FANUC cobot showdown in 2025 comes down to two main lines: CRX and CR.
Both are among the most trusted collaborative robots, but they serve different purposes. CRX cobots are lightweight, portable, and easy to program, whereas CR models deliver heavy-duty payloads and industrial-grade performance.
With global cobot adoption expanding rapidly, the cobot market is projected to reach $12.71 billion by 2030. Many manufacturers are weighing which cobots offer the best return on investment for tasks like welding, machine tending, and packaging. Standard Bot’s RO1 could always be the perfect fit, but let’s compare FANUC’s offering.
FANUC cobot showdown: TL;DR
What is a FANUC cobot?
A FANUC cobot is a collaborative robot built to work safely alongside humans in manufacturing and industrial environments. Unlike traditional industrial robots, these machines operate without extensive safety guarding, stop on contact, and are easily programmable or reprogrammable.
FANUC cobots combine precise motion control with built-in safety features, including force-limiting sensors, collision detection, and smooth arm designs, to reduce risk during human-robot interaction.
FANUC offers two main lines:
- CR series: Heavy-duty models with payloads up to 35 kg, ideal for welding, palletizing, and demanding material handling
- CRX series: Lightweight, portable models that are quick to set up, making them a fit for small shops and flexible tasks
Both lines use FANUC’s intuitive programming environment with drag-and-drop teach modes and integrate with standard tooling and vision systems. Many models also feature plug-and-play compatibility, helping reduce integration time.
FANUC CRX series overview
The FANUC CRX series is a lightweight and portable collaborative robot line built for fast deployment and simple programming. You can set up a CRX without advanced coding skills and maintain it with minimal downtime.
Their sealed, streamlined arms make them suitable for a wide range of environments, including workshops, production lines, and inspection stations.
Here are three key CRX models:
FANUC CRX-5iA
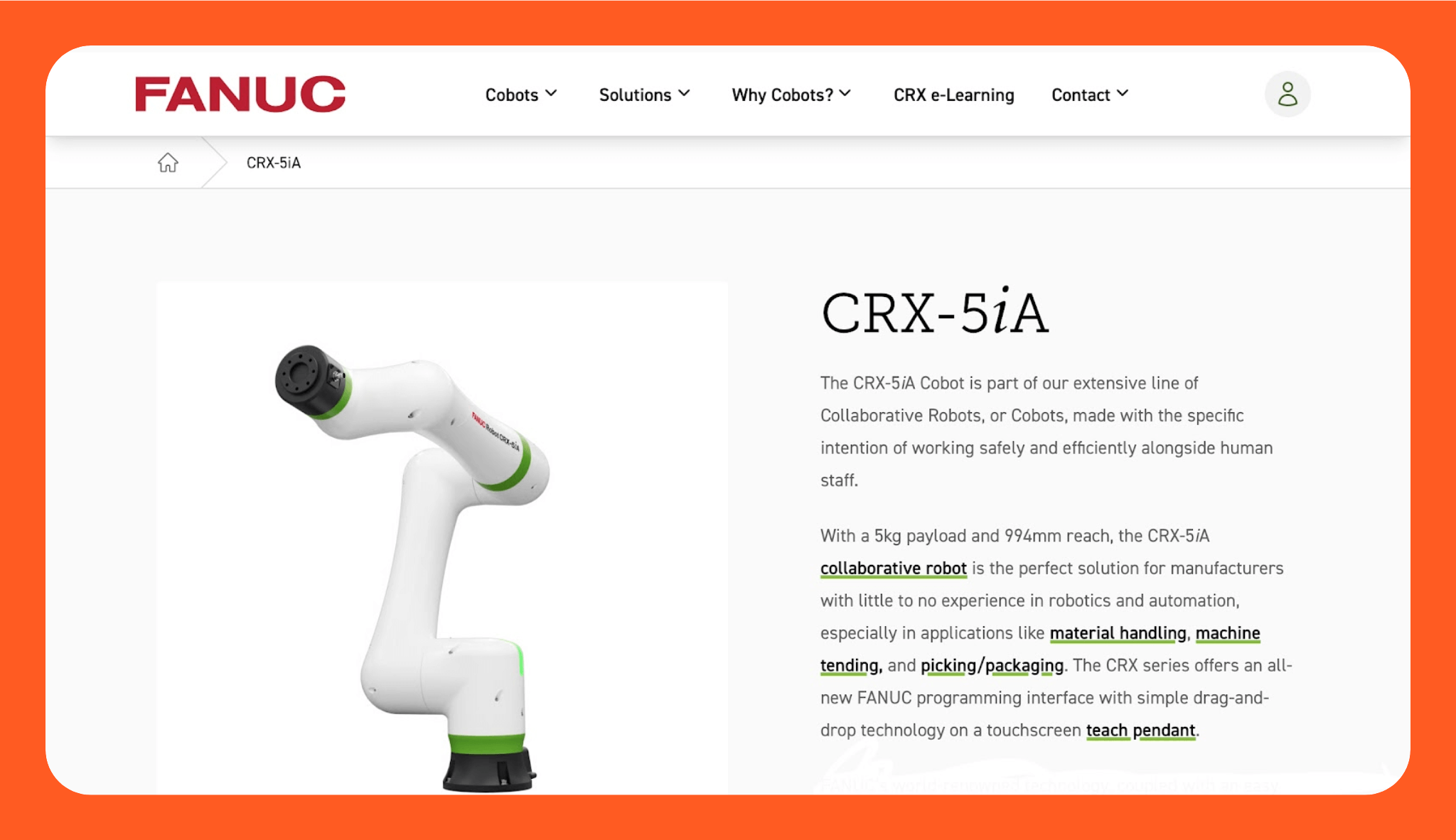
With a 5 kg payload and 994 mm reach, the CRX-5iA is designed for light-to-medium-duty tasks where reach and precision are equally important. It’s ideal for CNC machine tending, pick-and-place, light assembly, and inspection work.
The compact arm design allows it to operate close to machinery, and its tablet-style teach pendant makes programming accessible even to first-time users. Its flexibility means it can be redeployed across different stations without lengthy reprogramming, keeping downtime minimal.
FANUC CRX-10iA/L

The CRX-10iA/L offers a 10 kg payload and an extended 1,418 mm reach, making it suitable for applications where the cobot must work over larger fixtures, handle wider conveyors, or serve multiple machines from one position.
This model works well for packaging, palletizing lighter loads, and material handling in medium-sized work envelopes. The “L” variant’s longer reach reduces the need for repositioning, and it retains the same ease-of-use and low-maintenance benefits as the rest of the CRX family.
FANUC CRX-30iA
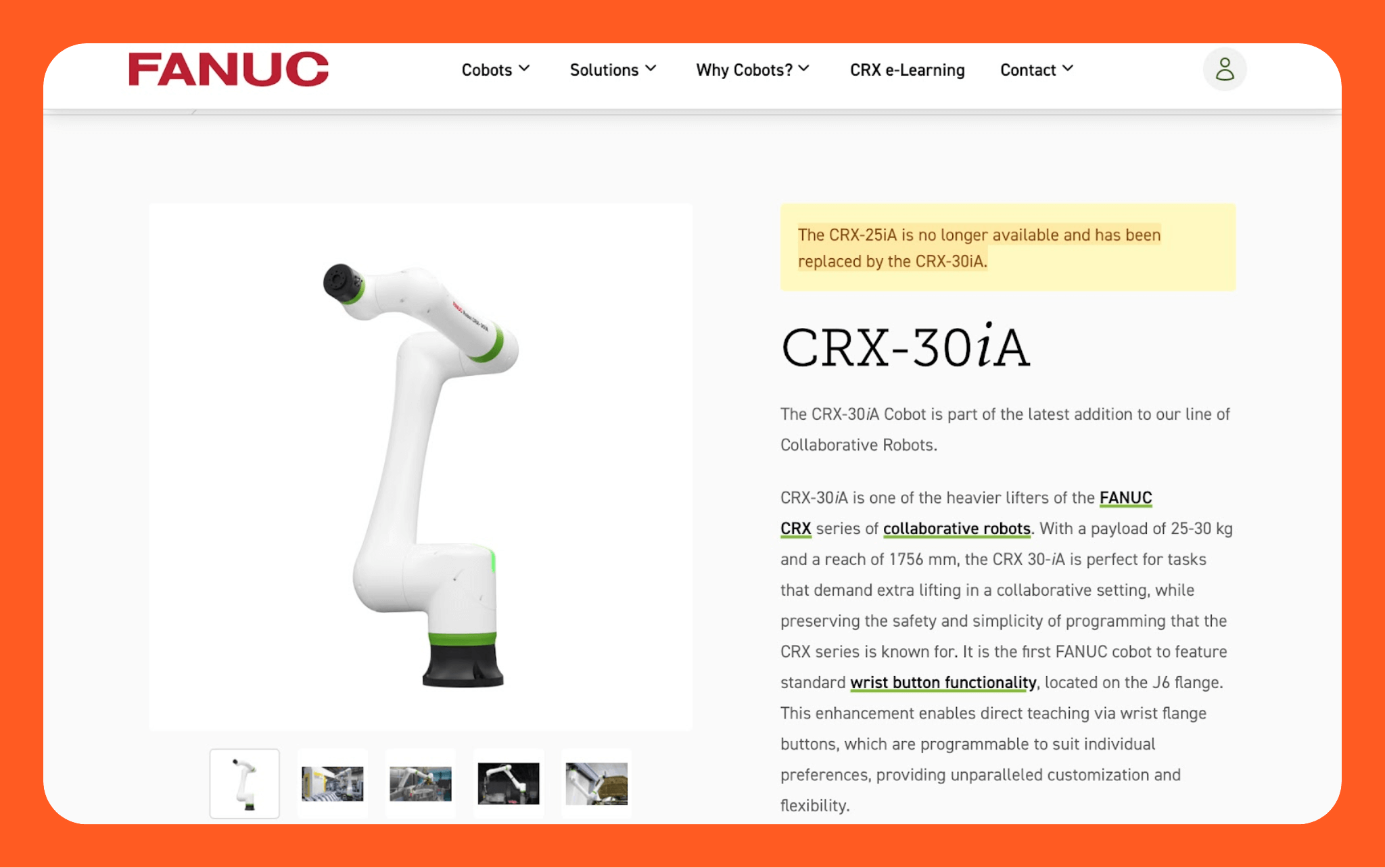
The CRX-30iA is the most powerful cobot in the CRX lineup, offering a 30 kg payload and a 1756 mm reach. It’s built for heavy-duty collaborative applications such as palletizing, bulk packaging, and moving large or awkward components in shared workspaces.
Despite its high capacity, it retains the CRX family’s easy drag-and-drop programming, smooth motion for safe human interaction, and long maintenance intervals. This model is ideal for facilities that need industrial-level lifting power without sacrificing collaborative flexibility.
Also consider the CRX‑25iA for packaging and palletizing; its 25 kg payload and 1889 mm reach bridge the gap between light assembly and heavier handling.
Advantages:
- Portability for quick redeployment across workstations.
- Flexible integration with grippers, vision systems, and third-party software.
- Simple programming through drag-and-drop interfaces and tablet controls.
- Low maintenance requirements, with intervals up to eight years before first lubrication in some models.
Applications: Machine tending, light assembly, packaging, inspection, and general pick-and-place in mixed production settings.
FANUC CR series overview
The FANUC CR series overview shows a lineup built for heavy-duty collaborative applications that require higher payloads and industrial-grade durability. These cobots use reinforced frames and handle up to 35 kg, making them ideal for palletizing, welding, and heavy material handling.
Compared to the lighter CRX line, CR models are engineered for tough, continuous operations in demanding industrial environments.
Here are three notable CR models:
CR-4iA
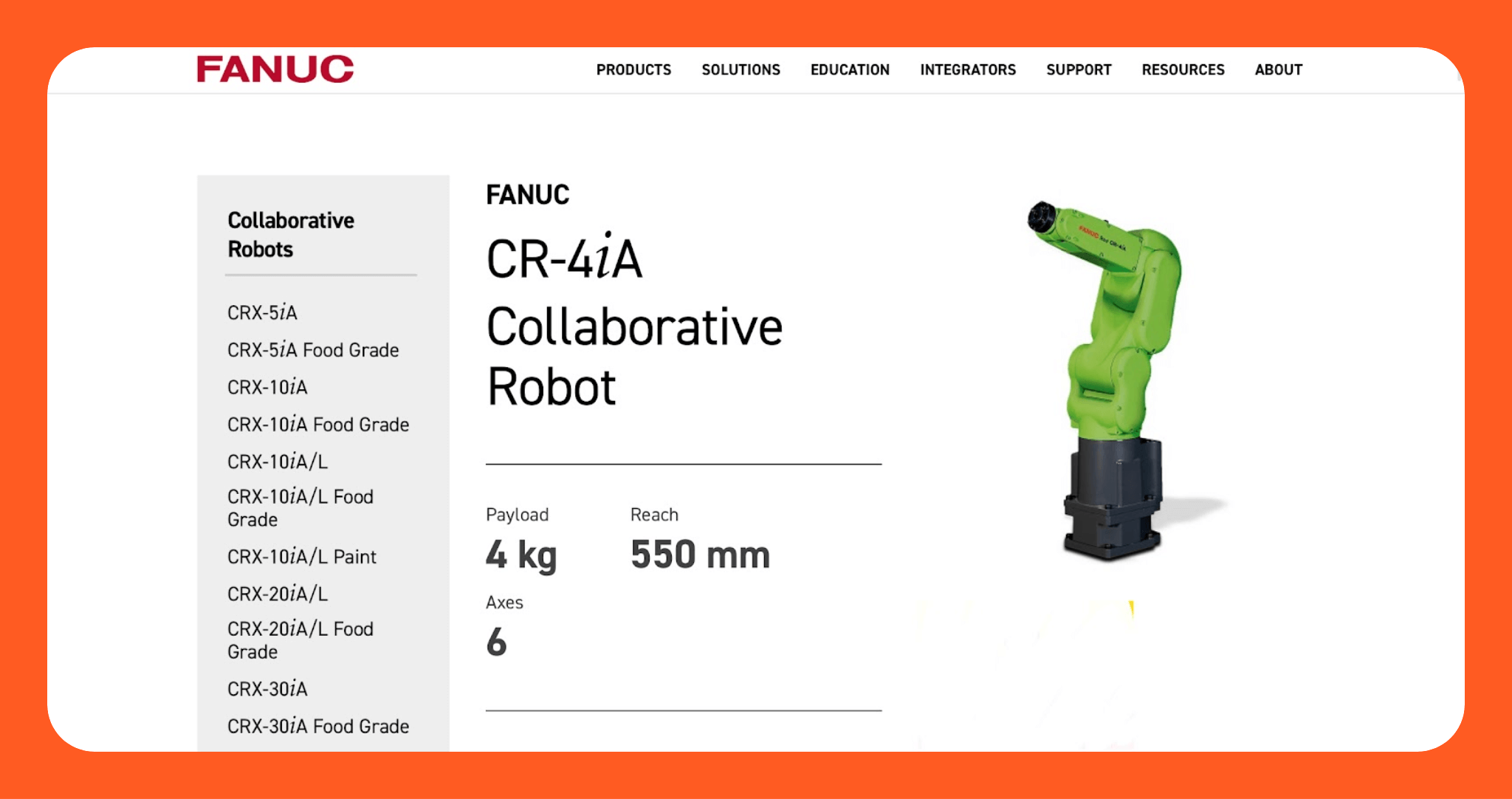
A 4 kg payload cobot with a 550 mm reach, the CR-4iA is the compact, heavy-duty option in the CR series. It’s built with the same strong arm structure as FANUC’s industrial robots, allowing it to run continuously in demanding environments.
Common uses include high-precision assembly, inspection, and delicate machine tending in industries like electronics and medical devices.
FANUC CR-7iA/L
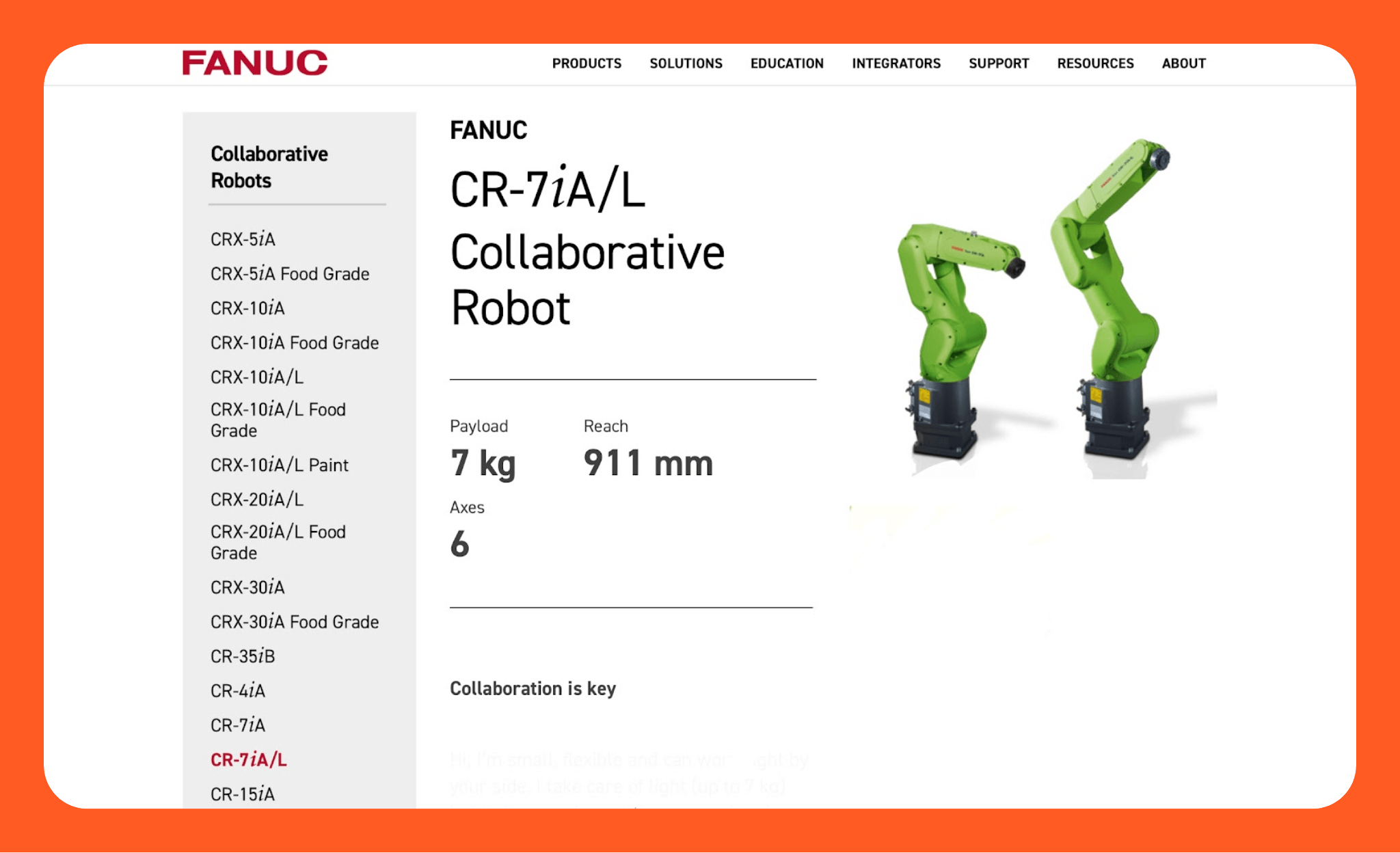
The CR-7iA/L is a versatile collaborative robot with a 7 kg payload and an extended reach of around 911 mm, making it ideal for tasks that require both precision and range. It’s well-suited for assembly work, inspection processes, and handling medium-sized components in industries like electronics, automotive, and consumer goods.
Its extended reach allows it to work over larger fixtures or service multiple stations without relocation, while maintaining FANUC’s built-in safety features for close human interaction.
FANUC CR-15iA

The CR-15iA offers a 15 kg payload and approximately 1441 mm reach, striking a balance between strength and coverage. It’s designed for heavier collaborative jobs such as palletizing, packaging, and machine tending for larger parts.
The higher payload capacity supports bulkier end-of-arm tooling or multi-pick grippers, while its collaborative design allows safe operation alongside people in shared workspaces. Its strong build makes it a strong choice for medium-to-high throughput applications that still require flexibility.
Advantages:
- Proven performance in integration with assisted‑lift workflows.
- Built for industrial reliability in high-volume, multi-shift operations.
- Compatible with advanced tooling, welding torches, and custom end effectors.
- Capable of handling loads beyond the limits of most cobots, including 20 kg and 25 kg payload cobot applications.
Applications: Heavy material handling, collaborative welding, high-volume palletizing, and other scenarios where strength and precision must work alongside human operators.
Specs and feature comparison table
This table compares payload, reach, repeatability, best-fit applications, and estimated 2025 price ranges for key CRX and CR series models.
Pricing is based on dealer listings and market estimates, as FANUC does not publish official prices.
FANUC cobots in action: Key applications
FANUC cobots in action cover applications from precision manufacturing to high-volume logistics. Their flexibility, safety features, and ease of integration make them suitable for tasks ranging from small-part handling to heavy-load palletizing.
Below are some of the most common and high-value applications in 2025:
Machine tending
CRX series cobots excel in repetitive, light-payload CNC machine tending. Their compact footprint and portability allow quick redeployment between machines, making them ideal for job shops and high-mix, low-volume manufacturing.
Operators can program them using FANUC’s tablet-style teach pendant, which supports drag-and-drop commands, reducing setup time from hours to minutes. Typical integrations include 2- or 3-finger grippers, vacuum end effectors, and vision cameras for part orientation checks.
This makes them a strong fit for tasks such as loading raw parts into CNC lathes, unloading finished components, and performing visual quality inspections.
Welding
For heavy-duty welding applications, the CR series offers the payload and rigidity required for consistent, high-quality welds. Models like the CR-14iA/L can mount larger welding torches, wire feeders, and protective shrouds without compromising reach or stability.
They integrate smoothly with leading welding systems from Lincoln Electric and Fronius, supporting MIG, TIG, and arc welding processes. These cobots can operate continuously across multiple shifts, improving arc-on time and reducing rework rates.
Their collaborative safety features mean they can work alongside human operators on shared fixtures, enabling hybrid welding setups that combine automation with skilled craftsmanship.
Packaging and palletizing
FANUC’s 20 kg and 25 kg payload cobots, such as the CRX-25iA, bring the reach and lifting capacity needed for mixed SKU packaging and palletizing. They use vision-guided systems to identify package sizes, scan barcodes, and place items precisely, even when loads vary in shape and weight.
For heavier items, the CR-35iA offers a 35 kg payload, enabling bulk material palletizing in industries like beverages, building materials, and automotive components.
These cobots can stack loads directly onto pallets on the floor or conveyors, reducing strain-related injuries for workers and increasing throughput in busy distribution centers.
Cost and ROI considerations
Cost and ROI considerations for FANUC cobots in 2025 vary by model and setup. CRX series units generally range from $25,000 to $75,000, whereas CR series models start around $80,000 and can exceed $120,000. These are estimates from industry sources, as FANUC does not publish official pricing.
When budgeting, factor in tooling, integration, and software licensing, which can add $5,000 to $20,000 depending on your application. For example, a CRX-25iA with a palletizing gripper and vision system will cost more than a base unit used for light assembly.
ROI timelines typically range from 12 to 30 months (depending on usage), driven by labor savings, increased uptime, and reduced injury risks. Leasing options are available through FANUC distributors, with monthly payments varying by model and contract length.
This makes high-payload models like the CR-35iA more accessible for facilities that need capacity without a full upfront investment.
Final words: Which FANUC cobot is right for you?
Deciding which FANUC cobot is right for you depends on payload capacity, workspace size, application type, and budget. CRX series models work best for first-time cobot users or shops needing flexibility for light-to-medium tasks. CR series models are built for heavy-duty jobs, larger payloads, and demanding tools.
If your goal is fast deployment with lower upfront cost, a budget-friendly cobot from the CRX lineup may be your best fit. For maximum strength and long-term durability in tough environments, invest in a CR series model. Or, you could try Standard Bots.
Next steps with Standard Bots’ robotic solutions
Looking to upgrade your automation game? Standard Bots’ RO1 is the perfect six-axis cobot addition for any CNC or production setup, delivering unbeatable precision and flexibility.
- Affordable and adaptable: RO1 costs $37K (list price). Get high-precision automation at half the cost of traditional robots.
- Precision and power: With a repeatability of ±0.025 mm and an 18 kg payload, RO1 handles even the most demanding jobs.
- AI-driven simplicity: Equipped with AI capabilities on par with GPT-4, RO1 integrates smoothly with your workflow for advanced automation.
- Safety-first design: Machine vision and collision detection mean RO1 works safely alongside human operators.
Schedule your on-site demo with our engineers today and see how RO1 can bring AI-powered greatness to your shop floor.
FAQs
1. How much does a used FANUC CRX cobot typically cost in 2025?
A used FANUC CRX cobot in 2025 generally costs between $20,000 and $45,000, depending on the specific model, age, operating hours, and overall condition. Units that have been factory-refurbished or include accessories like grippers, vision systems, or custom mounts may be priced at the higher end of that range.
2. Can I lease a FANUC cobot, and what are the average monthly payments?
You can lease a FANUC cobot through authorized distributors and financing partners. Average monthly payments range from $600 to $2,500, depending on the model, lease term, and any additional tooling or integration services included in the agreement. Leasing can be a cost-effective way to deploy automation without the full upfront investment.
3. What training or certification is required to program a FANUC CRX model?
Programming a FANUC CRX model does not require formal certification. FANUC provides optional training through online modules, in-person classes, and on-site sessions. Most operators can learn the tablet-based teach pendant interface in less than a day, especially for basic pick-and-place or tending tasks.
More advanced applications like vision integration or custom I/O programming may require additional training time.
4. Which FANUC cobot model is best suited for welding stainless steel?
The FANUC CR-14iA/L is a common choice for stainless steel welding. Its 14 kg payload and 911 mm reach support heavier torches and larger fixtures. The model is compatible with popular welding systems from Lincoln Electric and Fronius for MIG, TIG, and arc welding processes.
5. How often do FANUC cobots need preventive maintenance, and what parts wear out first?
FANUC cobots typically require major preventive maintenance, such as lubrication of joints every 8 years under normal operating conditions.
Common wear parts over the cobot’s lifespan include seals, gaskets, protective covers, and cable assemblies. In high-duty-cycle environments, periodic inspection of wiring harnesses and connector joints is also recommended.
6. Do FANUC cobots come with plug-and-play cabling, or do I need a custom integration kit?
Most FANUC cobots come with plug-and-play cabling for standard tooling, making it possible to connect and operate basic grippers or vacuum tools immediately. However, specialized applications such as those requiring multiple tool changers, additional sensors, or unique end-of-arm tooling may require a custom integration kit.
7. What safety certifications and compliance standards do FANUC collaborative robots meet?
FANUC collaborative robots meet ISO 10218-1 and ISO/TS 15066 safety standards for industrial and collaborative robot operation. They also carry certifications such as CE for European markets and UL for North America. Additional regional or industry-specific certifications may be available depending on where the robot is deployed.
Join thousands of creators
receiving our weekly articles.