t dread walking into.
Industry 5.0 is a response to the limitations of 4.0 — and the EU helped define it in 2021 as a way to build more resilient, human-centric manufacturing. Where 4.0 prioritized data and automation, 5.0 brings humans back into the spotlight with tools that work alongside, not around, real people.
What makes Industry 5.0 so different?
- Cobots doing side quests: These robots don’t work near humans — they work with them right in the trenches. Need proof? Here’s a full breakdown of collaborative robots.
Example: In the automotive sector, SEAT Components successfully integrated 10 cobots from Universal Robots using only internal resources. This shows how accessible this technology is.
- Sustainability that’s not a buzzword (usually): Less waste, smarter energy use, and material precision are actually achievable with the right setup.
- Custom everything, kinda fast: High-mix, low-volume production doesn’t have to be a nightmare. 5.0 tools make personalization more feasible than it used to be.
- AR, AI, and all the acronym friends: Operators get overlays, real-time prompts, and assistance, not just dashboards yelling at them post-failure. (And usually, an expensive failure at that.)
- People-first by design: The whole point is to build systems around human strengths, not treat people like backup plans for automation.
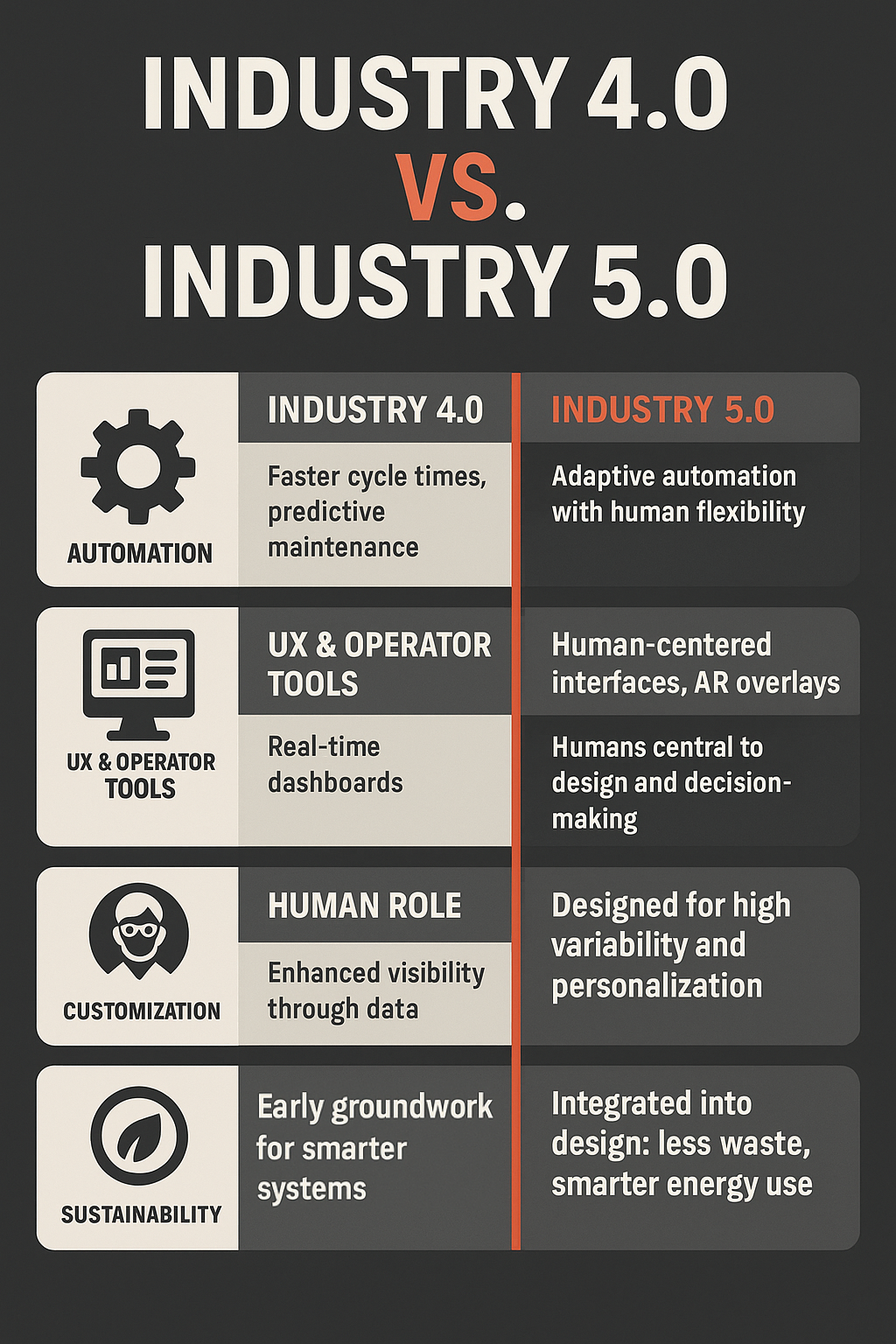
The value and limitations of Industry 4.0
Industry 4.0 didn’t fix everything. It made machines smarter, but humans often fell by the wayside. Here’s where it delivered, and where it didn’t.
Where did Industry 4.0 make an impact?
- Predictive maintenance is a lifesaver: Downtime alerts and sensor-driven schedules reduce the whole “surprise breakdown at 4 p.m. on a Friday” routine.
- Process visibility leveled up: Real-time dashboards help managers make faster calls — assuming they trust the data (and the Wi-Fi holds up).
- Cycle times went down (for some): Automation helped speed up repetitive steps, especially in high-volume, low-variation lines.
- It made robotics less scary: Many factories went from zero to smart-arm thanks to Industry 4.0 tools and tech. Take a look at how robot arms work in these setups.
Where did Industry 4.0 fall short?
- Personalization was … kind of a joke: It’s great for mass production, but what if you wanted high-mix, low-volume customization? Good luck reprogramming everything fast.
- UX was a mess: Dashboards that felt like spreadsheets, alerts that made no sense, and training manuals from 1997.
- People got pushed out: The focus was on efficiency, not on keeping humans in the loop or designing systems they wanted to work with.
Industry 5.0: What are the opportunities?
Industry 5.0 opens up possibilities that weren’t even on the table before. Customization, flexibility, and machines that make life easier for operators? Yeah, that’s new.
For example, global appliance manufacturer Haier used Industry 5.0 principles to empower its employees as value creators. Haier integrates smart tech and enables mass customization, proving that human-centric innovation drives flexible and resilient manufacturing.
- High-mix doesn’t have to mean high stress: With cobots and adaptive automation, it’s possible to switch product types without needing a full team huddle and a 48-hour reprogramming window.
- People are making a difference again: Human oversight leads to smarter decisions. You don’t need 1,000 sensors to know when a part is off — sometimes a technician with a good eye catches it first.
- Sustainability becomes real, not performative: More precise dosing, less overproduction, and better material control all start adding up fast, especially at scale.
- Human–AI collabs hit new levels: Instead of just tracking KPIs, 5.0 setups use AI to support in-the-moment decisions — with humans still behind the scenes.
How to transition from Industry 4.0 to 5.0
You don’t need to tear up your factory floor to make the leap — just layer smarter tools on what already works.
How to start making that shift in 5 steps
- Don’t ditch — upgrade: Most 5.0 tools, like cobots or edge AI, can be added to your existing 4.0 infrastructure. Think “add-on pack,” not full reinstall.
- Start with a pilot cell: Pick one use case — such as precision gluing or operator-guided assembly — and test it with a collaborative setup. Fast feedback, minimal risk.
- Train the humans first: Forget the 100-page manuals. Give your operators touchscreen interfaces, simulations, and actual time to upskill.
- Use cobots to break the ice: Deploy a six-axis cobot like RO1 in a space where it can assist, not replace. Once people see it sanding or tending without drama, adoption gets easier.
- Let the KPIs do the talking: Don’t try to sell 5.0 on theory. Track improvements in changeover time, defect rates, energy use, and operator satisfaction.
How Standard Bots supports the shift
RO1 by Standard Bots is a six-axis cobot for manufacturers in both worlds — fast, data-driven production and human-centric flexibility. It plugs into legacy lines easily, adapts to high-mix output, and doesn’t need a full team of engineers.
What makes RO1 built for the 4.0 to 5.0 transition?
- Fast deployment with no system shock: RO1 works with your existing machines, layouts, and tooling. No rip-and-replace is needed, typically.
- Built-in safety for close human collab: Vision systems, collision detection, and smooth force control make it safe to deploy where people are already working.
- Operator-friendly controls: You don’t need to write code or memorize a dozen shortcuts. Teaching RO1 is as simple as point, tap, go. No-code simplicity.
- Flexible across roles: Gluing, tending, sanding, inspecting — one unit, multiple use cases, all on a budget your CFO won’t side-eye.
Frequently asked questions
- Is Industry 5.0 replacing Industry 4.0?
No, and it’s not trying to. Think evolution, not exile. 4.0 laid the groundwork: automation, data, sensors everywhere. 5.0 just steps in with a fresh perspective and asks, “Cool, now how do we make this not soul-crushing for the humans still involved?”
- What industries are best suited for Industry 5.0?
Areas best suited for Industry 5.0 include anywhere a robot still needs a human co-pilot. That means electronics, consumer goods, medical assembly, aerospace, and even logistics. If your operators still have to think on their feet — or shift between jobs often — 5.0 tech like cobots and adaptive systems will help.
Mass production lines? Still 4.0’s turf. High-mix, mid-volume? That’s 5.0 territory.
- What is Industry 4.0 primarily used for?
Industry 4.0 rules in environments where predictability wins. If your process repeats all day and uptime is king, 4.0 gets you there faster with fewer surprises. Think automotive welding lines, bottling plants, or mega-factories where humans mostly tap buttons and check logs.
It’s smart, efficient, and not that flexible, which is fine when your SKU count is low and your demand is steady.
- Can I upgrade from 4.0 to 5.0 without replacing equipment?
Definitely, unless your setup is prehistoric. Most Industry 5.0 tech is designed to bolt onto what’s already there: cobots that work with legacy machines, AR overlays for analog processes, AI that reads from existing sensors. You don’t need to scrap your line, just retrofit and pilot.
Start small. One cobot cell, one digital twin test, one operator assist tool. Then expand what works.
- What is human-centric manufacturing?
It’s building systems around people instead of pretending humans are the bottleneck. In practice, it means tech that adapts to operators, not the other way around.
So, in place of a screen full of cryptic error codes, you get a cobot that pauses and waits. Instead of drowning in spreadsheets, you get dashboards that show what you need, when you need it.
- Is Industry 5.0 more sustainable than Industry 4.0?
It can be, depending on how you deploy it. With better human oversight, precision tools, and fewer one-size-fits-all processes, 5.0 setups can reduce material waste and energy use without sacrificing output.
- Can Standard Bots help with Industry 5.0 adoption?
Yes, and without making your floor feel like a software convention. RO1 is made for human–machine collaboration. It’s safe, flexible, and fast to teach. No code, no 30-step install guides, no robotic tantrums.
Use RO1 in CNC tending, light assembly, gluing, or anything where you want people + machines working together instead of stepping on each other’s toes.
Summing up
Industry 5.0 reintroduces people as active collaborators, prioritizing customization, sustainability, and meaningful human-tech interaction on the factory floor. In contrast, Industry 4.0 centers on digitized automation and interconnected machinery designed to streamline operations and reduce human involvement.
The conversation around Industry 5.0 vs. Industry 4.0 is more than a game of picking sides — it’s about knowing what tools to use and when. 4.0 gave factories their digital nervous system, while 5.0 brings back the heart.
The best setups now have the best of both worlds: Automation where it makes sense, and human-centric design where it makes an actual difference. That’s not a buzzword or a dumb trend; it’s how smart manufacturers are staying flexible, creative, and surprisingly resilient.
Next steps with Standard Bots
RO1 by Standard Bots is the six-axis cobot upgrade your factory needs to bridge Industry 4.0 and 5.0.
- Affordable and adaptable: Best-in-class automation at half the price of competitors; leasing starts at just $5/hour.
- Precision and strength: Repeatability of ±0.025 mm and an 18 kg payload make it ideal for CNC, assembly, and material handling, and a lot more.
- AI-driven and user-friendly: No-code framework means anyone can program RO1 — no engineers, no complicated setups. And its AI on par with GPT-4 means it keeps learning on the job.
- Safety-minded design: Machine vision and collision detection let RO1 work side by side with human operators.
Book your risk-free, 30-day onsite trial today and see how RO1 can help you level up both sides of your automation strategy.
Join thousands of creators
receiving our weekly articles.