A case packing robot automates the placement of products into shipping cases, boxes, and containers with precision and speed that manual labor simply cannot match. Manual case packing is like trying to keep up with a Formula 1 race on a bicycle. The pandemic-driven e-commerce boom created massive demand for automated packing solutions that human hands alone cannot satisfy.
This complete guide covers everything you need to choose the right case packing robot for your operation, including types, costs, and top manufacturers.
What are case packing robots?
Case packing robots are automated systems that place products into shipping cases, display boxes, and containers. They handle everything from delicate electronics to heavy automotive parts, stacking items in precise patterns that maximize space and minimize damage.
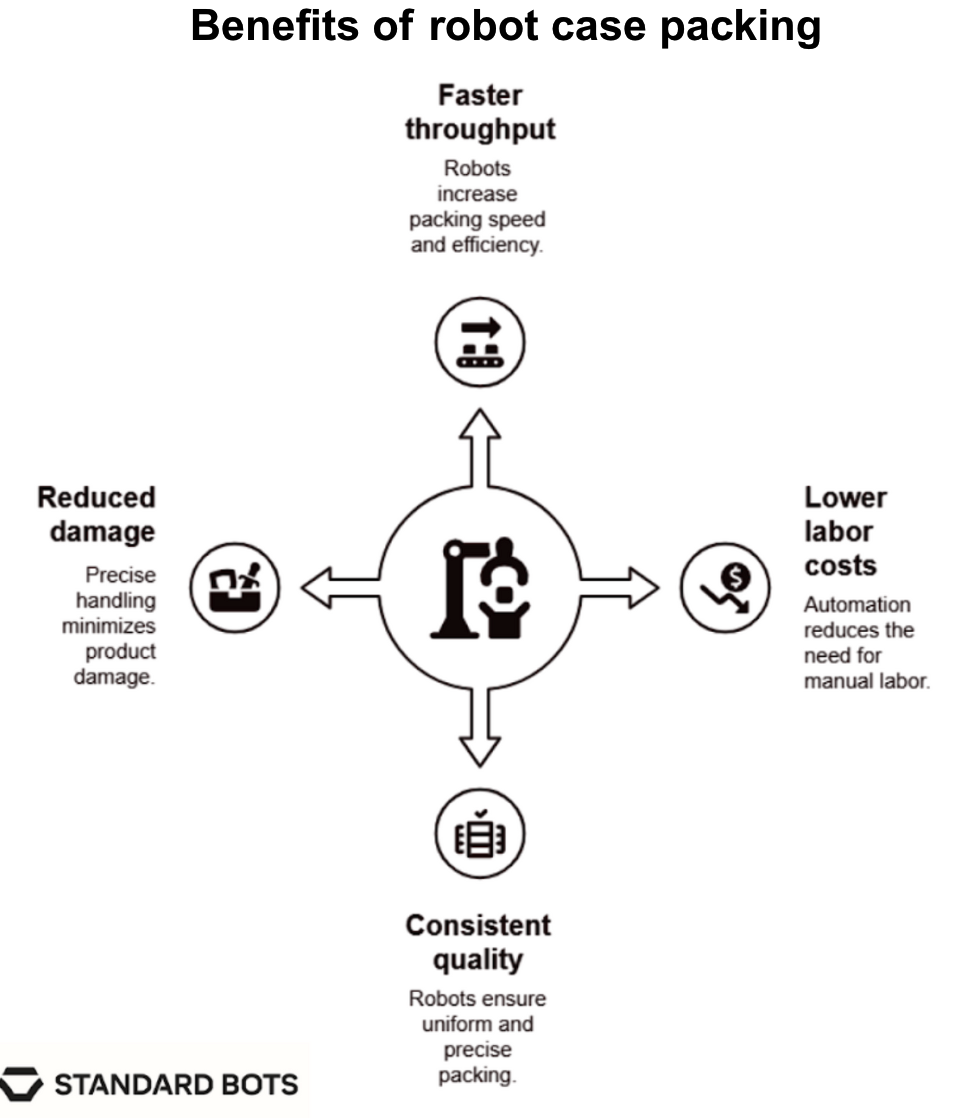
Modern robotic case packing systems combine articulated arms, specialized grippers, and vision systems to identify products, calculate optimal placement, and execute consistent packing patterns. Unlike human workers, they don't get tired, make fewer mistakes, and work 24/7 without breaks.
According to the Association for Advancing Automation, robot orders in North America grew 14.1% in Q3 2024, with non-automotive industries driving demand for packaging automation.
Automation results in faster throughput, lower labor costs, and consistent packing quality that reduces damage claims and customer complaints.
Types of case packing robots
The main types of case packing robots are SCARA, Cartesian, gantry, and articulated robots.
Your case packing robot choice depends on your products, space, and speed requirements. Here's what actually works in real-world automated packing scenarios.
1. Cartesian/Gantry robots
Gantry robots operate on overhead tracks with linear X, Y, and Z movements. They're the workhorses of heavy-duty case packing operations.
- Best for: Large products, heavy cases, high-volume operations
- Payload: Up to 100 kg+
- Speed: Moderate to high
- Footprint: Large (requires ceiling mounting)
Gantry robots excel at lifting heavy items and maintaining precise positioning for high-volume case packing operations. However, their rigid construction limits flexibility. If your automated packing requires intricate patterns like nesting or interlocking items, gantries struggle with these complex movements.
2. Articulated robots
Articulated robots mimic human arm movements with 5–6 joints. They're the Swiss Army knives of case packing, versatile, precise, and adaptable.
- Best for: Mixed products, delicate items, complex packing patterns
- Payload: 5–25 kg (varies by model)
- Speed: Moderate
- Footprint: Compact
These robots handle fragile items with human-like dexterity while reaching tight spaces and navigating obstacles. Articulated robots adapt their arm configurations to access challenging areas within cases, ensuring complete and precise automated packing.
3. SCARA robots
SCARA (Selective Compliance Assembly/Articulated Robot Arm) robots specialize in fast, precise horizontal movements. They sacrifice some flexibility for speed and accuracy.
- Best for: High-speed operations, uniform products, simple packing patterns
- Payload: 3–20 kg
- Speed: Very high
- Footprint: Compact
SCARA robots move faster than six-axis robots because fewer joints mean less complex calculations. Their controlled movements prevent unwanted tilting or product rotation during case packing operations.
Fixed vs. mobile case packing robots
Your facility layout and workflow determine whether you need stationary or mobile robots for your automated packing system.
1. Fixed robots
Fixed robots stay in one location while products come to them via conveyor systems.
Advantages:
- Higher speeds and payload capacity
- Easier conveyor integration
- Lower cost
- More stable operation
Disadvantages:
- Require product transport infrastructure
- Less flexible for layout changes
- Single-point-of-failure risk
2. Mobile robots
Mobile robots travel to packing locations using wheels, tracks, or other locomotion systems.
Advantages:
- Pack at multiple locations
- Easy relocation as needs change
- Compact footprint
- Flexible deployment
Disadvantages:
- Slower speeds and lower payloads
- Higher cost
- Limited conveyor integration
- Navigation complexity
Pro tip: Many factories use hybrid approaches with fixed robots for high-volume case packing, mobile robots for smaller batches, and specialty items. This strategy maximizes both throughput and flexibility in automated packing operations.
How to choose a case packing robot
Selecting the right automated packing system requires evaluating multiple factors beyond just price and speed.
1. Production volume and speed requirements
Match robot speed to your actual throughput needs, not theoretical maximums.
Ask yourself:
- What's your current daily/hourly packing target?
- How does volume vary during peak seasons?
- Do you need 24/7 operation capability?
- Are you planning production increases?
Example: If you're packing 1,000 units per hour during peak times, choose a case packing robot that comfortably handles 1,200+ units to account for maintenance downtime and efficiency variations.
2. Product variety and packaging complexity
Different products require different handling approaches.
- For uniform products (same size, shape, weight): SCARA or simple articulated robots work well
- For mixed products (varying dimensions, fragility): Articulated robots with adaptive grippers
- For delicate items (electronics, food): Robots with force-sensitive grippers and vision systems
Real example: At Cascina Italia S.p.A., an Italian egg supplier processing over 2.5 million eggs per day, manual case packing was automated using Universal Robots UR5 six-axis arms equipped with vacuum grippers.
These robots pack cases ranging from 96-egg cartons up to 1,400-egg cases, achieving speeds of around 15,000 eggs per hour, dramatically boosting throughput, reducing repetitive labor, and improving consistency and safety
3. Case sizes and types
Ensure your robot can handle your specific packaging requirements.
Consider:
- Case dimensions and weight limits
- Standard vs. custom case sizes
- Sealing and closure mechanisms
- Material types (cardboard, plastic, metal)
Gantry robots handle the largest cases, but may be overkill for small operations. Articulated robots offer more size flexibility but have payload limitations.
4. Integration with existing systems
Seamless integration prevents costly downtime and compatibility issues.
Evaluate:
- Conveyor system compatibility
- Control system interfaces
- Software integration requirements
- Data exchange protocols
Choose robots that communicate with your existing equipment without requiring major infrastructure changes.
5. Ease of use and programming
Your team's technical skills determine how complex a system you can realistically operate.
No-code interfaces let operators create new packing patterns without programming knowledge. Advanced programming offers more customization but requires skilled technicians. Hybrid approaches provide both simple and advanced options
Standard Bots' RO1 uses no-code programming. Operators guide the case packing robot through movements once, and it remembers the pattern for future automated packing cycles.
6. Maintenance and service
Factor in long-term operational costs, not just purchase price.
Consider:
- Maintenance frequency and complexity
- Spare parts availability and cost
- Manufacturer support quality
- Expected downtime for repairs
Robots with predictive maintenance alert you to potential issues before they cause downtime.
7. Cost and ROI calculation
Calculate the total cost of ownership, not just the upfront price.
Upfront costs:
- Case packing robot purchase price: Typically ranges from $25,000 to $200,000+, depending on type, payload, and level of automation. Standard Bots lists its RO1 cobot at $37,000, while RobotWorx estimates $50,000 to $80,000 for new six-axis robots. According to Motion Controls Robotics, a full robotic case packing cell (with conveyors and vision) may cost $150,000–$300,000+.
- Installation and integration: $10,000 to $50,000, depending on your factory layout, conveyor compatibility, and robot model. See how robotic system integration adds to total setup time and cost.
- Training and setup: $5,000 to $15,000, although systems like RO1 reduce training time with a no-code interface and built-in vision.
Ongoing costs:
- Maintenance: $3,000–$10,000 annually
- Spare parts: $1,000–$5,000 annually
- Software updates: $0–$2,000 annually
ROI factors:
- Labor cost savings: 1 to 3 full-time positions per case packing robot
- Productivity increases: 20 to 300% depending on the automated packing application
- Quality improvements: 10 to 50% reduction in damage claims
- Payback period: Typically 12 to 36 months
Top case packing robot manufacturers
In 2023, more than 4.28 million industrial robots were working in factories around the world, an all‑time high and a 10% year-over-year increase, per IFR. Here are the leading manufacturers:
1. Standard Bots (USA)
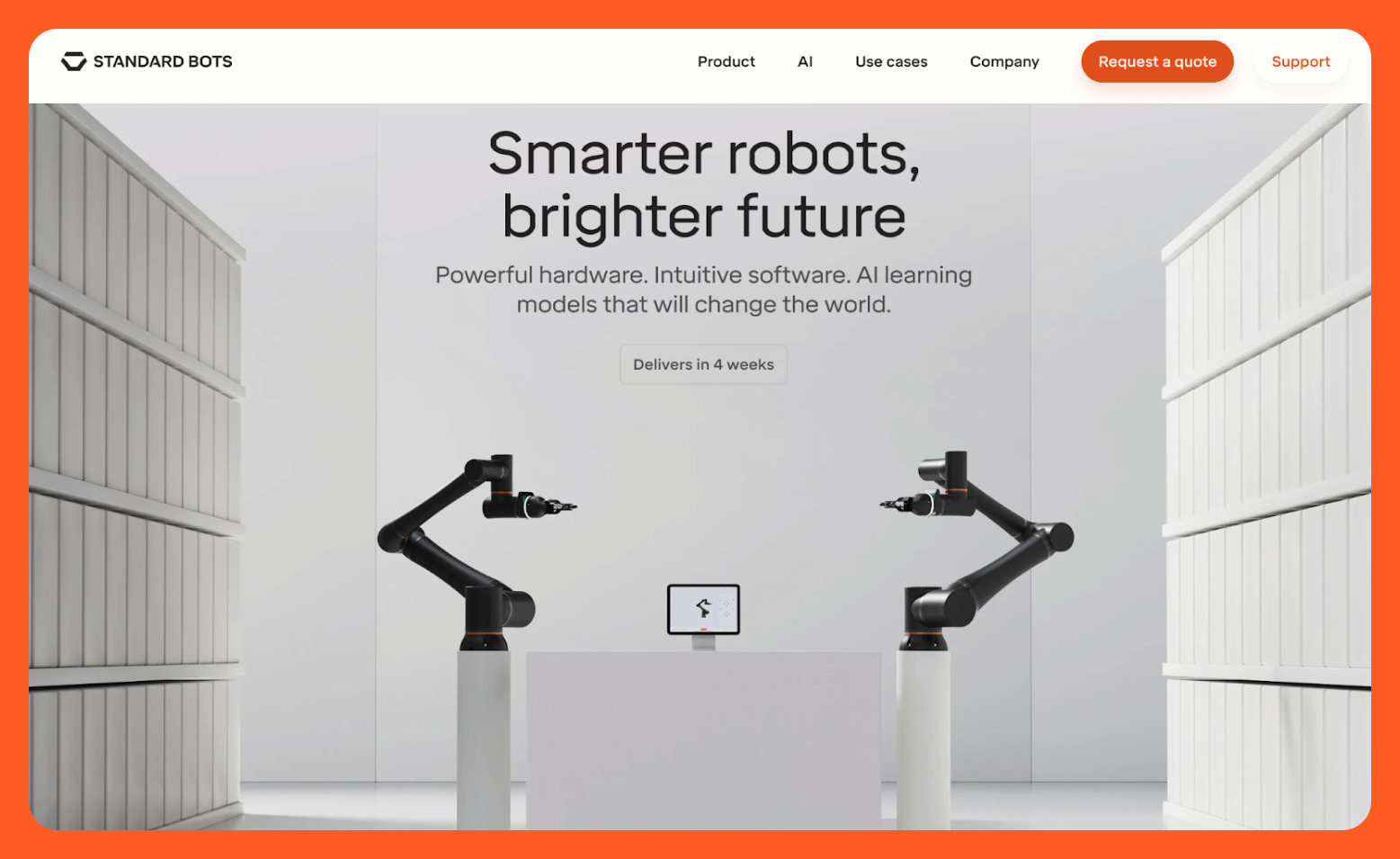
Standard Bots' RO1 combines articulated robot flexibility with SCARA-like speed and precision for superior case packing performance. At $37,000 (list price), it's significantly more affordable than comparable robots while offering superior capabilities.
Key advantages:
- 18 kg payload capacity: Higher than most competitors
- ±0.025 mm repeatability: 2x more accurate than competing models
- Built-in 3D vision: No additional camera systems needed
- No-code programming operators learn in hours, not weeks
- Made in the USA, faster delivery, and support
RO1 handles case packing plus machine tending, pick-and-place, welding, and other applications, maximizing your investment flexibility.
2. ABB Group (Switzerland)
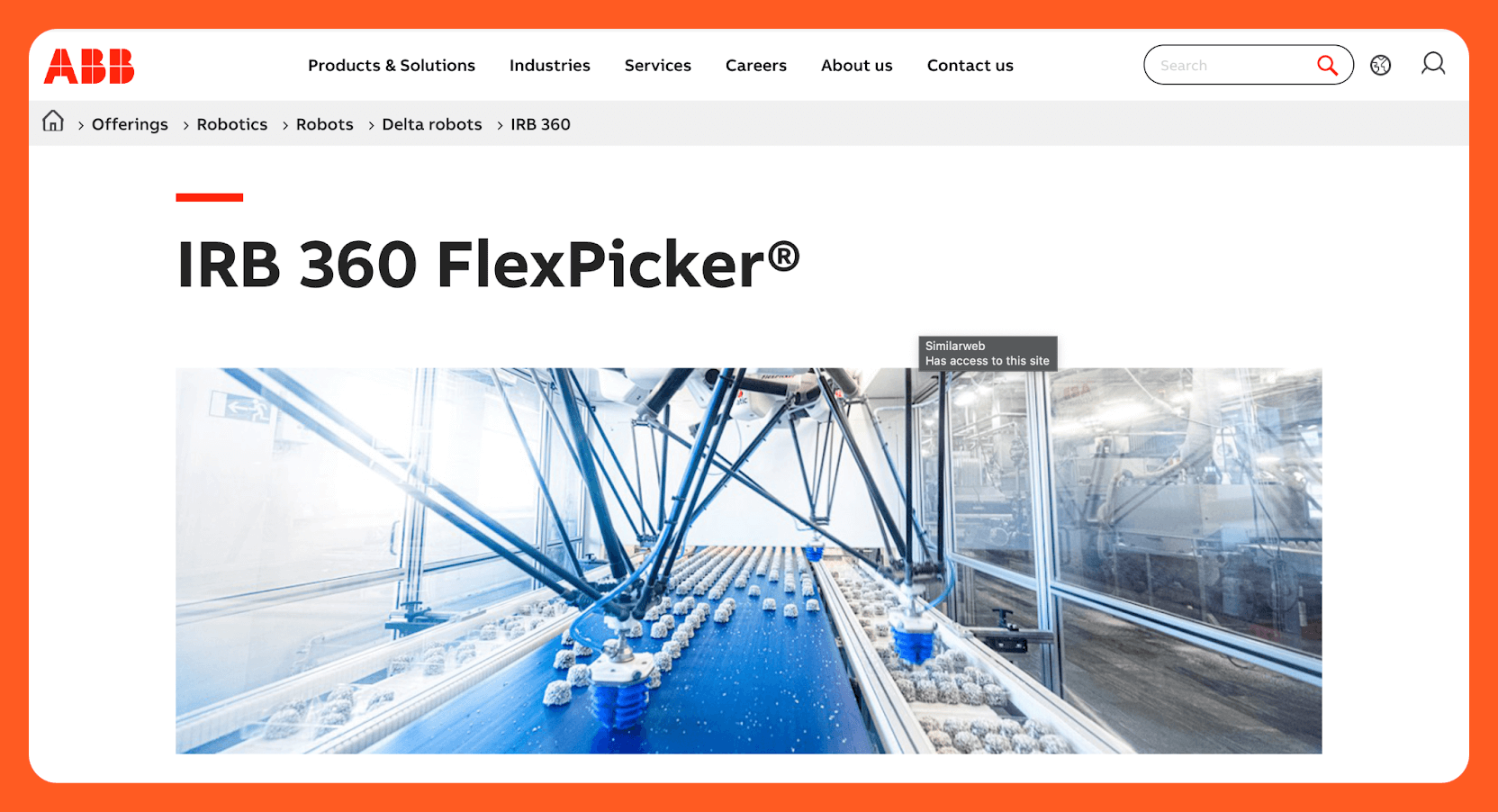
ABB offers comprehensive industrial robots with strong performance in pharmaceuticals, logistics, and consumer goods. Their automated packing systems feature intuitive programming interfaces and advanced vision systems for improved handling and quality control.
- Strengths: Speed, precision, adaptability
- Applications: Pharmaceuticals, logistics, consumer goods
- Price range: $35,000–$150,000+
3. KUKA AG (Germany)
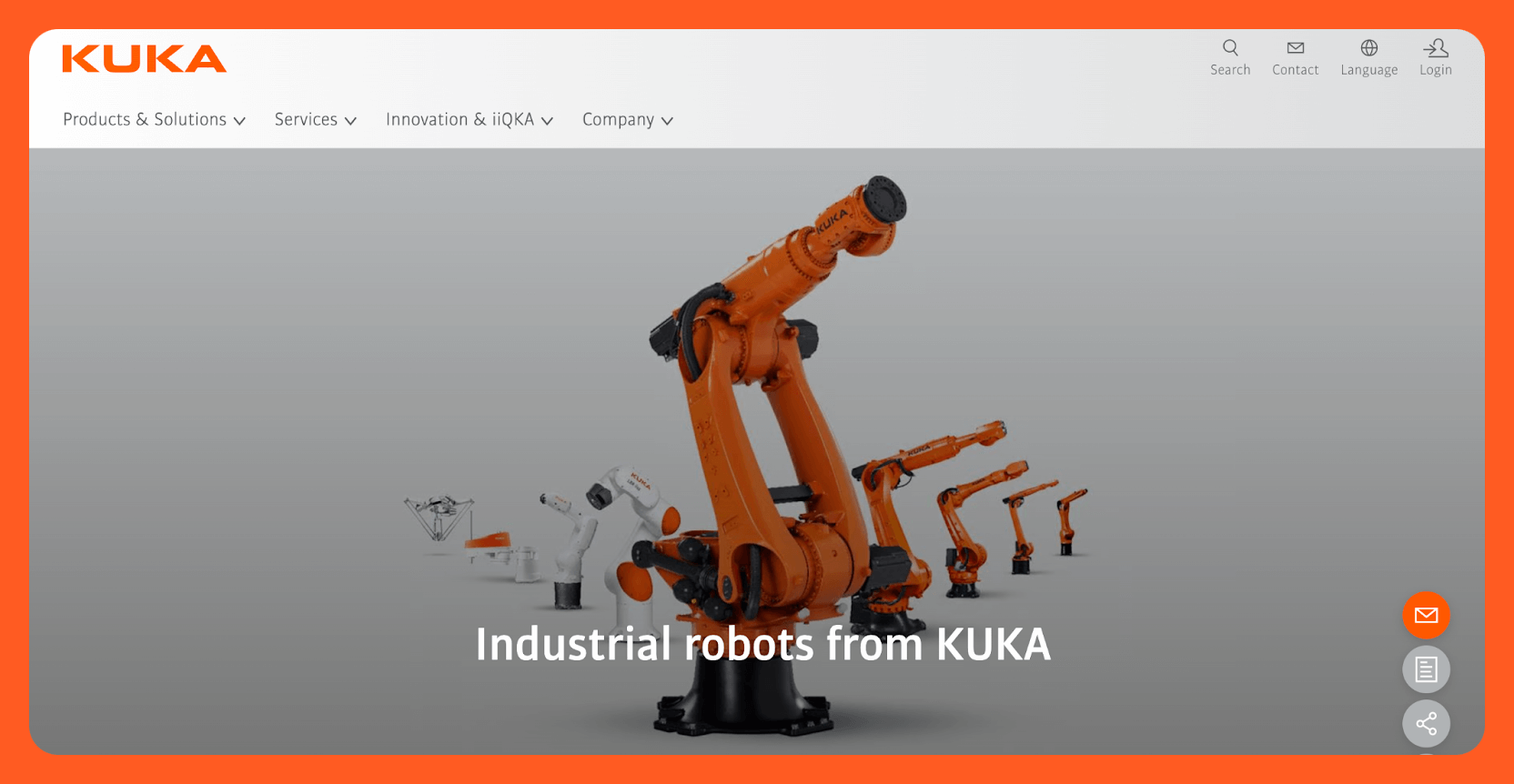
KUKA specializes in robotics and automation solutions across automotive, electronics, and e-commerce sectors. Their case packing robots feature advanced control systems and software for seamless production line integration.
- Strengths: Advanced control systems, integration capabilities
- Applications: Automotive, electronics, e-commerce
- Price range: $30,000–$120,000+
4. FANUC (Japan)
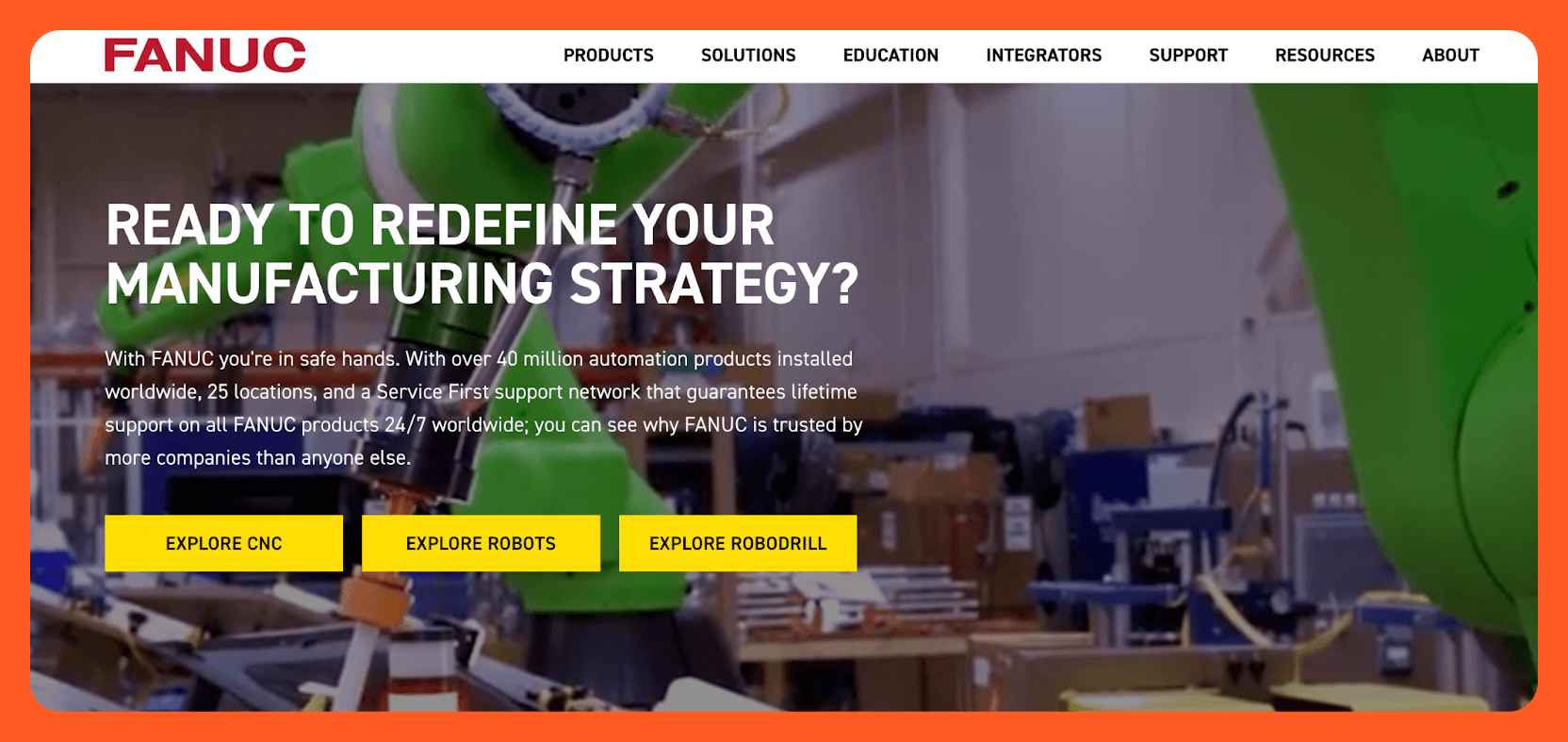
FANUC robots feature user-friendly programming interfaces and robust safety measures. Their case packing systems offer diverse payload capacities and reach to accommodate various automated packing requirements, working with RSC cases and display cases.
- Strengths: User-friendly interfaces, safety features, payload variety
- Applications: General manufacturing, automotive, electronics
- Price range: $30,000-$100,000+
Key takeaways
Case packing robots aren't just nice-to-have anymore. They're essential for staying competitive in today's automated packing landscape. Manual packing can't keep up with modern demand, and the robots that seemed expensive five years ago now pay for themselves in months.
The key is matching robot capabilities to your specific needs: production volume, product variety, case types, and integration requirements. Don't overbuy capabilities you won't use, but don't underbuy and limit your growth potential.
Consider these priorities for your case packing robot selection:
- Production volume ensures the robot can handle your throughput
- Product variety determines flexibility requirements
- Integration ease prevents costly delays and compatibility issues
- Long-term costs include maintenance, support, and expansion capabilities
Standard Bots' RO1 offers the best combination of performance, affordability, and ease of use for most automated packing operations. At half the cost of comparable robots, it delivers superior speed, precision, and flexibility.
Next steps with Standard Bots
Looking to upgrade your automation game? Standard Bots’ RO1 is the perfect six-axis cobot addition to any case packing setup. It delivers unbeatable precision and flexibility to operations of all sizes.
- Affordable and adaptable: RO1 costs $37K (list). Get high-precision automation at half the cost of traditional robots. Available at half the cost of comparable robots, or lease it starting at $5/hour.
- Precision and power: With a repeatability of ±0.025 mm and an 18 kg payload, RO1 handles even the most demanding CNC jobs.
- AI-driven simplicity: Equipped with AI capabilities on par with GPT-4, RO1 integrates seamlessly with CNC systems for advanced automation.
- Safety-first design: Machine vision and collision detection mean RO1 works safely alongside human operators.
Schedule your on-site demo with our engineers today and see how RO1 can bring AI-powered greatness to your shop floor.
FAQs
1. What's the best case packing robot for 2025?
RO1 by Standard Bots is the best case packing robot for 2025. It combines superior performance, affordability, and ease of use. At $37,000 (list price), it's half the cost of comparable robots while delivering higher payload capacity and better precision.
2. How much do case packing robots cost?
Case packing robots’ costs range from $25,000 to $200,000+, depending on capabilities. RO1 costs $37,000 (list price) and includes features that competitors charge extra for, like built-in vision and no-code programming.
3. Can case packing robots handle fragile products?
Yes, with proper end effectors and force control. Robots with vacuum grippers, force-sensitive sensors, and vision systems handle delicate items better than manual workers. RO1's ±0.025 mm repeatability ensures consistent, gentle handling.
4. How long does it take to install a case packing robot?
Installation time for case packing robots varies from days to weeks, depending on complexity. RO1 typically installs in 1–3 days thanks to its portable base and plug-and-play design. No concrete mounting or extensive programming required.
5. What's the ROI for case packing robots?
In most cases, packing robots pay for themselves in 18–36 months through labor savings, productivity increases, and quality improvements. RO1's lower cost and higher performance often deliver ROI in under 18 months.
Join thousands of creators
receiving our weekly articles.