An order picking robot doesn’t get tired, doesn’t make too many mistakes, and won’t try to unionize, which is why your warehouse probably needs one.
They’re sorting, lifting, and scanning faster than your best worker, and unlike Chad in receiving, they don’t rage-quit over label printers.
Whether you run a 3PL, a pharma warehouse, or a DTC sweatshop with dreams of scaling, order picking machines are what get boxes out the door on time. Plus, they’re cheaper than you’d expect.
What is an order picking robot?
An order picking robot in your warehouse focuses on one thing: Grab the right item from a shelf, bin, or tote — then hand it off for packing or shipping. No blubber, no missed SKUs, and absolutely no “sorry I forgot to scan that.”
These bots have one thing on their robo-brains: Making your fulfillment flow way less chaotic. But they’re not all the same, and they’re definitely not doing the whole job alone.
What do order picking robots do?
- They pick, they don’t pack or sort: A robot that grabs headphones out of bin 7? That’s a picking robot. A robot that tapes boxes shut or stacks them on a pallet? That’s someone else’s problem.
- They live in the middle of the mess: Most picking robots hang out between storage and packing. Think of them as the cool middle child of the warehouse, holding it all together while the others fight for attention.
- They come in all shapes and grippers: Some are mounted. Some roam around like alcoholics. Some use suction cups. Some flex multijoint arms with machine vision and deep learning.
- They do piece picking, case picking, or both: One robot might carefully grab a lipstick. Another might haul a 40-pound dog food bag. Welcome to the wide world of warehouse picking robots.
- They play well with others (sometimes): Most work with WMS, ERP, or a full robotic order preparation system, unless you bought one off a sketchy auction site, in which case, good luck.
- They are not your IT guy’s replacement (yet): They follow instructions well, but don’t ask them to explain your VPN setup or deal with Todd in accounting.
Common applications for picking robots
Picking robots are in the trenches across industries, hauling everything from shampoo to syringes.
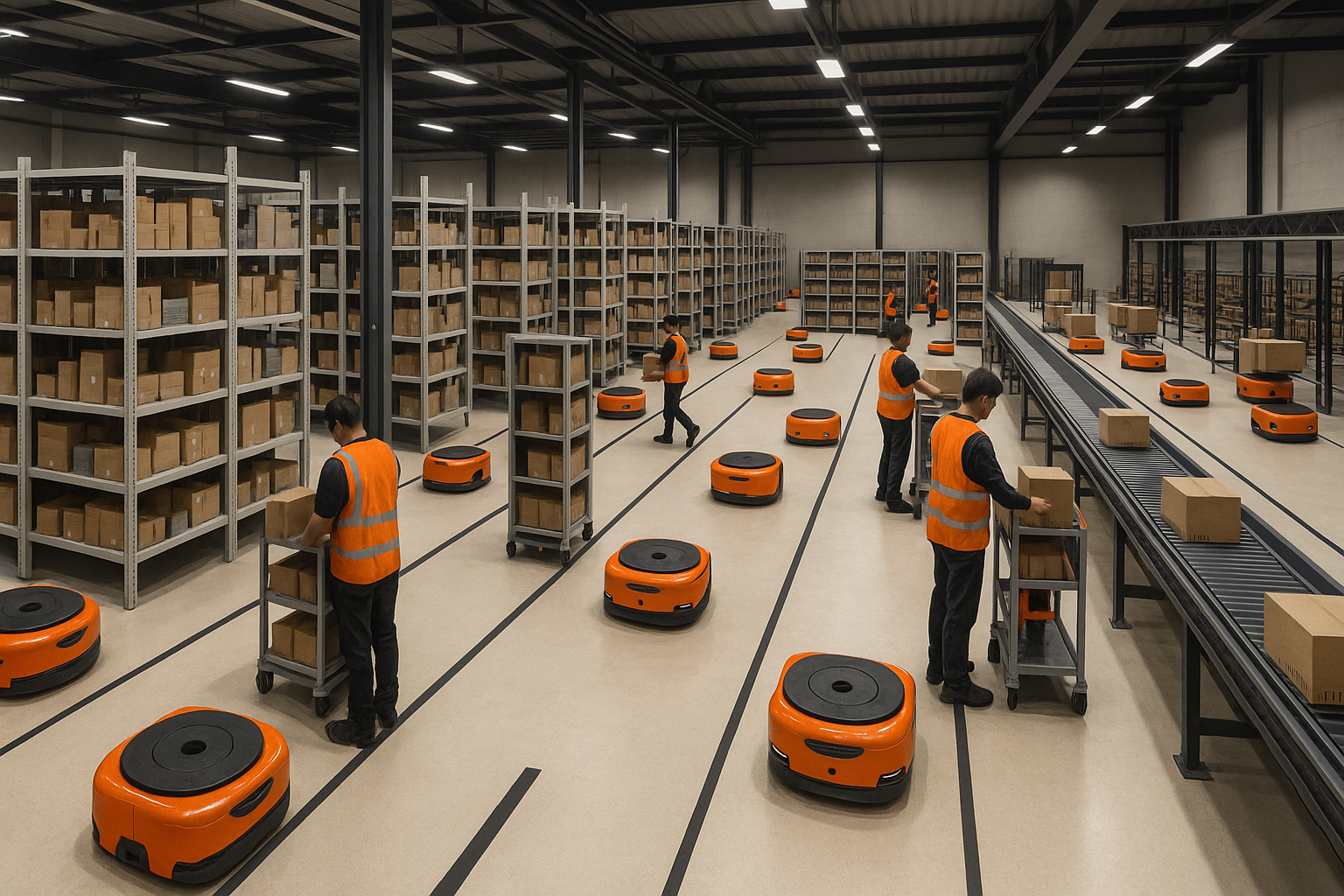
Where are order picking robots already grinding for XP?
- E-commerce and 3PL hellscapes: Fast-moving SKUs, daily inventory churn, and customers who want their socks yesterday. Picking robots crush it in DTC fulfillment centers, where speed and accuracy decide who survives Q4.
Example: Amazon’s Vulcan robot helps workers pick items from high/low bins with tactile sensing. - Direct-to-consumer retail setups: When you're shipping 5,000 eyebrow pencils an hour, one mispick = angry influencer. Order picking robots reduce errors and protect your review score like their job depends on it (because it kind of does).
Example: GEODIS gets 99.8% order accuracy, managing over 17,000 SKUs. - Pharmaceutical and medical logistics: These environments need precision, sterility, and near-zero “oops.” Robotic picking systems handle vials, blisters, and sensitive meds without sneezing on them or sending the wrong thing to surgery.
Example: RightHand Robotics’ RightPick robot gives people ultra-fast, traceable pharma picking. - Kitting-heavy manufacturing lines: Got custom kits? Assembly ops? Subscription boxes with 12 micro-SKUs and a seasonal mug? Automated picking robots can handle that puzzle way better than Steve with a clipboard.
Example: Pick-it 3D and UR5 collab on vision-guided kitting in manufacturing. - Food and cold chain logistics: Yes, warehouse picking robots can handle frozen goods. No, they don’t need gloves. Bonus: they won’t complain about the temperature or “accidentally” eat a cookie off the line.
Example: RIOS DX-1 robot picks and sorts fragile (and tasty) food items like eggs and chips. - Returns and reverse logistics: Picking doesn't stop at outbound. Some systems now help sort and prep returns, which is helpful when your customer sends back three dresses and one completely unrelated toaster.
Example: Locus Robotics ramps up returns efficiency in robotic reverse logistics.
Types of warehouse picking robots
Not all picking robots have the same vibe. Some roll solo with grippers, some ride tracks like tiny subway goblins. And some just sit in one place, looking like tortured poets.
If you're not sure where they all fit into your setup, our warehouse robot types guide breaks it down even further.
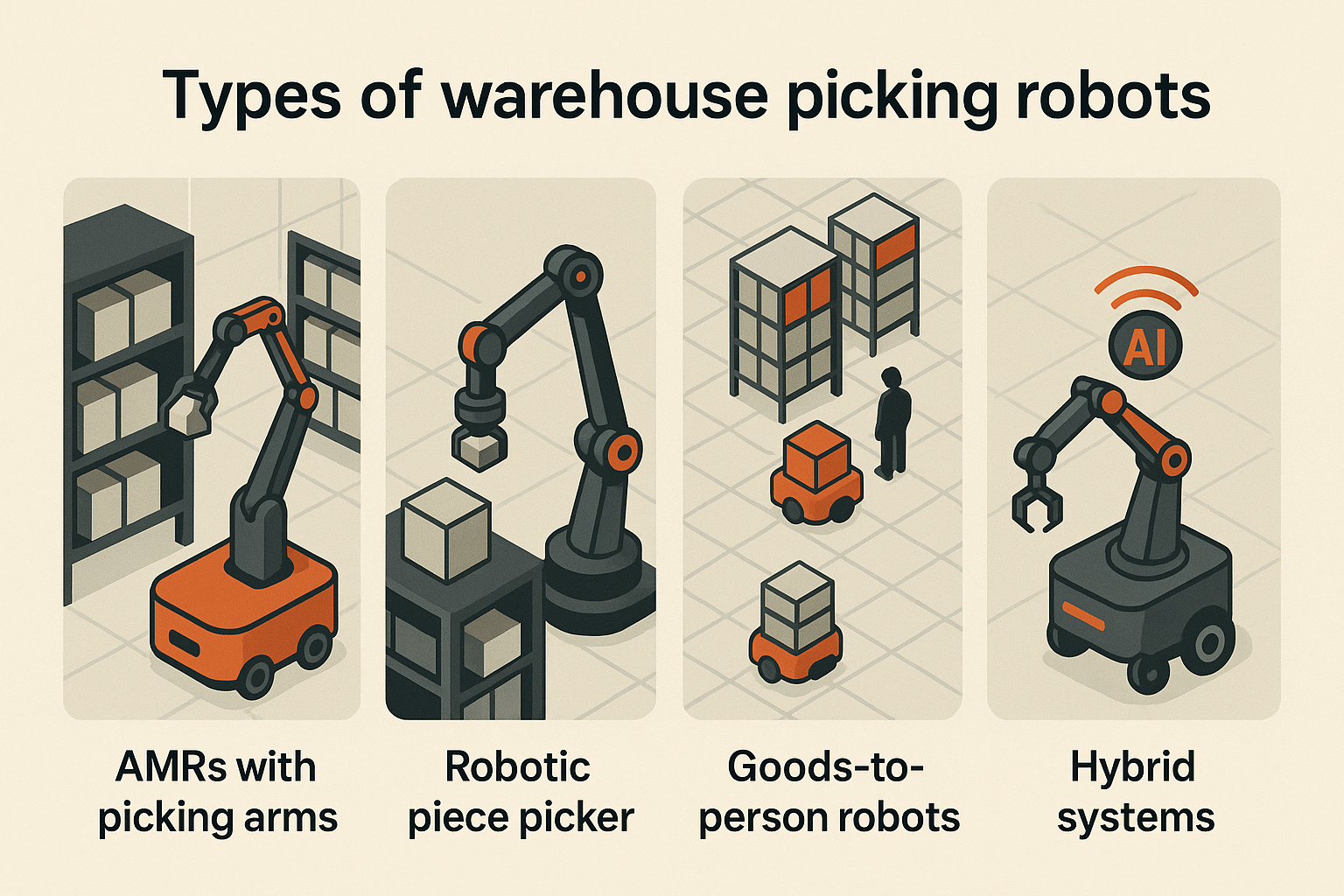
How much do picking robots cost?
Picking robots aren’t dollar-menu cheap, but they’re way more accessible than you’d think. Whether you’re going full automation or just ditching Pete and his barcode scanner, here’s what a decent order picking robot might run you in 2025.
The money math behind robotic picking
- Starter bots (for the “I just need a picker” crowd): You’re looking at around $35K–$75K. These basic piece-picking bots use suction or grippers and are built for simpler jobs. Great for entry-level automation.
Read more: How much do robots cost? - Mid-range machines (the “this one has a brain” tier): These come in around $75K–$150K. You’re paying for smarter vision systems, better object handling, and higher pick accuracy. Most warehouse picking robots fall in this range.
- Enterprise-level prep systems (for people who say “WMS integration” without flinching): Custom builds with full-stack software, AI-driven robotic order preparation systems, and seamless warehouse sync can land north of $200K. If your fulfillment center is bigger than your high school, this is your lane.
Dig into real-world setups: The 3 best robot arms for any industrial job. - Leasing (aka RaaS, aka “I want the bot, not the bill”): Some vendors offer picking robots on lease starting at a few bucks per hour. It’s a solid move for teams that want the tech without going full CapEx commitment.
- Maintenance and upgrades: Budget around 10–15% of the robot’s value annually to keep it from glitching out mid-shift. That covers service, software updates, and whatever that one arm keeps doing when it’s “calibrating.”
- Integration fees: These sneak up fast. Between training, software customization, and retrofitting your layout, total deployment cost can climb well past the hardware price, especially for larger robotic picking systems.
Related read: Case packing automation and Palletization show where your robot fits in the bigger picture.
How to choose the right picking robot: 7 key checks
- Inventory profile: Got 5,000 micro-SKUs that vary by label color? You’ll want a vision-guided piece picker. Moving pallets of identical boxes? A simpler order picking machine can handle it.
- Accuracy vs. speed trade-off: Some robotic picking systems are wicked fast. Others can be gentle with fragile items. You probably can't have both unless you’re spending enterprise-level money.
- Warehouse layout: If your space looks like a cursed puzzle, go for mobile automated picking robots that can handle clutter. Compact, predictable zones? Go for goods-to-person or shuttle systems.
- Integration friendliness: Make sure the bot plays nice with your WMS, ERP, or whatever duct-taped stack your IT team is clinging to. The best warehouse picking robots should sync with minimal drama.
- Human-robot handoffs: Are you pairing bots with human packers or going lights-out? Some systems shine in hybrid flows. Others panic when Mike the temp moves too fast.
- Tech support + workforce skill level: If your team panics at the word “firmware,” skip the hyper-custom solutions. Stick with intuitive systems that don’t need you to absorb a masterclass on robotic order preparation systems.
- Total cost of ownership vs. short-term savings: Cheaper isn’t always smarter. A $20K robot that breaks every month costs more than a $40K one that never calls out, never trips over a tote, and doesn’t need therapy. Or, when in doubt, just buy RO1 by Standard Bots.
The 7 best automated picking robots in 2025
Most automated picking robots look great in demo reels, until they meet an actual warehouse.
Scene: Missed scans, mangled SKUs, and a breakdown the second someone drops a granola bar on the floor. So we filtered the noise and found seven systems and companies that can handle real warehouses.
1. Standard Bots RO1

RO1 isn’t some vague “robotic solution.” It’s a six-axis, AI-powered order picking robot with precision so tight it makes your calipers nervous. It’s made for manufacturers, but it thrives in real-world picking, where bins aren’t labeled perfectly, boxes vary in size, and humans occasionally throw things.
What does it actually do?
- Picks items up to 18 kg with ±0.025 mm repeatability
- Uses machine vision to ID objects, even when they’re jumbled together in chaos bins
- Adapts on the fly using AI that’s trained like a GPT-4 cousin
- Supports rapid pick-and-place for case packing, sorting, and direct-to-line fulfillment
- Handles welding, QC, painting, and CNC machine tending
- Mounts in multiple configurations (floor, ceiling, or elbow-drop position — your call)
Why does it make the list?
- Easy WMS + ERP integration, no 12-week setup spiral
- Can go from install to production in a single day
- Costs half as much as legacy robotic order preparation systems
- Affordable, with a risk-free 30-day trial
Best use case
Automated picking robots in mixed-SKU bins, high-speed packing zones, and anywhere a dumb arm would normally panic and shut down.
2. LocusBots
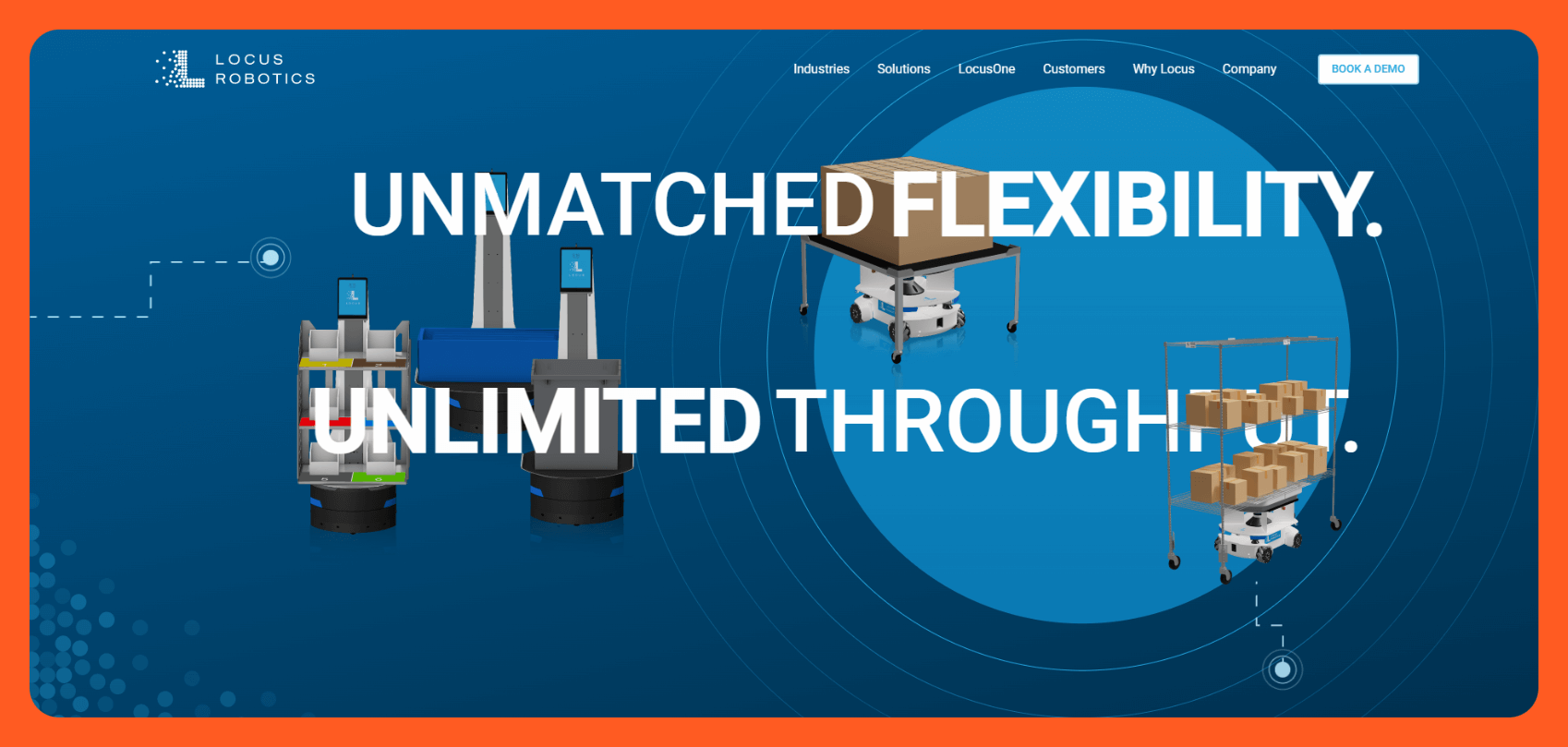
LocusBots pick, they sprint, reroute, recalculate, and make your pickers feel like billionaires with personal robot chauffeurs. These AMRs navigate warehouse floors like seasoned commuters and deliver totes to wherever your human pickers are stationed.
What does it actually do?
- Comes in multiple models (Origin, Vector, Max), handling payloads from 40 to 120 lbs
- Uses real-time route optimization to cut down on traffic and congestion
- Offers autonomous navigation with obstacle detection, zone-specific speed control, and safe human interaction
- Fully integrates with your WMS for better job allocation and inventory sync
- Operates up to 14 hours per charge with less than 60 minutes of recharge time
Why is it on the list?
- Proven to double productivity by eliminating unproductive walking
- Fleets can scale from 10 to 500+ bots without redoing your layout
- Includes analytics dashboards to measure pick rates, route efficiency, and ROI in real time
- Already in use at Geodis, DHL, and Radial, not just hype
Best use case
High-SKU ecommerce and 3PL warehouses that want human pickers to stop burning 12,000 steps per shift (they’re still going to have to get their steps in).
3. inVia Picker
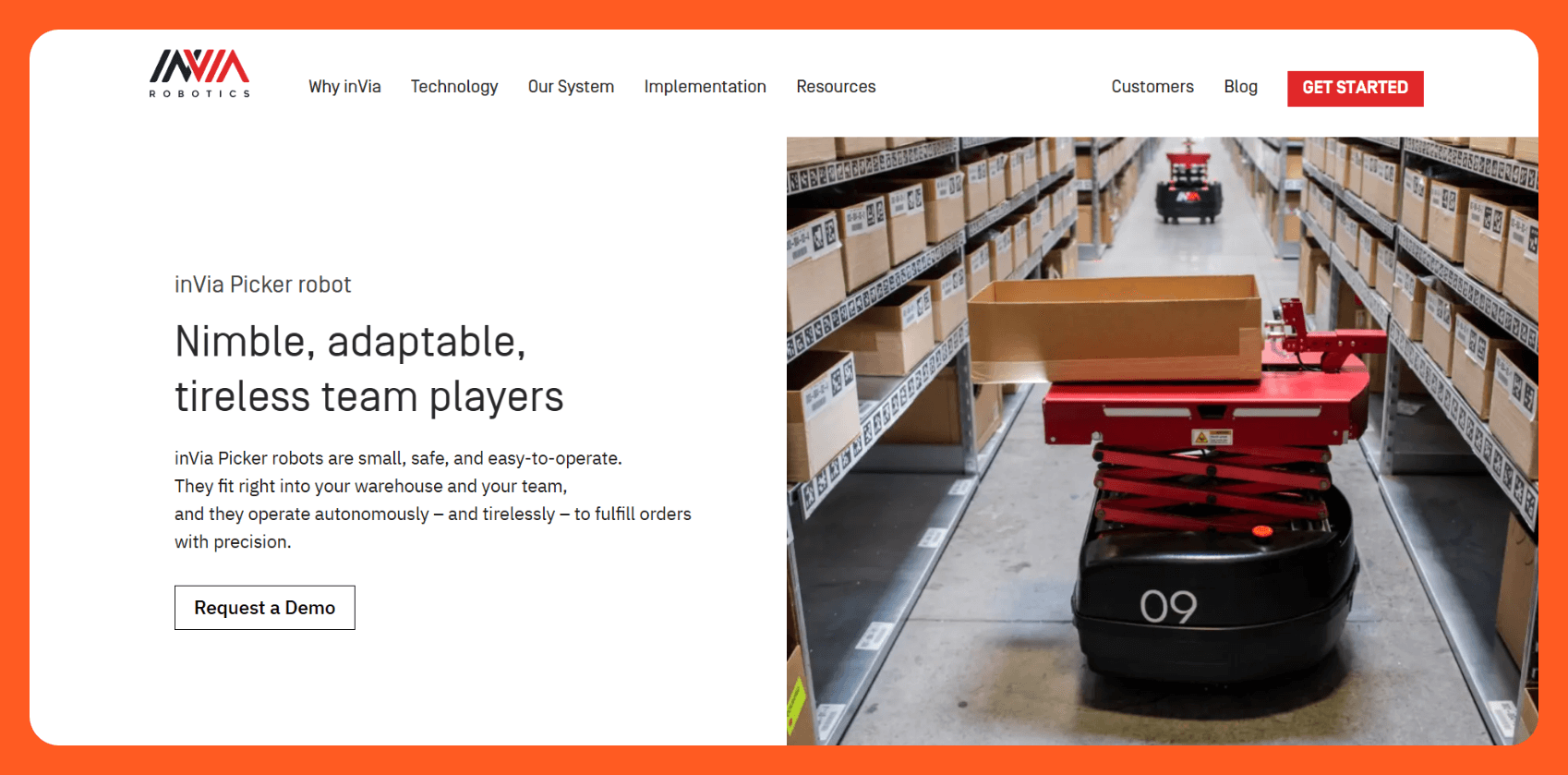
inVia’s Picker looks like a minimalist shelf-scooter but works like a precision retrieval bot. It’s a goods-to-person system for real warehouses. No bulldozing layouts, just quiet bin delivery that lets your workers pick without wandering blindly into forklift lanes.
What does it do?
- Reaches up to 8 feet and retrieves bins directly from standard racking
- Uses SLAM navigation to chart efficient, obstacle-free routes
- Travels up to 5 mph and carries up to 40 lbs
- Powered by a 10-hour hot-swappable battery with auto-recharging
- Syncs with inVia Logic, a software layer that optimizes pick paths and order waves live
Why does it make the list?
- You lease it like software; zero CapEx, full support
- Doesn’t care if your warehouse is “not automation-ready”
- Improves pick rates 2–3x by cutting travel and batching smarter
- Used in pharma, consumer goods, and DTC fulfillment
Best use case
Mid-size operations that want robotic goods-to-person picking without gutting their existing floor plan
4. AutoStore + RightHand Robotics
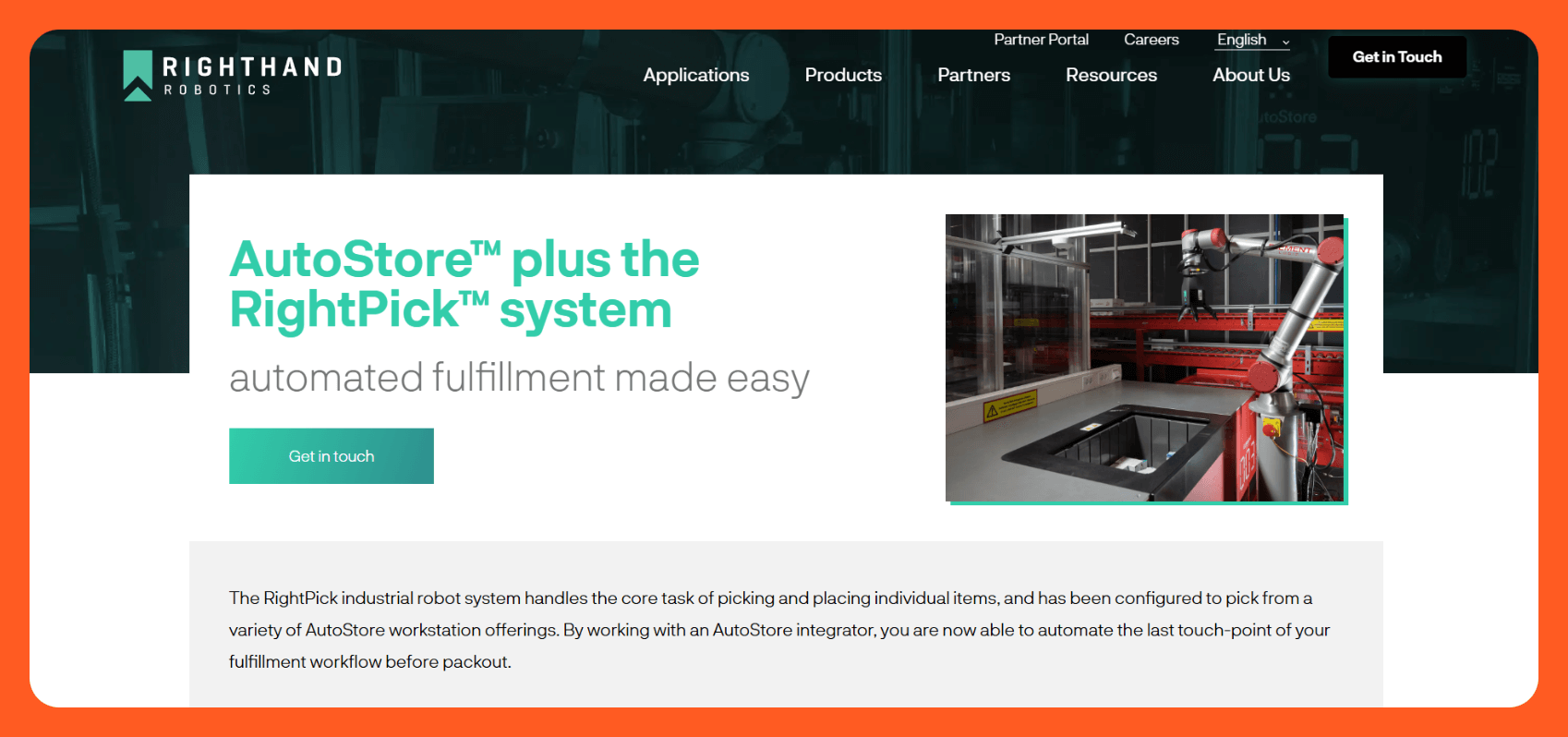
AutoStore is the storage savant. RightHand is the surgical extractor. Together they form a hyper-efficient cube-based picking system with AI grip finesse and terrifyingly fast retrieval.
What does it do?
- AutoStore delivers densely stacked storage bins to workstations using grid-running bots
- RightPick uses vacuum and tactile-sensor grippers to pluck SKUs out of those bins
- Learns from each pick; tracking orientation, weight, packaging type, and success rate
- Supports item validation and barcode scanning mid-pick
- Runs continuous feedback loops to improve accuracy and adapt to new SKUs
Why is it on the list?
- Cuts warehouse footprint in half while increasing throughput
- The picker handles both structured and unstructured products, even polybags and tubes
- Fully integrates with WMS and ERP for true last-touch automation
- Already deployed in logistics for apparel, electronics, and health sectors
Best use case
High-SKU environments with dense storage and zero tolerance for mispicks or human fatigue.
5. Brightpick Autopicker
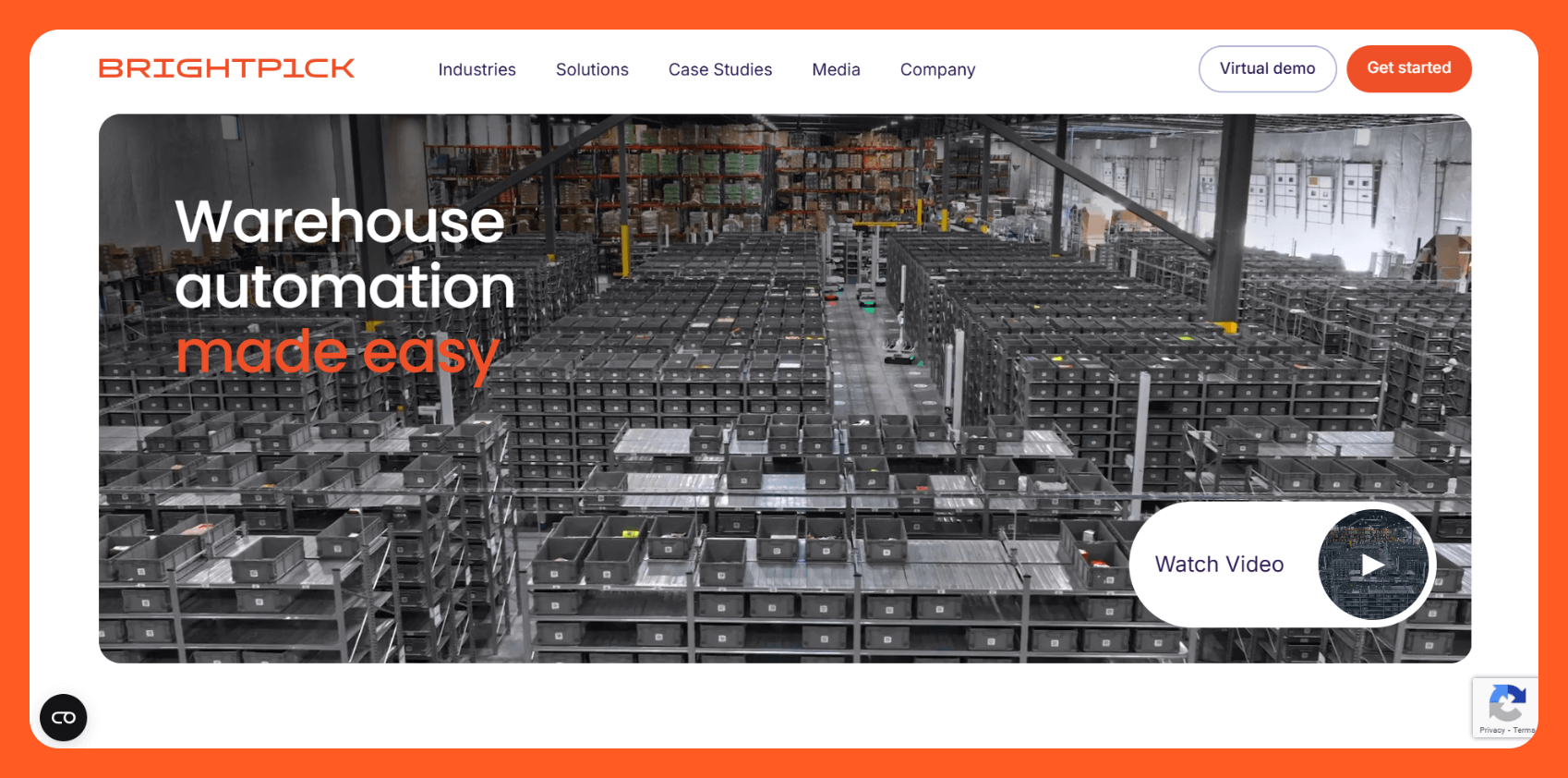
Brightpick made an awesome picker that drives, picks, delivers, and never whines about overtime. This is the first commercially available autonomous mobile picking robot to do it all. No relay, no swap, and no humans needed.
What does it do?
- Combines AMR navigation, storage tote retrieval, and order picking into one unit
- Uses a dual-tote design to grab stock and deposit picked items without stopping
- Vision-guided AI handles barcode-free picking and object ID in dynamic environments
- Supports real-time order consolidation in-aisle, reducing sortation bottlenecks
- Runs via SLAM and integrates natively with Brightpick’s software platform
Why does it make the list?
- Delivers up to 1,000 picks per hour per robot, with scary accuracy
- Operates in narrow aisles and on standard shelving
- Reduces fulfillment costs up to 50% vs. traditional person-to-goods setups
- Already used by grocery, medtech, and cosmetics brands in live production
Best use case
Fulfillment centers that want fewer handoffs, higher accuracy, and robots that multitask like ops managers that downed 5 Red Bulls.
6. Geek+ RoboShuttle + P900
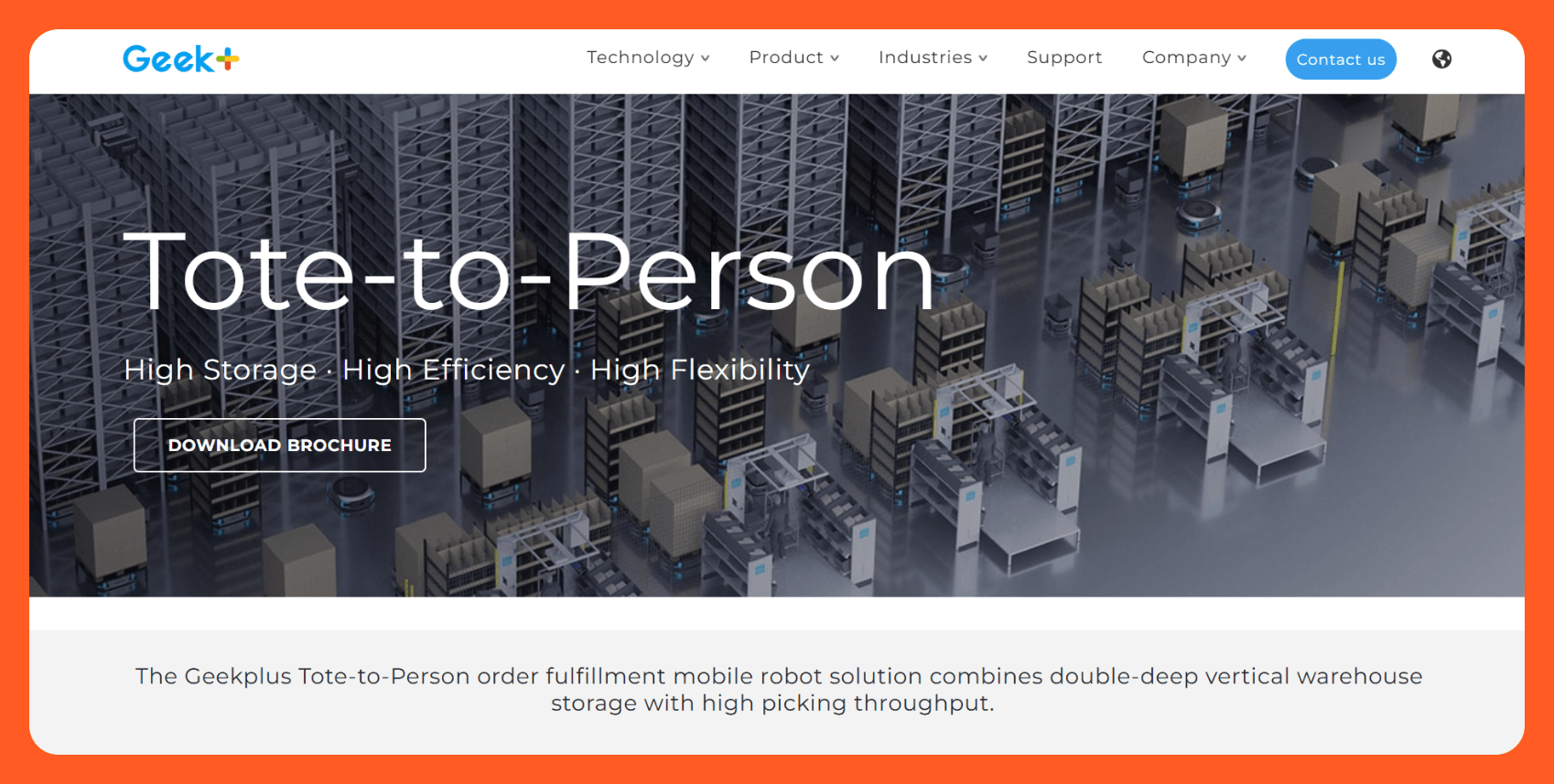
Geek+ isn’t trying to reinvent the robot, it just scales the hell out of it. The RoboShuttle + P900-series combo is a hybrid goods-to-person system that tackles dense storage and lightning-fast tote movement with one mission: don’t waste space, don’t waste time.
What does it actually do?
- RoboShuttle handles vertical storage retrieval from shelves up to 5 meters high
- P900 AMRs ferry bins, racks, and order totes across zones with zero human handoff (there are higher-payload models out there, too)
- Dual lift designs let them handle different tote sizes in the same pass
- Fleet software orchestrates bin delivery, recharge cycles, and route optimization in real time
- Integrates with major WMS platforms through Geek+'s own middleware stack
Why is it on the list?
- Enables >30% more storage density than traditional shelving
- Offers 500+ picks/hour per station when deployed in high-throughput environments
- Scales fast; customers can add racks, bots, or stations modularly
- Actively deployed in retail, grocery, and consumer electronics, not just a prototype stack
Best use case
Warehouses with vertical ambitions and SKU chaos that need real robotic discipline, fast.
7. OSARO Robotic Piece Picking Systems
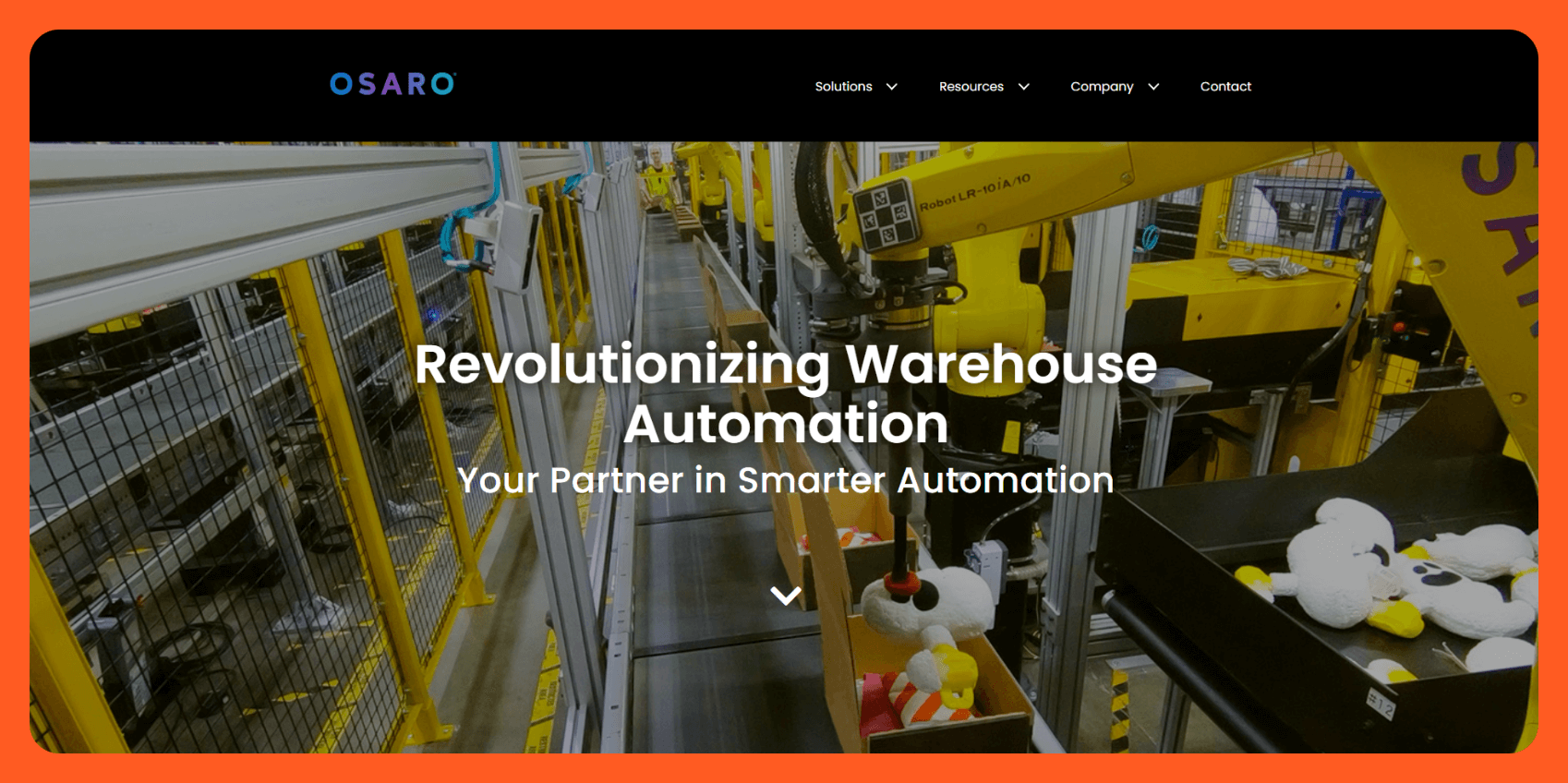
OSARO’s robots pick things, interpret the item, predict how best to grab it, and execute like they’ve been doing it for years. These vision-first piece pickers are built for high-mix environments where labels lie, shapes are weird, and humans keep making mistakes that robots usually don’t.
What does it actually do?
- Uses OSARO SightWorks™ to identify, track, and pick SKUs based on shape, material, and even reflectivity (all without a barcode)
- Adapts to new products on the fly without retraining or reprogramming
- Supports vacuum and two-finger grippers with automatic grip selection
- Handles pick-and-place from bins, trays, conveyors, and ASRS exits with human-like fluidity
- Integrates well with AMRs, conveyors, AutoStore setups, and third-party warehouse control systems
Why is it on the list?
- Delivers 24/7 picking with consistent accuracy and zero sick days
- Already deployed in e-commerce, cosmetics, apparel, and 3PL fulfillment
- Doesn’t care if your packaging is shiny, squishy, clear, or misaligned — it just figures it out
- Available as a full install or Robot-as-a-Service, so you can get started without drowning in CapEx
Best use case
Facilities that play a juggling game with high-mix SKU profiles, fast order cycles, and fragile packaging, especially in industries where pick errors = returns = rage.
What’s next for robotic order picking?
Robots used to just grab stuff. Now they’re predicting what you’ll ship tomorrow, scheduling maintenance for themselves, and throwing gentle shade at your fulfillment ops.
- AI-powered pick prediction: Advanced robotic order preparation systems are already training on SKU velocity and seasonality. The next wave? Bots that know what you’re about to need before the order’s even placed, and have it halfway packed.
- Multi-agent coordination: It’s not just “send a bot.” Future systems will run swarms of AMRs, arms, and shuttles that split tasks dynamically. Think Uber Pool, but for bin retrieval and tote delivery, minus the awkward small talk.
- In-aisle consolidation: Bots like Brightpick have started the trend, but the future is full tote-building mid-run. Robots will assemble orders on the fly instead of handing everything off to a slow post-pick zone.
- WMS-native automation: Robotic picking won’t be a bolted-on third-party thing. It’ll be baked into the warehouse OS, pulling SKU data, labor schedules, and traffic patterns into every pick decision, automatically.
- Vision that doesn’t suck: Low-light, glare-heavy, packaging-shifted picking used to be a nightmare. The next gen of vision systems (like OSARO’s and Standard Bots’) are already showing they can ID a shiny bottle cap buried under crumpled polybags.
- Lights-out fulfillment centers: Full dark. No humans. Just bots picking, sorting, packing, and prepping pallets while the rest of us sleep. It’s real, it’s scaling, and it’s terrifyingly efficient. Learn about lights-out manufacturing.
Summing up
A great order picking robot lifts your entire operation: From AI-driven arms to AMRs that navigate rush-hour warehouse traffic better than your senior manager, these bots are at the core of modern fulfillment. Faster, smarter, and shockingly good at not messing up.
The best systems combine robotic picking accuracy with flexible integration, affordable deployment models, and ROI you can truly show your boss without sweating.
And if you want one that’s affordable, install-ready, and not wrapped in layers of licensing fluff? Start here. 👇
Next steps with Standard Bots’ robotic solutions
RO1 by Standard Bots adapts to your floor like it’s been there since day one. From order picking to pallet stacking to bin handling, this six-axis cobot covers more ground than most ops teams, and actually delivers.
- Affordable and adaptable: Buy it for half the price of most six-axis robots, at a list price of $37K.
- Precision and power: With ±0.025 mm repeatability and an 18 kg payload, RO1 handles everything from picking and packing to welding, palletizing, and painting, without breaking stride.
- AI-driven simplicity: RO1 sees, adjusts, and runs in sync with your existing systems. No drama, no weeks-long setup.
- Safety-first design: Built-in vision and collision detection mean it works right next to your team without getting in the way.
Try RO1 with a 30-day on-site trial and see how much smoother your floor runs when your robot actually knows what it’s doing.
FAQs
1. What’s the best order picking robot in 2025?
If you want flexibility, AI, and the ability to do more than just pick bins, RO1 is it. It’s affordable, fast, and doesn’t need a warehouse redesign or an IQ of 190.
2. How much do automated picking robots cost?
Anywhere from $35K to $200K+ depending on how many bells, arms, sensors, and acronyms you’re adding.
3. Can order picking robots work with existing warehouse setups?
The good ones can. Look for robots that integrate with your WMS, don't require custom shelving, and can handle real-world mess, not just showroom floors. RO1 fits into most setups without triggering a remodel.
4. Are robotic order preparation systems worth it for smaller operations?
If you’re shipping more than a few hundred orders a day and your staff is sprinting laps around the shelves, yes. ROI isn’t just about speed, it’s about fewer errors, lower turnover, and way less mess.
5. Do order picking machines need constant reprogramming?
Not anymore. Modern systems use vision and AI to identify SKUs and adjust in real time. No more oversight about every product change or label shift. Which is great, because you have better things to do.
Join thousands of creators
receiving our weekly articles.