Robotic arc welding helps manufacturers reduce errors and save on labor, without adding extra shifts. In 2025, it’s a practical, affordable solution for shops that need precision and consistency.
Manufacturers that use arc welding robots see real improvements in how fast they can produce parts, with many reporting substantial productivity gains that can effectively double output and far fewer defects.
These manufacturers also note that robotic systems help them win contracts for precision work and bigger projects they couldn't handle before.
What is robotic arc welding?
Robotic arc welding is an automated welding process where a robot, controlled by pre-programmed instructions, performs arc welding tasks. This process uses an electrical arc to melt metal and fuse workpieces together, with the robot precisely positioning the welding torch along a predefined path.
Depending on the setup, robotic arc welding can include MIG (Metal Inert Gas) and TIG (Tungsten Inert Gas) processes. MIG is more common for high-speed, high-volume jobs, whereas TIG is used where applications need finer control and cleaner welds.
Both methods benefit from automation, especially when consistent quality and output are critical.
Manufacturers implementing robotic arc welding frequently see significant reductions in cycle time and at least 50% fewer defects. This directly leads to higher profit margins and fewer customer complaints.
Key advantages of robotic arc welding
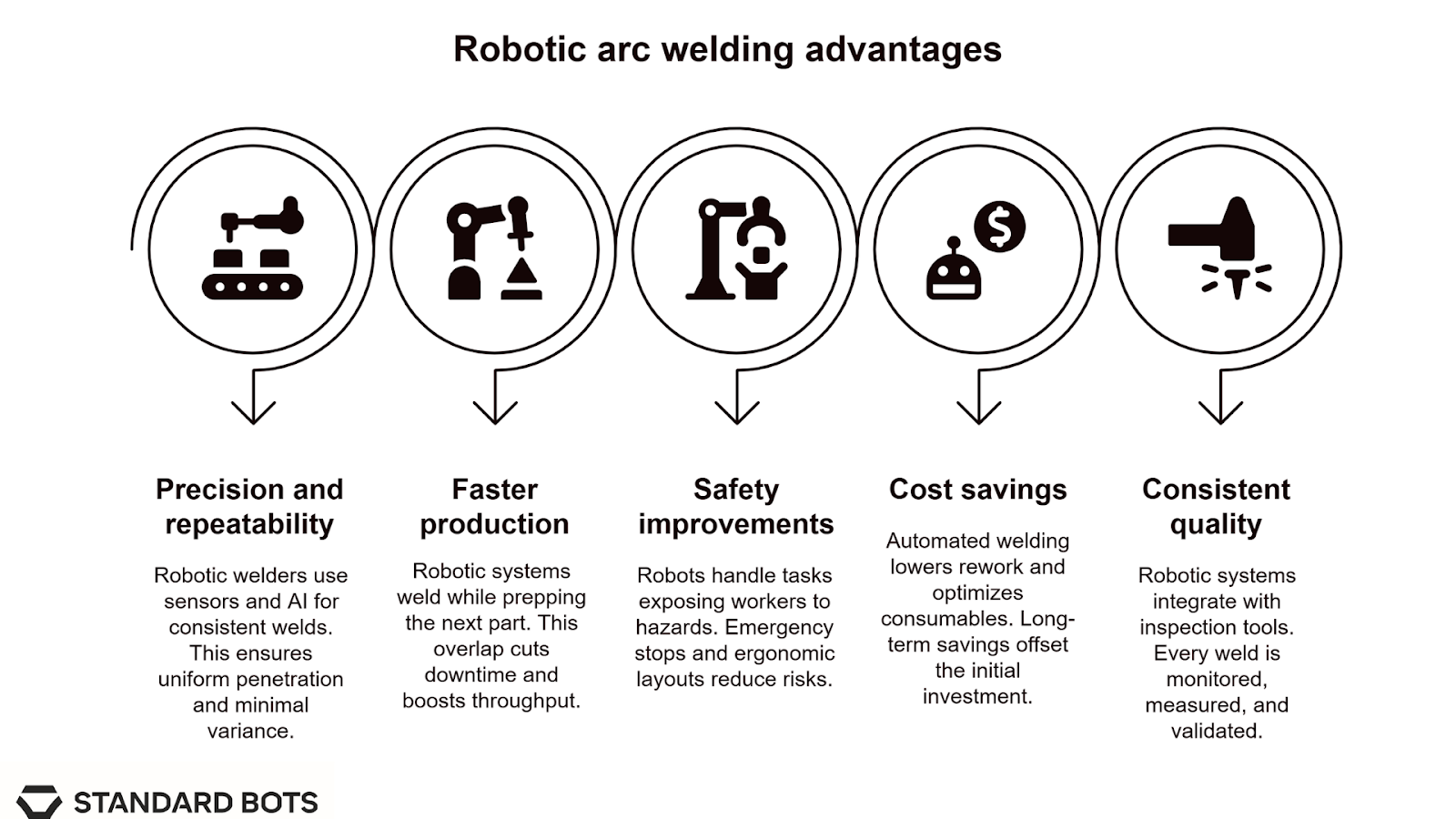
Choosing arc welding robots solves real production problems, like slow cycle times, inconsistent welds, rising labor costs, and safety risks. It’s not just about keeping up with automation trends.
If any of that sounds familiar, here's what robotic systems can fix:
1. Precision and repeatability: Robotic welders use advanced sensors and AI-driven pattern recognition to make micro-adjustments in real time. This leads to consistent weld paths, uniform penetration, and minimal variance between cycles.
2. Faster production cycles: With motion planning algorithms and adaptive speed controls, robotic systems can weld while simultaneously prepping or loading the next part. This overlap cuts downtime and boosts overall throughput.
3. Safety improvements: Robots take over tasks that expose workers to hot metals, toxic fumes, and repetitive strain. Built-in emergency stop protocols and ergonomic layouts further reduce workplace risks.
4. Cost savings over time: Automated welding lowers rework and scrap rates, optimizes the use of consumables, and keeps maintenance predictable. These long-term savings often offset the upfront investment.
5. Consistent quality control: Robotic systems integrate easily with inspection tools like vision cameras or ultrasonic sensors. That means every weld can be monitored, measured, and validated, without slowing down production.
Notably, manufacturers that switch to robotic arc welding can often take on larger contracts and tighter-deadline projects they previously had to turn away due to capacity constraints.
How robotic arc welding works
Robotic arc welding follows a structured sequence powered by sensors, AI, and real-time feedback.
Here's how a typical cycle works:
- The robot loads or receives the workpiece: Fixtures or positioners hold the metal parts in place while the robot aligns itself for welding.
- Sensors calibrate position and material: Cameras or sensors detect joint location, surface irregularities, and material type before the weld begins.
- AI selects parameters: Based on the input, the system adjusts current, voltage, travel speed, and torch angle to suit the specific weld path.
- Welding torch executes the weld: The arc is activated, the filler metal melts, and the robot moves along the programmed path with high accuracy.
Optional: Post-weld scan or inspection: Vision systems or non-destructive testing tools check the weld for consistency, defects, or gaps.
Advanced systems adapt mid-weld using feedback loops, automatically correcting travel angle, speed, or arc length in response to material variation or positional drift. This ensures each weld stays within spec, even under changing conditions.
Robotic arc welding vs. manual welding
Applications in modern manufacturing
- Automotive: Robotic arc welding is a core part of automotive manufacturing, used for frame assembly, chassis parts, and exhaust systems. Robots deliver consistent welds at scale, reducing errors and speeding up production.
In EVs and lightweight vehicle builds, they handle thinner materials and mixed metals with less heat distortion. So, whether it's door panels or mufflers, robotic welders keep quality tight and operations efficient. Even when running 24/7 on high-volume lines. Continuous operation also means manufacturers can fulfill rush orders without overtime costs.
- Aerospace: In aerospace, robotic welding is used for high-precision welds on materials like aluminum and titanium. These metals need strict heat control and uniformity, which obviously robots handle better than humans.
Common uses include engine parts, brackets, and internal structures where consistency is critical. With real-time feedback and vision systems, robotic welders meet tight industry standards. Plus, they help in reducing waste and increasing throughput.
- Construction: Robotic arc welding is becoming more common in construction, especially for structural steel like I-beams and brackets. It's often used in prefabricated sections built off-site, where weld consistency matters.
Robots improve accuracy, reduce rework, and make it easier to scale modular construction. They also take on jobs in hot or confined spaces. This is important for improving worker safety while speeding up the build process.
- Consumer products: In consumer goods, robots weld parts for appliances like washing machines, refrigerators, and kitchen tools. These jobs often involve thin metal sheets that need precise, clean welds to avoid warping.
Robotic systems apply just the right heat and speed to protect both function and appearance. With quick reprogramming, they easily switch between product lines and keep up with changing designs. Many manufacturers also use robotic arms for polishing and sanding tasks alongside welding.
How much does a robotic arc welding system cost?
A robotic arc welding system can cost $50,000 to $150,000. This price includes the robot arm, welding power source, control unit, wire feeder, and safety enclosures. The exact price depends on the complexity of the setup and the level of automation required.
Once installed, operating costs are relatively steady. These include routine maintenance, electricity, shielding gas, and consumables like wire and nozzles. Robots operate without breaks or performance drops, and that reduces errors and boosts output.
Most manufacturers see a return on investment within 12 to 24 months. Savings come from reduced rework, fewer material losses, and the ability to cover multiple shifts with one system. Over time, this leads to lower cost per weld and a more predictable production flow.
Beyond the financial ROI, robotic arc welding allows manufacturers to bid on precision-critical projects that manual welding operations simply cannot win. This creates access to new market segments and revenue opportunities.
Robotic arc welding challenges
These are some of the most common robotic arc welding limitations manufacturers should consider before investing.
- High setup complexity for varied jobs: Programming and tooling can be time-consuming when switching between different product types or welding tasks. This makes robotic welding less agile for mixed production lines.
For example, manufacturers producing both stainless steel tanks and aluminum frames on the same floor may face delays from frequent reprogramming and torch adjustments.
- Not ideal for small-batch or custom work: For one-off jobs or low-volume runs, the time and cost to program the robot often outweigh the benefits. Manual welding remains more practical in these cases.
- Requires operator training for setup and oversight: Even with automation, technicians must set parameters, monitor quality, and troubleshoot issues. An AWS Welding Journal study shows that SMEs adopting cobots still require well-trained staff to achieve consistent weld quality, highlighting that automation doesn’t replace expertise.
- Integration with legacy systems can be tricky: Older factory setups may not easily support robotic welding cells. Custom interfaces or infrastructure upgrades are often needed to make them compatible. This is where having easy-to-use robots with modern interfaces becomes crucial.
The future of robotic arc welding
Robotic arc welding is moving beyond basic automation. In the coming years, systems will become smarter, easier to use, and more flexible across industries. AI and machine learning are enabling real-time weld adaptation.
Rather than sticking to fixed settings, future systems will adjust based on arc behavior and material feedback in real time. This lets the robot correct deviations instantly, improving accuracy and reducing scrap.
Programming is also becoming more accessible. Low-code and no-code platforms will let operators define weld paths or make adjustments through simple visual interfaces, reducing dependence on specialized programmers.
This is important to understand because there are several kinds of robotic welding systems in use today. Each is suited for different materials, production needs, and precision levels.
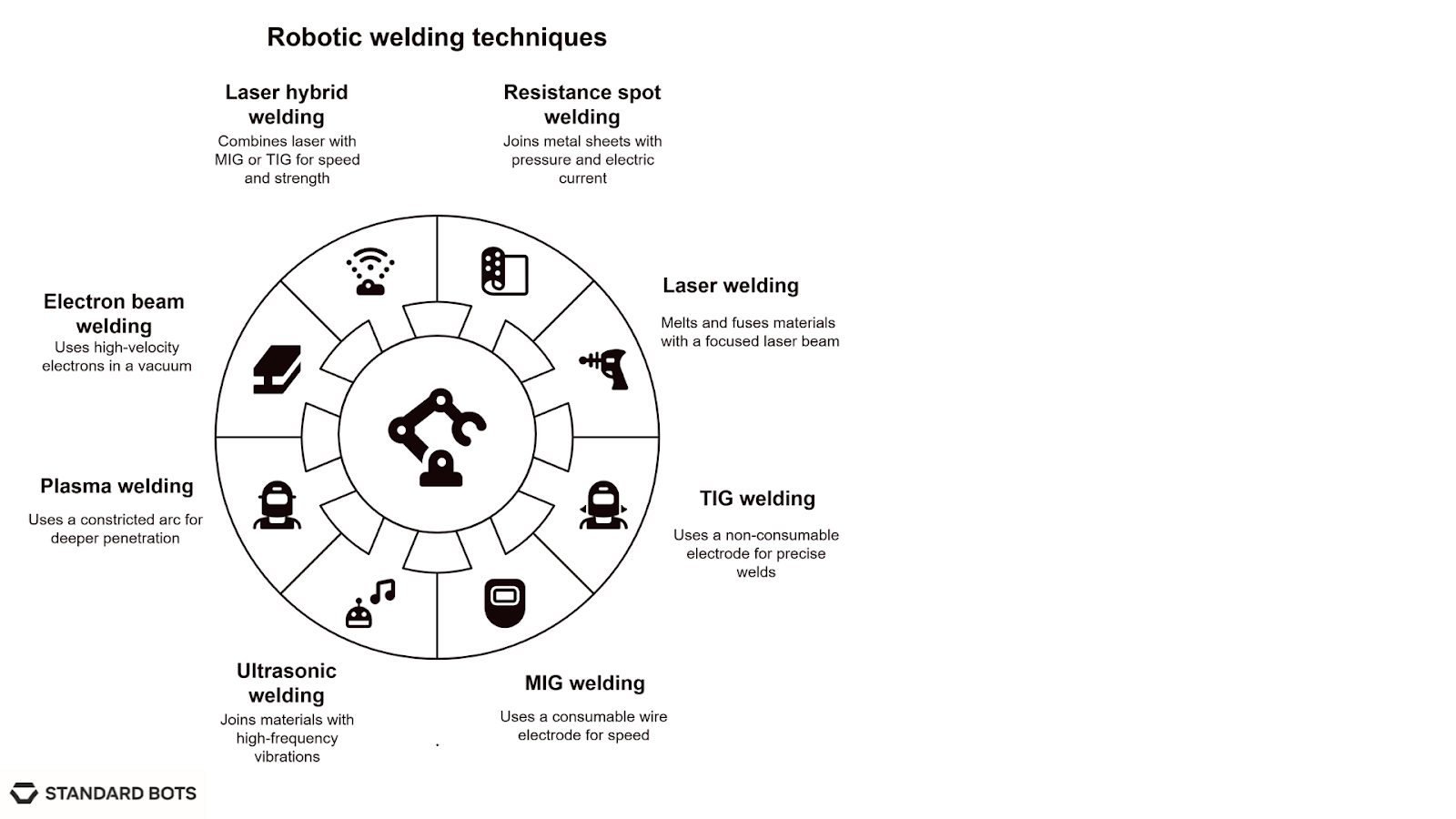
Smarter safety systems are being integrated directly into the robot's workflow. Vision sensors and proximity detection help prevent collisions, ensure correct part positioning, and allow robots to operate safely around humans without physical barriers. These advances make industrial automation more accessible to smaller manufacturers.
Collaborative robots, or cobots, are starting to play a bigger role in welding. These machines can share workspaces with people and assist in tack welding or part handling tasks. They are especially useful in small shops that want to automate without overhauling their entire setup. Learn more about collaborative robots and their applications beyond welding.
The future is not just about more robots, but about more intelligent, adaptable, and accessible welding systems that fit into a wider range of production environments.
Best robotic arc welding solutions in 2025
1. Standard Bots RO1: The RO1 is a six-axis industrial robot built for welding, handling, and assembly. What makes it stand out is its affordability and U.S.-based manufacturing. It pairs with popular welders like Miller and Lincoln and includes easy-to-use software for programming weld paths and torch angles. If you're looking for a flexible system that doesn't require a dedicated robotics team to run, RO1 is a strong contender.
2. FANUC ARC Mate Series: FANUC's ARC Mate robots are widely used across automotive and general manufacturing. They support high-speed welding with built-in wire feeders and come pre-integrated with Lincoln Electric and Fronius systems. FANUC offers one of the most robust support networks globally, making it a go-to for large-scale, high-volume applications.
3. ABB IRB 1660ID: Designed specifically for arc welding, the ABB IRB 1660ID features internal cable routing and tight torch control. It offers fast cycle times and is optimized for narrow workspaces. ABB's RobotStudio software allows offline programming and simulation, which helps reduce downtime during setup and changes.
4. Yaskawa Motoman AR Series: The AR Series from Yaskawa is built for high-precision welding across thin materials and complex geometries. These robots integrate seamlessly with power sources from Miller, Lincoln, and OTC. Yaskawa's programming interface is beginner-friendly, and their support for collaborative setups is expanding in 2025.
Final thoughts
Robotic arc welding is a proven solution for improving throughput, safety, and quality in welding-heavy operations.
You could be running a small machine shop or managing high-volume production lines, robotic welding systems offer measurable benefits in consistency, throughput, and worker safety. The technology has matured to the point where setup is faster, programming is simpler, and ROI is predictable.
If you're still relying on manual welding, the bigger risk might be waiting. Delaying automation often leads to higher long-term labor costs and slower output, while competitors continue to move forward with modern systems.
Ready to explore how robotic welding fits into your broader automation strategy? Check out our complete guide to manufacturing automation for more insights.
Next steps with Standard Bots' robotic solutions
Standard Bots' RO1 is the perfect six-axis cobot addition to any shop floor, big or small.
- Affordable and adaptable: Available for $37K (list), which is half the cost of comparable robots.
- Precision and power: With a repeatability of ±0.025 mm and an 18 kg payload, RO1 handles even the most demanding jobs, like welding, palletizing, and pick-and-place. You name it.
- AI-driven simplicity: Equipped with AI capabilities on par with GPT-4, RO1 integrates perfectly with production systems for even more advanced automation.
- Safety-first design: Machine vision and collision detection mean RO1 works safely alongside human operators.
Schedule your risk-free, 30-day on-site trial today and see how RO1 can bring AI-powered greatness to your shop floor.
FAQs
1. What's the best robotic arc welding system for small manufacturers?
RO1 is the best robotic arc welding system for small manufacturers in 2025. It's affordable at $37K (list), easy to program with no-code software, and integrates with popular welding equipment like Miller and Lincoln. Plus, it handles multiple applications beyond welding, making it a versatile investment.
2. How long does it take to set up robotic arc welding?
Setup time varies by complexity, but most systems take 1 to 3 weeks for installation and programming. RO1 can be deployed faster due to its plug-and-play design and intuitive software. Simple welding applications can run within days.
3. Can robotic welding handle different materials?
Yes, modern robotic welding systems can handle various materials, including steel, aluminum, stainless steel, and specialty alloys. The key is having the right sensors and programming to adjust parameters for each material type.
4. Is robotic arc welding safe around human workers?
Cobots like RO1 are designed to work safely alongside humans, with built-in collision detection and force-limiting features. Traditional industrial robots may require safety barriers, but cobots can operate in shared workspaces.
5. What's the ROI timeline for robotic arc welding?
Most manufacturers see ROI within 12–24 months. Savings come from reduced labor costs, improved quality, less rework, and the ability to run multiple shifts. The exact timeline depends on your production volume and current labor costs.
Join thousands of creators
receiving our weekly articles.