Cobot TIG welding delivers aerospace-grade precision without the six-figure price tag or PhD in programming.
Manufacturing shops are switching to collaborative TIG welding robots, much faster setup times, and welds that pass X-ray inspection on the first try.
Research showed a 36% setup time reduction in welding robots, with a 43% reduction in motions during changeover processes. Cobot TIG welding handles aluminum, stainless steel, and exotic alloys with repeatability that makes manual welders jealous. Here's what actually works in 2025.
What is cobot TIG welding, anyway?
Cobot TIG welding is when collaborative robots (cobots) handle tungsten inert gas welding, a process known for being super precise but nearly impossible to master without years of practice. Cobots show up, follow the program, and deliver near-perfect welds like it's no big deal.
Think of it like having a surgeon's hands with a machine's consistency. Sensors constantly adjust for heat, alignment, and positioning to keep the weld flawless. Programming is drag-and-drop simple, so even non-techies can set them up without drama.
Cobots handle the technical execution while you focus on setup, programming, and quality control.
Key features that matter
How does cobot TIG welding actually work?
Cobot TIG systems combine robotic arms with TIG torches and adaptive control software to automate precision welding tasks. The process starts with path programming, then executes with constant sensor feedback.
Here's the step-by-step process:
- Path programming: Operators teach the cobot by guiding it through the desired weld path or using CAD files
- Parameter setup: Input material type, thickness, and joint configuration for automatic welding settings
- Sensor calibration: Vision systems locate parts and track seam positions for accurate torch placement
- Execution: The cobot follows the programmed path while sensors adjust heat, speed, and positioning in real-time
- Quality monitoring: Systems track arc stability, penetration, and consistency throughout the weld
Real example: Studies show that manufacturing facilities using robotic welding systems can increase productivity by up to 30% while significantly reducing setup times and improving weld consistency in production applications.
Cobot TIG welding vs. manual TIG welding: The honest breakdown
Manual TIG welding is the definition of stressful. It demands perfectly steady hands, endless patience, and years of practice to get consistent results. Cobots, on the other hand, don't have shaky hands or bad days. They bring robo-level precision to a job that's all about accuracy and control.
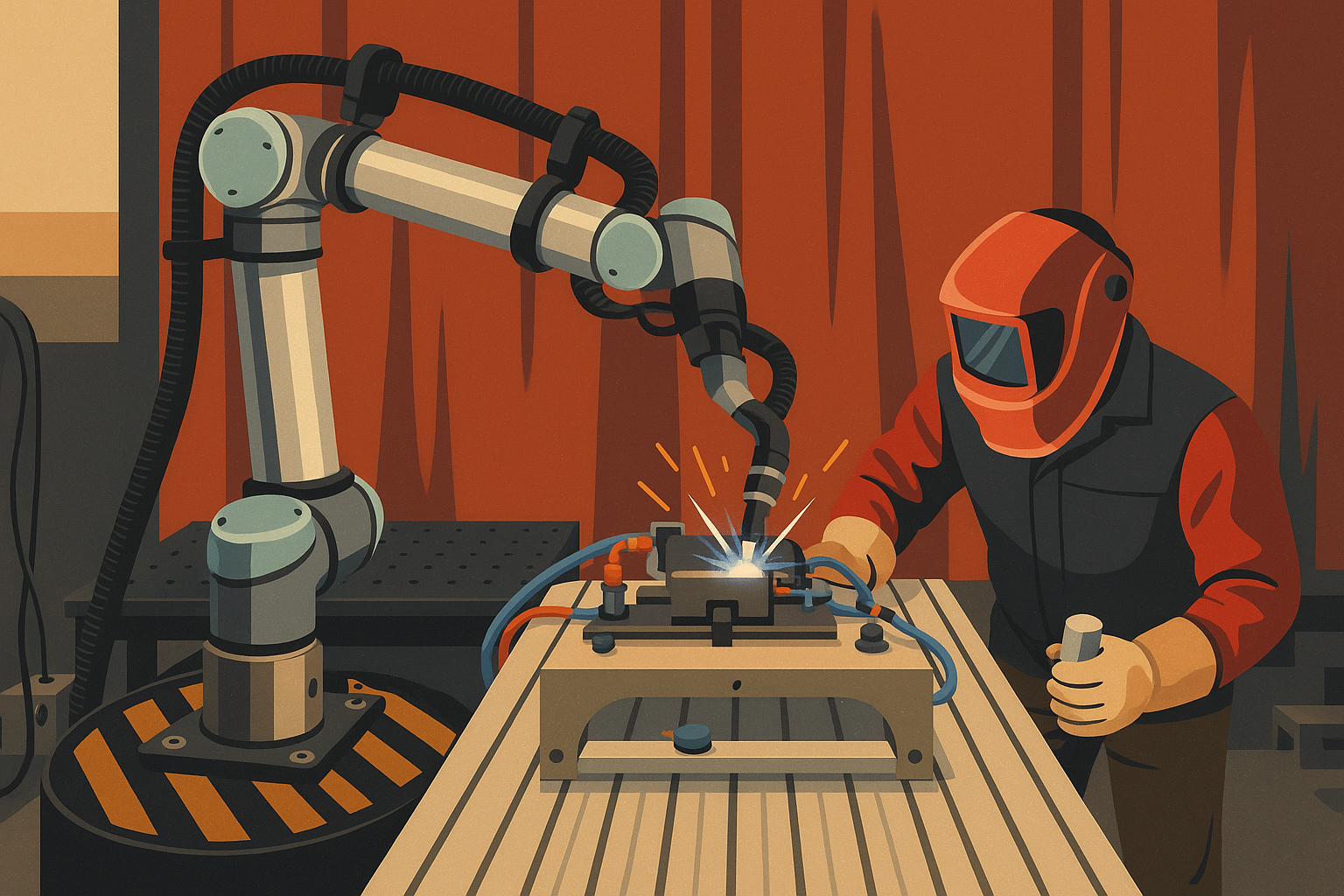
Based on industry data comparing both methods across multiple applications, here's how they stack up:
Winner: Cobots for repetitive production runs; manual for complex custom fabrication and repairs.
What works (and what doesn't) with cobot TIG welding?
Pros that actually matter
- Eliminates the learning curve: TIG welding requires extensive skill development and years of practice to master. Cobots deliver expert-level results from day one with proper programming.
- Handles difficult positions: Overhead and vertical welds that exhaus human welders become routine. Cobots maintain steady torch control regardless of position.
- Reduces material waste: Consistent penetration and bead placement cut scrap rates by 15–30% compared to manual welding on precision parts.
- Works through breaks: Continuous operation without fatigue means higher throughput on large production runs. Although, of course, they can break down and do need maintenance.
Cons you need to know
- Limited adaptability: Complex repairs or unique joint configurations need human judgment. Cobots excel at repetitive tasks, not problem-solving.
- High upfront costs: Quality cobot systems traditionally start around $75,000, though affordable options like RO1 bring costs down to $37,000.
- Programming overhead: Each new part requires path programming and testing. This makes cobots inefficient for one-off jobs.
Should you use cobot TIG welding? My take
Cobot TIG welding pays off when you have repetitive, high-quality welding requirements that justify the initial investment. This technology works best for manufacturers with consistent product lines rather than custom job shops.
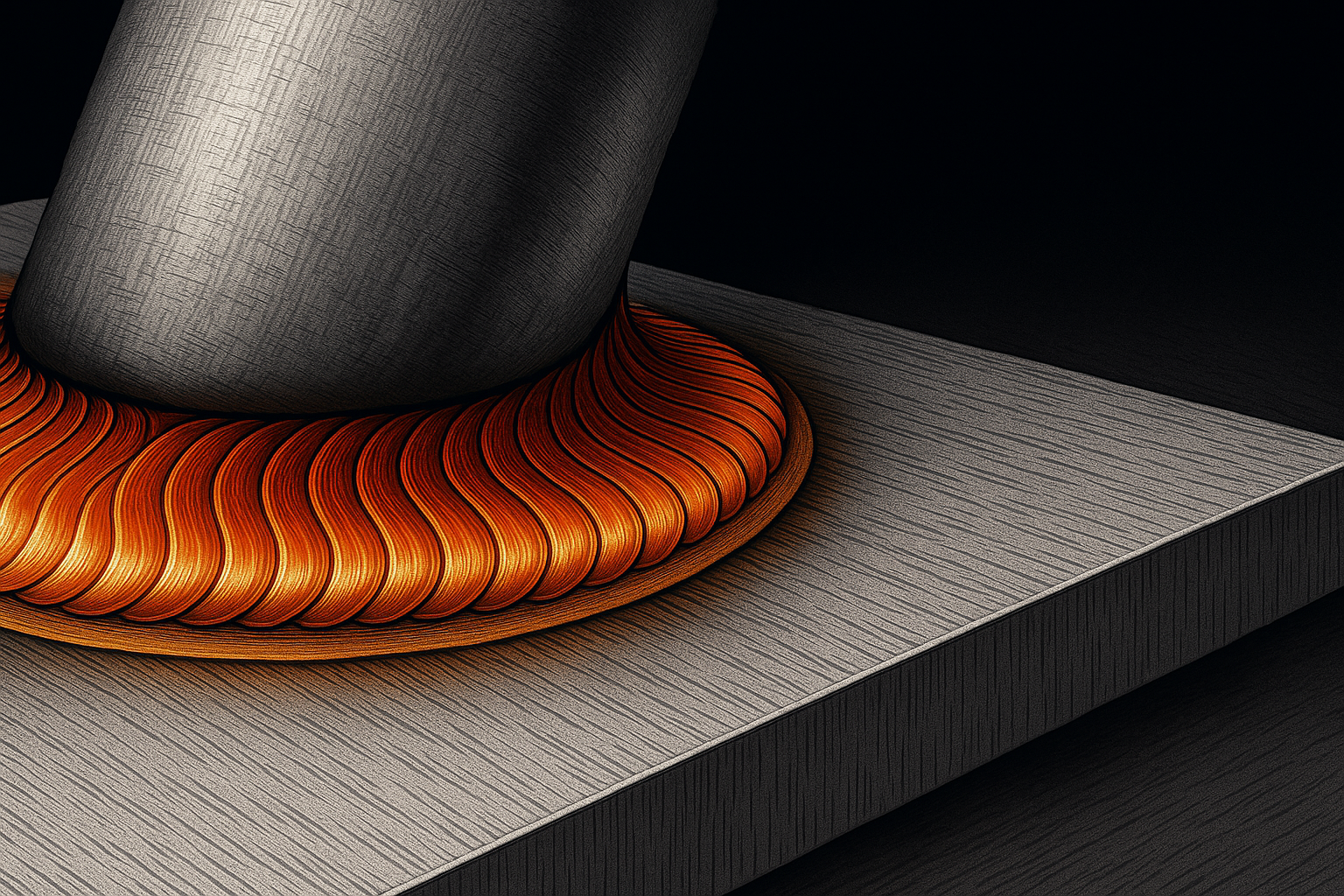
Cobot TIG welding is perfect for:
- Aerospace manufacturers that need identical welds on flight-critical components with full traceability and quality documentation.
- Defense applications where weld failure isn't an option with critical components, like turbine blades and structural joints.
- Medical device production where weld quality directly impacts patient safety and regulatory compliance under FDA standards, e.g., surgical instruments and implants that require biocompatible welds under strict quality standards.
- Automotive fabrication with high-volume runs of exhaust systems, roll cages, brackets, and structural components, requiring consistent quality for both safety and performance. Cobots handle critical automotive components with precision that keeps drivers safe.
- Food processing equipment, e.g., stainless steel fabrication, where consistent penetration prevents contamination risks.
- Small shops with skilled labor shortages that need consistent TIG quality without years of welder training. This addresses a critical issue given the projected 320,000 welder shortage by 2029, according to the American Welding Society.
Learn more about industrial automation applications across different sectors.
Skip cobot TIG welding if you:
- Handle mostly custom one-off projects where programming time exceeds welding time
- Work with complex geometries that require constant human judgment and adaptation
- Have budget constraints under $30,000 since quality cobot systems require significant upfront investment
Alternative recommendation: For custom work, consider advanced TIG welding equipment and welder training instead of automation.
How to get started with cobot TIG welding in 5 steps
- Evaluate your welding volume: Calculate how many identical or similar welds you perform monthly. Cobots need consistent work to justify costs.
- Choose the right system: Match payload capacity to your largest parts. Most TIG applications work with 10–18 kg capacity cobots like RO1.
- Plan your workspace: Cobots need clear access around parts. Measure reach requirements and make sure you have adequate ventilation for TIG processes.
- Start with simple parts: Program basic straight-line welds first, then advance to complex geometries as your team gains experience.
- Train operators gradually: Focus on programming and quality control rather than welding technique. Most operators master cobot basics within 2–3 weeks.
Pro tip: Run side-by-side comparisons between cobot and manual welds on the same parts to validate quality before full production.
Best practices that separate success from expensive mistakes
Proper setup determines 80% of your success with automated welding systems. These practices separate successful implementations from expensive mistakes.
- Consistent part fixturing: Use precision jigs for identical part positioning for every weld cycle
- Regular torch maintenance: Clean tungsten electrodes and check gas flow daily to prevent arc instability
- Backup programming: Save multiple versions of successful weld programs before making modifications
- Material preparation: Clean base metals thoroughly, since cobots can't compensate for contamination like skilled welders
Common mistakes to avoid
- Skipping test welds: Run qualification samples before production, even on “identical” parts
- Ignoring environmental factors: Temperature and humidity changes affect arc characteristics more than manual welding
- Overcomplicating initial programs: Start with basic parameters and optimize gradually rather than trying to perfect everything immediately
- Poor torch alignment: If the torch is off even a little, welds can turn into a mess of missed spots and uneven joints
- Neglecting maintenance schedules: Check alignment, calibrate sensors, and replace worn parts regularly; a little upkeep saves a lot of downtime
For more automation guidance, check out our complete guide to cobot welding.
Market reality check: What cobot TIG welding costs in 2025
The market is heating up. The global robotic welding market is projected to grow from $5.80 billion in 2021 to $9.76 billion in 2028 at a CAGR of 7.7%.
Cobot TIG welding system costs range from $37,000 for basic setups like RO1 to $150,000+ for high-end industrial systems. Most manufacturers see ROI within 12–24 months through improved quality and reduced labor costs.
Budget breakdown for a typical setup:
- Entry-level cobot system: $37,000 – $50,000
- Mid-range systems: $50,000 – $75,000
- High-end industrial systems: $75,000 – $150,000+
Hidden costs to consider:
- Training and setup: $5,000 – $15,000
- Fixtures and tooling: $3,000 – $10,000
- Annual maintenance: 10–15% of purchase price
Used welding cobots typically cost 30–50% less than new models, but make sure you check operating hours and maintenance history.
My verdict on cobot TIG welding
Cobot TIG welding delivers on its promises for the right applications. Industry data shows it's a solid investment for manufacturers with repetitive, high-quality welding requirements who want to reduce dependency on skilled labor.
The technology works best when you have consistent part geometries and production volumes that justify the overhead. Quality improvements alone often pay for the system within 18 months through reduced scrap and rework costs.
Consider alternatives if your work involves complex custom fabrication where human adaptability outweighs robotic consistency. Traditional TIG equipment upgrades might deliver better ROI for job shops handling diverse, one-off projects.
My recommendation
Implement cobot TIG welding for production runs of 50+ identical parts, but maintain manual capabilities for custom work and complex repairs.
Next steps with Standard Bots
RO1 by Standard Bots is more than a robotic arm; it’s the six-axis cobot welding upgrade your factory needs to automate smarter.
- Affordable automation for any size shop: High-end robotic welding at half the price of competing systems; RO1 is available for $37K (list).
- Precision that never slips: Repeatability of ±0.025 mm means flawless welds, whether you’re running high-volume production or tackling delicate projects.
- AI that keeps learning: RO1’s AI on par with GPT-4 learns on the job, and its no-code framework means you can easily redeploy it for new jobs, even if they’re not welding-related, like CNC machine tending, palletizing, pick-and-place, painting, you name it.
- Built-in safety for human-machine collaboration: Advanced machine vision and collision detection mean RO1 works safely alongside human welders without compromising safety.
Book your risk-free, 30-day onsite trial today and see how RO1 can take your welding operation to the next level.
FAQs
1. What is the best cobot for TIG welding applications?
RO1 by Standard Bots is the best cobot for TIG welding in 2025. It combines precision (±0.025 mm repeatability), adequate payload (18 kg), and affordable pricing ($37K list) with no-code programming that doesn't require robotics expertise.
2. How much does a cobot TIG welding system cost?
Cobot TIG welding system costs range from $37,000 to $150,000+ for high-end industrial systems. Most manufacturers see ROI within 12 to 24 months through improved quality and reduced labor costs.
3. Can cobots handle all TIG welding positions?
Yes, cobots can handle all TIG welding positions, including overhead and vertical orientations that are challenging for human welders. Their consistent torch control and lack of fatigue make difficult positions routine.
4. Do I need programming experience to operate a cobot TIG welder?
No, you do not need programming experience to operate a cobot TIG welder. Modern systems use no-code interfaces that allow operators to create weld paths by physically guiding the robot or using simple drag-and-drop controls.
5. What's the difference between cobot TIG welding and robotic TIG welding?
Cobots are designed to work with humans, so they're safer, easier to program, and usually cheaper. In contrast, traditional or industrial robotic welding machines are bigger, faster, and locked into fenced-off zones. They are not designed to work alongside humans. Cobots are also more flexible and easier to reprogram for different parts.
Join thousands of creators
receiving our weekly articles.